Ease of maintenance cited as a major advantage
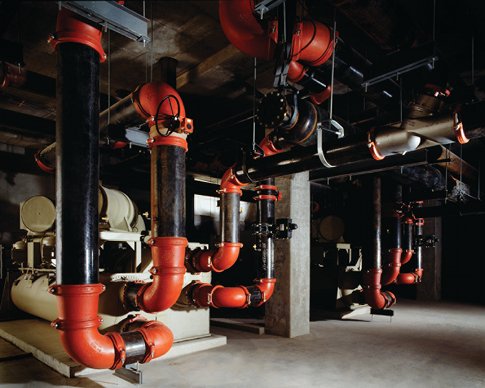
The importance of conducting regular maintenance in plant facilities is well documented, but when it comes to your mechanical system, why spend more time on maintenance than is necessary? For plant engineers, minimizing system shutdowns for maintenance is critical in order to maintain the plant’s bottom line.
Of all the pipe joining methods available, maintenance on HVAC systems installed using grooved piping products is the fastest, most efficient, and simplest to perform. They allow plant engineers to complete maintenance such as strainer/suction diffuser servicing quickly, and move onto other crucial tasks, such as equipment repair.
Consider the following when evaluating the best pipe joining method for your mechanical piping systems.
1. The design of grooved mechanical pipe joints makes them inherently easier to work with during maintenance activities.
In fact, grooved couplings, grooved fittings, and grooved components offer many benefits to the owner over the life of the system. Grooved mechanical systems reduce the need for maintenance overall, but when system service, alterations, or expansions become necessary, they provide a union at every pipe joint for quick and easy system access, reducing maintenance time and hence system downtime.
The ease of system access is created through the design of the grooved mechanical joint. The components of a grooved mechanical coupling include grooved-end pipe, coupling housing segments, an elastomer gasket, and bolts and nuts. The pipe is grooved by either a cold forming operation called roll grooving or machining a groove into the end of a pipe. The key sections of the coupling housings engage the groove.
The gasket is resilient, C-shaped, and pressure-responsive. The bolts, which hold the housing segments together, are tightened with a socket or impact wrench. In the installed state, the coupling housing encases the gasket and engages the groove around the circumference of the pipe to create a unified joint that provides a leak-tight seal in a fully self-restrained pipe joint.
A grooved mechanical joint is designed such that once installed and tested, it is maintenance free for the life of the system. The gaskets do not require periodic lubrication or replacement. The bolts and nuts will not loosen over time from being subjected to vibration from pumps or other equipment, or as a result of system thermal changes.
2. Grooved pipe joining systems attenuate vibration within the coupling, thereby eliminating the possibility of periodic product repair or replacement.
Flexible grooved couplings provide allowances for controlled pipe movement, including expansion, contraction, and deflection. This allows the flexible couplings to accommodate piping thermal movement, settlement, and seismic activity, as well as dampen noise and vibration generated by system equipment.
The design of flexible grooved couplings—in which the housing key section floats in the groove and the elastomer gasket is in full circumferential contact around both pipe ends and the housing interior diameter—results in a reduction of the noise and vibration being transmitted across the grooved joint, thereby localizing vibrations generated by equipment and reducing the amount of noise transmitted down the pipeline from pumps, chillers, and other components.
Flexible couplings are used for pump and equipment connections not only because of their vibration attenuation characteristics, but also because of their ability to accommodate piping misalignments and reduce stresses at the pump or equipment connections. Additionally, the use of flexible grooved couplings around equipment connections will eliminate the need for elastomeric arch-type connectors and braided flexible hoses, which can be long-term maintenance items for the facility owner.
3. A union at every joint allows for easy access to the system and flexibility for future system expansion.
One of the most notable design features of grooved mechanical systems is that the grooved coupling creates a union at every joint, providing easy access to the system. To access the system through a grooved mechanical coupling, a worker simply loosens two bolts and removes the coupling housing segments and gasket.
Removing two adjacent grooved couplings enables a section of pipe to be directly removed without the need for pushing or pulling adjacent piping or spreading the pipe ends at the joint. This makes required maintenance, such as cleaning strainers or suction diffusers, replacing corrupt pipe sections, removing equipment for repair, or slipping in a grooved tee to expand or join piping systems, much quicker and easier to accomplish.
“Flexible couplings are used for pump and equipment connections not only because of their vibration attenuation characteristics, but also because of their ability to accommodate piping misalignments and reduce stresses at the pump or equipment connections.” |
---|
To complete the job, the gasket is reinstalled, the grooved coupling is placed back on the pipe or grooved fitting, and the two bolts are re-tightened. Since grooved mechanical pipe joining systems simplify assembly and disassembly, they also require less labor and increase the speed of installation during maintenance, retrofitting, and expansion projects.
Serviceability in tight spaces is also easier and more time efficient with grooved systems because grooved couplings allow a full 360-degree rotation of the pipe and system components before tightening so that proper alignment can be achieved. In addition to routine maintenance, sometimes it is necessary to join two existing systems or reroute an existing system. With a union at every joint, a grooved system can be easily rerouted in retrofit projects.
The grooved system does not require torches. As a result, there is no need to dry the piping around the joint. Grooved couplings can be installed on wet lines, making it easier for the facility to return to full operating capacity quickly, without disrupting plant personnel.
4. Grooved piping increases safety during maintenance.
No flame or cutting equipment is necessary and no fumes are created during the assembly and disassembly of grooved mechanical piping systems, eliminating fire hazards. This is particularly important in areas of the plant where volatile chemicals and combustible materials are present. By eliminating flame, sparks, and fumes, grooved piping reduces risk to property as well as maintenance personnel.
In terms of speeding maintenance, the no-flame characteristic of grooved piping eliminates the need for a fire watch and jobsite preparation, such as ventilation, barriers, and signage.
Mechanical piping systems and their components must be properly maintained to maximize operating efficiency and equipment lifetime, but there are actions plant engineers can take to reduce system servicing and refocus limited maintenance hours on process-critical tasks. The selection of a grooved pipe-joining system is one of those actions.
Grooved piping offers the fastest, most efficient, and simplest access to piping systems among the number of pipe-joining methods available. The ease of installation, disassembly, and reinstallation makes grooved piping systems an efficient and effective way to reduce maintenance costs for mechanical systems.
David L. Hudson is a senior engineer for Victaulic Company, Inc. He is a practicing mechanical engineer with 31 years of experience. He can be reached at [email protected].