Systems integrator supports seizing of a supply chain opportunity
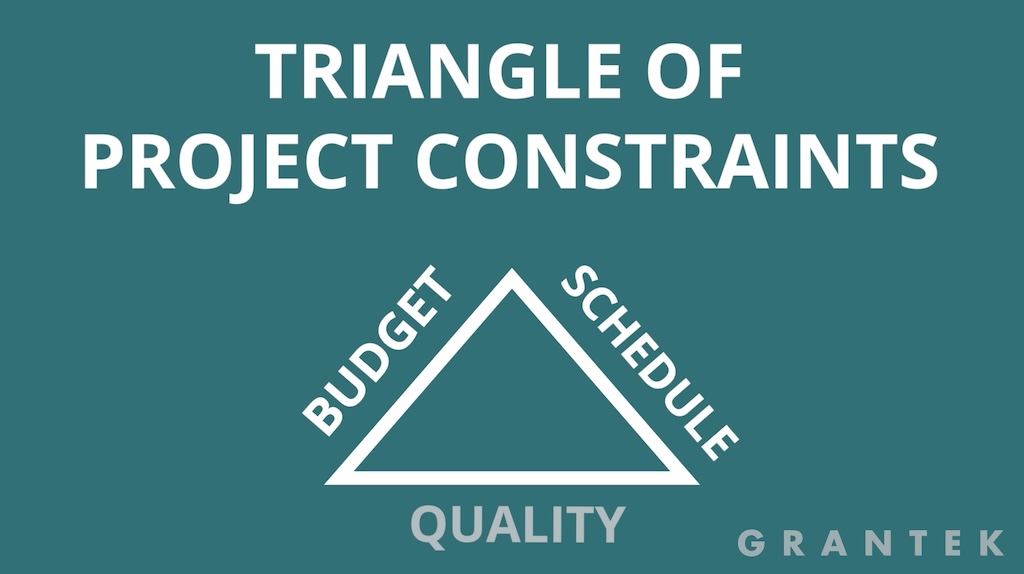
Supply chain insights
- In response to supply chain challenges, Grantek established proactive strategies, leveraging networks and early planning to expedite project delivery.
- Grantek’s collaboration with a pharmaceutical company showcases successful implementation of an advanced alarm management system for improved efficiency and compliance.
As we enter 2024, let’s look back to the onset of the supply chain issues brought on by the COVID-19 pandemic.
Here at Grantek, we established best practices to mitigate supply chain issues that were delaying already approved integration and automation projects from proceeding due to lack of available hardware. Grantek is a manufacturing business consultant and system integrator in business since 1980 and that today has a presence across North America and nine global offices.
Establishing these best practices allowed Grantek to “seize the opportunity” and deliver solutions for our pharmaceutical and food & beverage manufacturing clients. One of these solutions is outlined below.
First, let’s review some of the processes and procedures goods producers can put in place to ensure project completion continuity for clients. The “Supply Chain Risk Mitigation Best Practices” detailed below outline some steps Grantek recommends to help clients protect themselves against uncertain, unstable supply chains. These steps won’t guarantee prompt hardware delivery, but they will help put projects in the best position to be delivered as close to schedule as possible.
In the last few years, many conversations Grantek had with clients concerned hardware procurement and supply chain issues the manufacturing industry is facing.
In early 2020, common automation and controls hardware had typical lead times of around two to three weeks in most cases. For some specialty items, lead times might creep upwards of a couple of months.
Since 2021 it’s been a completely different story. Countless devices, across almost all suppliers — including variable frequency drives, I/O modules, programmable controllers and network switches — are involved. Even something as simple as a contact block can see lead times of four to six months.
The one question we get from almost everyone is, “How can we expedite things?”
How can we expedite?
To start, an understanding of the triangle of project constraints is important (See figure 1). The three sides of the triangle equate to budget, schedule and quality. The general rule of thumb is that you can’t impact one without adjusting the others.
In most cases, that means if a project is subject to schedule overruns, a typical response is to spend more on resourcing or overtime to speed things up. However, hardware lead times are different. For required components, if no stock is available, paying more won’t improve the delivery date.
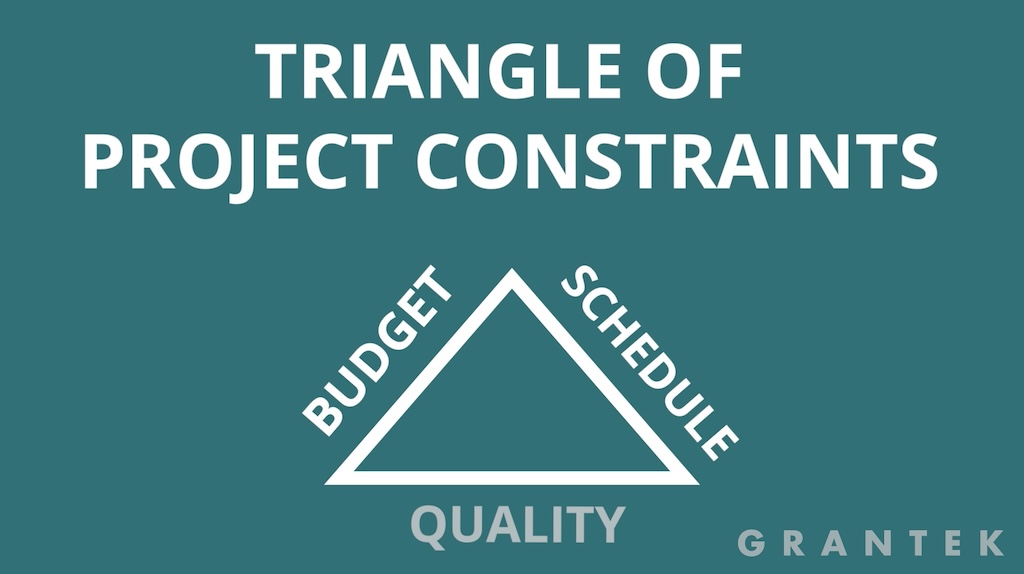
However, things that can be done to reduce project risk associated with long-lead items. Having a high-level design in place as early as possible allows identification of key component and lead-time determinations, as well as ordering of long lead items. This is the best way to keep a project on schedule. The earlier the order is placed, the earlier the hardware is available for installation.
Use of preliminary electrical-design services gets major controls components defined and ordered. Spending a little budget up front reduces costs of the remaining effort and streamlines the procurement phase.
Not all project timelines allow for sufficient up-front engineering effort. And often, timeline constraints are so tight that even when hardware is ordered well in advance, lead times still cause issues. To help clients through this, Grantek leverages a few different things:
First is our distribution network. With over 40 years of relationships, Grantek has a wide network of distributors we leverage to get needed hardware. Many distributors have different levels of stock on hand across the continent.
Second is a predictive procurement strategy. This includes analysis of all our projects to identify common components, lead times, installation dates and volume orders. This increases the stock available at any given time. A large volume of automation hardware that often be shifted around to meet client needs, without impacting other project schedules.
Third is overall industry experience and familiarity with hardware options across many different platforms. This allows specification of alternative hardware options (both within the same brand or different brands if acceptable).
These alternatives greatly reduce lead time while having a minimal impact on design rework and no impact on system functionality.
Don’t forget this
A final point doesn’t directly pertain to project execution, but rather facility maintenance and general operations.
If there are doubts as to whether a facility is carrying adequate spares of critical components, that’s a problem. When lead times are less than a week, this may not be a huge risk; however, with months-long lead times today for common devices, if production critical hardware fails, down times may be longer than anticipated.
Critical spare assessments typically include a comprehensive on-site review of the facility’s control system to generate an asset list. This asset list can then be compared with spare parts available. A gap analysis is developed, with a suggested procurement list for at-risk hardware to consider ordering now, before anything fails.
This not only prepares for worst case scenarios, but also identifies obsolete hardware and supports developing a modernization roadmap for manufacturing sites.
Real-life example
A leading pharmaceutical manufacturing company recognized the need for an advanced alarm management system to ensure efficient monitoring and compliance with regulatory requirements. The company asked Grantek to design and implement automation based on Inductive Automation’s Ignition SCADA platform to streamline alarm management and improve overall productivity.
The company required an alarm management system capable of handling various alarm data from existing Siemens PLCs and OPC tags for multiple systems on site. The system needed to allow users to enter comments for each active alarm, work in conjunction with Windows Active Directory, create user profiles, and generate filterable reports. The solution had to comply with the stringent regulations of the pharmaceutical manufacturing industry. Some of the challenging requirements involved included the following:
-
Integration with existing Matrikon OPC Server and Siemens controllers
-
Ensuring all levels of alarm management for configured tags and meta data type options
-
A user-friendly interface for operators and managers
-
Customizable and filterable reporting features.
Grantek recommended Ignition by Inductive Automation as the SCADA system for this project. The Ignition Perspective application connected to 22,000 tags and 11,000 alarm points while offering a future pathway to connect 96 new Allen Bradley PLCs directly to the gateway. A user-friendly real-time alarm management workflow was developed, along with high-density alarm summary and alarm history views for advanced filtering.
The result delivers
The implemented solution allowed for well-defined alarm management, handling up to 10,000 alarm events per day. Administrators perform in-depth configuration updates and add new alarms through the front end of the application. Additional features include automatic notifications, report distribution, and a high-availability database architecture for historical retention of alarm information.
The custom data archiving and report schedule builder ensured smooth operations and regulatory compliance. The UI tools provided flexibility for users to manage points, request changes, and track progress. Grantek’s solution also offered AD integration and workflow for system administrators to approve or deny new users or role changes.
By collaborating with an expert system integrator, the pharmaceutical manufacturing company seized the opportunity to improve its alarm management system, streamline processes, and ensure regulatory compliance. Partnering with systems integrators to design, test, connect, implement, and upgrade automated systems enhances productivity and efficiency in the industrial value chain.
Fast fact
The pharmaceutical supply chain faces challenges that include supply chain visibility, drug counterfeiting, cold-chain shipping and rising prescription drug prices, according to Pharma News Intelligence.