Breathe new life into old switchgear with modernization and see the benefits of improved reliability and safety

Learning Objectives
- Explore challenges with maintaining legacy switchgear.
- Learn how equipment maintenance plans can enhance electrical safety.
- Learn the impact of modernization and digitalization to enhance optimization and effectiveness of equipment maintenance plans.
Electrical safety insights
- Switchgear modernization and monitoring enhance reliability, safety and cost-effectiveness by optimizing equipment maintenance plans, surpassing traditional reactive and preventive practices that can compromise performance.
- Effective maintenance plans (EMPs) should integrate NFPA standards, manufacturer recommendations and modernization strategies to address challenges like part obsolescence, expertise gaps and sustainability concerns, ensuring long-term reliability and safety.
Reliability and safety are critical topics when it comes to optimization of switchgear asset performance and life cycle. Today’s business asset managers face economic limitations that require deeper analysis to prioritize investment needs. In many cases, traditional practices, such as reactive and even preventive maintenance, may appear to be the most cost-effective solutions; however, in practice, they may compromise performance targets for reliability and safety, leading to economic setbacks in downtime and overall operational cost.
Conversely, switchgear modernization and monitoring can support equipment maintenance practices that lead to robust performance and life-cycle extension of the equipment. Through modernization and digitalization of their equipment, asset managers can optimize their equipment maintenance plans (EMP) for a more reliable, safer and more cost-effective result.
Evolving maintenance needs
Designing and implementing effective EMPs is critical. A robust EMP requires consideration of many factors including, but not limited to:
-
NFPA 70B: Standard for Electrical Equipment Maintenance and NFPA 70E: Standard for Electrical Safety in the Workplace
-
Manufacturer recommendations.
-
System conditions.
-
Workforce availability.
-
Outage restrictions.
-
Budget constraints.
Maintenance plans are complex to build and require continuous improvements as the processes and methodologies are implemented. Lessons learned on a continuous basis must be implemented to ensure the maintenance plan is set up for success. All of these considerations help ensure that the safety of personnel and assets always takes top priority.
With today’s pressure-cooker economic environment, having an EMP with traditional practices is not enough, particularly with aging assets. Assessing the long-term viability of maintaining legacy switchgear involves evaluating factors such as equipment reliability, performance and operational needs against the cost of ongoing maintenance and potential risks.
Developing a strategic asset management plan that considers life cycle costs, risk mitigation strategies and technology trends is essential for informed decision-making. There are five major challenges:
-
Obsolescence of parts/equipment
Legacy equipment often contains parts/accessories that are no longer manufactured or available in a reasonable timeframe. Sourcing these items becomes a supply chain nightmare due to higher costs and longer lead times, potentially leading to extended downtime to maintain, if even possible. From an inventory management aspect, more parts must be stocked to reduce risks of higher lead times and limited availability, adding more costs to maintenance budgets.
-
Lack of technical documentation
Legacy equipment may lack comprehensive documentation, including maintenance manuals, schematics and operating instructions. This lack of documentation complicates troubleshooting, diagnosis and repair efforts, requiring maintenance personnel to rely on their experience and knowledge of the equipment.
-
Expertise gap
Maintaining legacy equipment requires specialized expertise that is scarce in the labor pool. As experienced professionals retire, their tribal knowledge also retires. This leads to gaps in the maintenance capabilities of the next generation of labor.
-
Reliability and safety
Aging switchgear generally undergoes a gradual decrease in reliability, causing unexpected downtime and failures. In addition, electrical safety codes and standards evolve over time. While in most cases these do not mandate replacement of legacy equipment, ensuring maximum safety of personnel and equipment becomes increasingly difficult with older switchgear that was not built to comply with today’s codes and standards.
-
Sustainability and environmental impact
As organizations globally focus on sustainability, much emphasis is placed on reducing carbon footprints. Legacy assets can contribute to a higher footprint due to increased maintenance requirements and waste generation among other issues.
Many older switchgear components use insulating material such as SF6 gas and oil. SF6 gas is a potent greenhouse gas. The European Union is already moving toward legislation to have electrical equipment SF6-free as early as 2026 for voltage levels to 24 kilovolts (kV), and by 2030 for up to 52 kV (some exceptions apply to installed products).
Legacy switchgear is also known to contain hazardous materials such as lead, asbestos, mercury and cadmium, posing significant risks to personnel and the environment. End-of-life services for equipment containing such materials must be carried out by licensed waste management organizations as determined by relevant regulatory authorities.

Considering the factors outlined above, an effective EMP must include consideration for a mix of modernization plans to enhance the impact of maintenance toward safety and reliability. From an economic standpoint, the cost of maintaining legacy equipment can be substantial, encompassing expenses related to spare parts, repairs and downtime (see Figure 1).
Modernization strategies help achieve safety goals
Switching devices are the switchgear components most impacted by electrical and mechanical aging. Effective modernization strategies focus on techniques that enhance technology and maximize value of the maintenance and asset management process. Consider three key modernization strategies:
-
Hard bus retrofill
A hard bus retrofill solution involves a standard cradle/fixed part hosted inside the legacy panel. The cradle consists of a standard, fully tested compartment with all new interlocks and shutter mechanism, as per the latest applicable standards interfacing with the existing switchgear. These solutions use standard withdrawable circuit breakers, offering vacuum interrupter technology and options for spring-charged energy storage mechanism or magnetic-actuation mechanism.
Some manufacturers also offer motorized racking options with the new circuit breakers, providing enhanced arc flash safety for the operators. This technique renews main functional components of the original switchgear. The installation process requires significant modification to the panel to accommodate the new apparatus as well as new secondary wiring.
-
Cradle-in-cradle solution
The cradle-in-cradle solution has the new cradle/fixed part hosted inside the legacy panel. The fixed cradle is designed to connect to the fixed part of the legacy panel in the same manner as the moving part of the legacy circuit breaker — although as a fixed installation. The other fixed part uses standard components to accept a standard withdrawable breaker. The two fixed parts make one single assembly.
Like the hard bus retrofill, the cradle consists of standard compartment features such as new interlocks and shutter systems. These solutions use standard withdrawable circuit breakers as well. The installation process requires moderate modification to the panel to accommodate the new apparatus as well as new secondary wiring.
-
Direct replacement/roll-in-replacement
Direct replacement solutions are engineered to match the original switching apparatus. The base breaker module used is a new standard fixed breaker based on the latest technology. It mounts on a truck that matches all interfaces in the existing panel (racking positions, shutter opening interfaces, interlocks, ground connection and so forth).
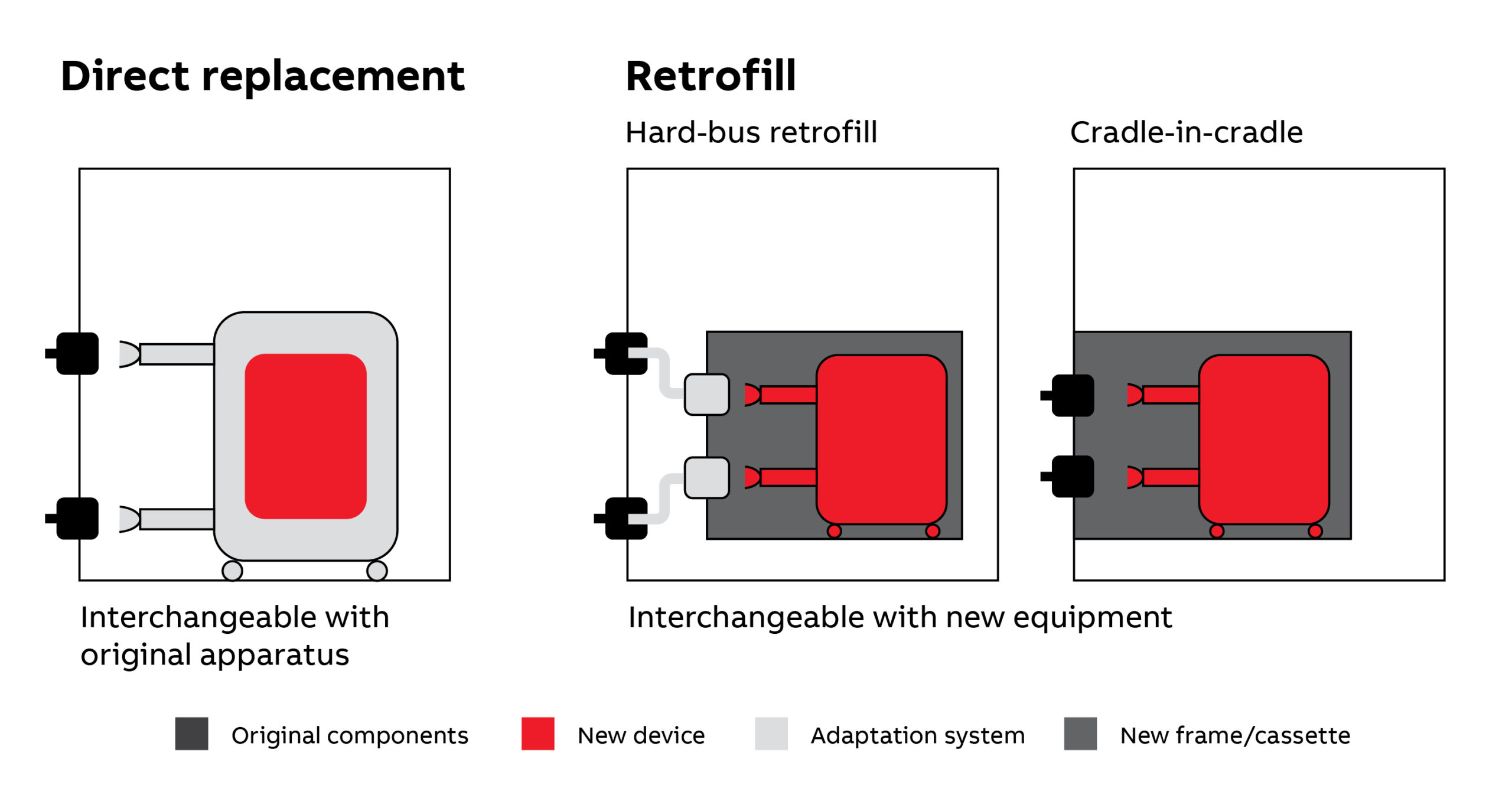
This solution is the most complex to design among the modernization techniques discussed because it requires in-depth knowledge of the existing legacy equipment to develop a new direct-replacement solution matching the fit, form and function of the legacy circuit breaker (see Figure 2). This solution does not require modification to the panel, and the secondary disconnect matches that of the existing equipment, eliminating wiring changes and requiring the least downtime to install.
Condition monitoring for safety and reliability
With these modernization techniques, advanced monitoring and diagnostics (M&D) can be applied as part of a modernization strategy, adding value to the maintenance plan. M&D systems provide detailed insights into the operation, condition and performance of the switchgear asset. These features enhance reliability, safety and efficiency by enabling condition-based proactive maintenance, early anomaly detection and faster fault resolution.
The M&D system collects condition monitoring data from various sources, including relays and sensors. It then processes this data using advanced algorithms to compute key performance indicators (KPIs), which describe the health status of monitored assets. Following are the key components of advanced M&D:
Circuit breaker diagnostics: The M&D system monitors circuit breakers by retrieving key performance data from numerical protection relays. Examples of monitored data include:
-
Opening and closing times.
-
Slipping and failed spring-charging attempts.
-
Inactivity days.
-
Remaining life estimation.
-
Trip coil supervision.
The monitored parameters help detect electrical or mechanical abnormalities that can lead to a circuit breaker failure.
Partial discharge monitoring: Throughout the industry, multiple methods are used to detect partial discharge (PD). For example, in the UHF technique, antennas detect PD activity and can be localized to the specific compartment. Another method involves the use of capacitive couplers to detect PD events on the three different phases and synchronize those events with power line voltage.
Early detection of PD patterns can help prevent arc flash and catastrophic equipment failures.
Temperature monitoring: In temperature monitoring, sensors detect real-time values in key locations, including bus bar joints, cables and circuit breakers. Installation of these sensors requires no modification to existing switchgear, and absolute and delta temperature readings can be used to monitor critical situations.
Temperature monitoring enables quicker detection of loose joints, insulation degradation, load unbalancing and other thermal failures than traditional methods, such as infrared (IR) thermal scanning. It also enhances safety by eliminating the need for site operators to perform IR scanning on live equipment.
Maintenance optimization to meet safety KPIs
Advanced M&D systems make it possible to access all critical KPIs remotely and send them to the control room. This enhances data visualization and asset management by providing real-time dashboards, trend analysis and status indicators. Centralized data collection enables predictive analytics for fault prediction and calculates health indices to prioritize maintenance. This results in optimized maintenance scheduling, improved resource allocation and enhanced switchgear reliability and safety. Artificial intelligence will play a larger role in the future to make algorithms smarter and more accurate, increasing the impact even more.
In a data center example, implementation of M&D systems reduced the amount of time required for routine maintenance and increased the time interval of maintenance by 30%. This was achieved by reducing maintenance tasks required for a three-year maintenance plan due to availability of real-time data replacing manual inspections, making operations leaner and eliminating safety risks during unnecessary inspections.
Repair/overhaul optimization by design
Older circuit breakers require maintenance at very short intervals due to aging to function properly and to avoid unforeseen downtime. Vacuum interrupters used in modern medium-voltage breakers require significantly less maintenance and offer clean, quiet operation compared to air magnetic breakers with arc chutes. Contacts used in the vacuum interrupters are designed to reduce arcing time and contact wear with good surface behavior.
Additionally, modern circuit breakers offer a simpler operating mechanism with fewer parts requiring maintenance. Spring tension and associated operating speed is not a concern. The breakers can be equipped with a magnetic actuation mechanism for medium voltage and compact modular structures for low voltage, both of which have few moving parts, reducing maintenance needs. Operating personnel can be trained on the newer equipment, increasing maintenance capabilities and expertise.
Stock parts management
Original manufacturer replacement parts for vintage circuit breakers are scarce. The used equipment market may no longer be able to supply dependable parts due to the aging of refurbished or used components, which can compromise reliability. Even if these parts are available, the lead times and costs are high.
In contrast, modern circuit breakers are often designed with standardized components, making it easier to find compatible spare parts across different models supported by the manufacturer — with significantly lower lead times and costs.
Operational safety by design
As mentioned, legacy circuit breakers may contain hazardous materials. For example, older circuit breakers contain arc chutes with asbestos. These materials are liabilities for the environment as well as a safety threat to personnel. The arc chutes are also known to be heavy, requiring removal before a safe and thorough inspection. New breakers do not contain hazardous materials, making operation and maintenance tasks easier, safer and more efficient.
Furthermore, changes in the power system over the years can expose equipment to higher fault levels and cause it to run closer to operational ratings, leading to equipment failure. With modernization, equipment can be upgraded to higher ratings as required by its current operational landscape.
Creating an effective maintenance plan is a complex endeavor and requires thorough planning and consideration. Modernization and upgrade of switchgear assets optimize EMPs, helping organizations achieve significant improvements in maintenance efficiency and system performance, ultimately ensuring a resilient and dependable electrical infrastructure, minimized downtime and safer operations.