Technology update: Digitalization was are among key trends for manufacturing and process facilities highlighted in the media session at ARC Forum 2019.
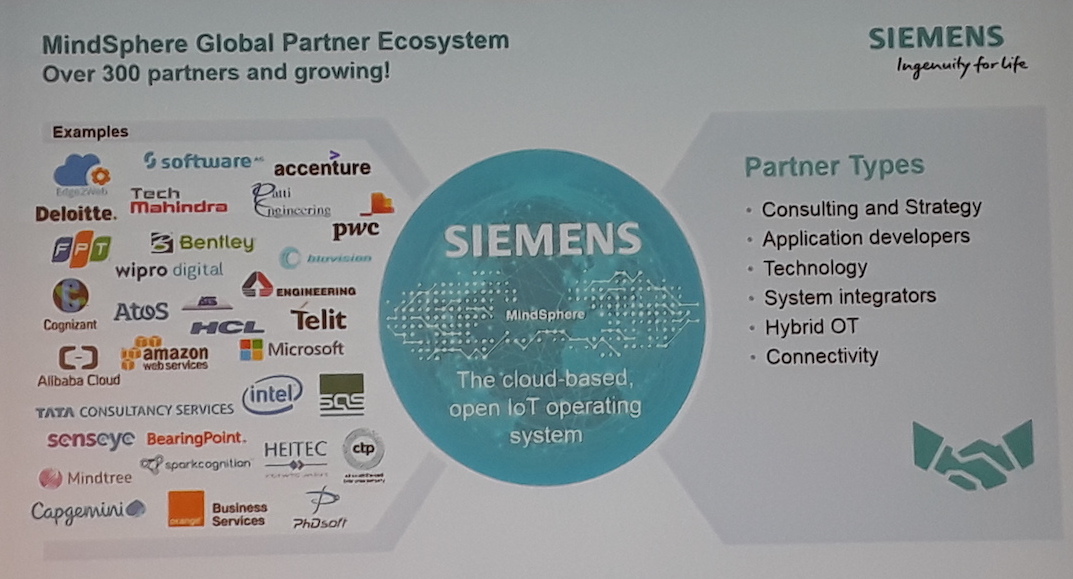
Manufacturing and process facilities are taking advantage of trends in digitalization to make applications more efficient, effective, secure, with lower risk, greater profitability, and more flexibility. Highlights from 2019 ARC Forum media meetings below reflect trends driving new product announcements.
Digital twins: Bentley
Greg Bentley, CEO of Bentley Systems, discussed the benefits of a digital twin cloud service developed jointly with Siemens. The service is designed to enable up-to-date, as-operated digital twins that synchronize the real plant and its engineering representations to make process plant operations more efficient.
During one construction project, Bentley said, drones were flown weekly to create 3-D project models, preserving information for future use (such as where buried utilities are located), creating more than 3 million tags, connecting databases with schematics and piping and instrumentation diagrams (P&IDs) to reduce time for the project and reducing risk, Bentley said.
Engineering design tools for plant infrastructures and building information modeling can create an immersive experience in virtual reality for training or better locate hidden utilities for smarter, more effective maintenance or upgrades in the future. Services software brings together physical and virtual so the as designed, as built and as operated versions reflect current reality.
Cloud services digitally connects components and workflows. An implementation can:
- Use 3-D reality mesh to find 2-D images of components to be identified.
- Train the software by creating bounding boxes around components and add classifications.
- Run a detector on 3-D reality mesh to locate and classify changes to components and systems.
- Use a browser application to highlight classified components in a reality mesh.
Each iteration applies knowledge and advances the model integrating a cost, schedule, and safety index. Rules can be created and applied as needed, Bentley said. (For instance, were the same grade of materials used?)
Cloud application, digitalization tools: Siemens
Bill Boswell, Siemens vice president of marketing for cloud application solutions – MindSphere, covered how infrastructure can leverage the Industrial Internet of Things (IIoT) using a cloud-based, open IoT operating system.
Technologies such as smart meters have shown how digital technologies save time and add value and functionality in utility applications. Getting started with digitalization, Boswell said, is often easier with a digital maturity model and horizontal industry technologies for specific customer needs. The ability to connect and monitor, analyze and predict, digitalize and transform integrates IoT data and other information into the plant and product lifecycle.
The concept of creating a digital twin can be applied to products, productions, and performance.
In a collaboration platform, applications, an open platform as a service (PaaS), and connectivity with edge products—computing power, distributed control, analysis, and communications distributed close to the process.
Software development tools, application program interfaces (APIs), and libraries can speed development, simplify programming, device linking with IoT extensions, and integration with other systems, including enterprise-level software, Boswell said.
API versioning allows backward compatibility, and software can access and work with multiple cloud-based systems, he said. Siemens’ acquisition of Mendix low-code software helps reduce programming time by 10 times by using model-driven development for visual modeling.
Digital transformation: GE
Matt Wells, GE Digital vice president of product management said software products today can provide new capabilities and insights with automation, manufacturing execution systems (MES), and historian software. Cloud capabilities can provide greater insights, across many sites and processes, than more traditional implementations, all adding productivity and reducing downtime. Such software can speed up actions on real-time data to improve efficiency and reduce costs.
In 2018, GE announced plans to create a new independent company, GE Digital, putting its power, digital, and grid software businesses together into one company with $1.2 billion in annual revenue, to help serve GE verticals and other customers with advanced automation, manufacturing execution software (MES), and historian software.
Wells said software should offer customers simple accessible options to achieve their digital transformation journey.
Mark T. Hoske is content manager, Control Engineering, CFE Media, [email protected].
KEYWORDS: Digitalization, automation
ARC Forum 2019 included manufacturing and process trends.
Digitalization is among the key trends impacting manufacturing.
An up to date model of the facility provides opportunities for savings.
CONSIDER THIS
Are you integrating new designs and technologies quickly enough to accelerate faster than your competitors?