Lift truck fleet management is as much about the management as the vehicles in the fleet. Pat DeSutter, the director of fleet management at NACCO Materials Handling Group, Inc. offers 10 ways to get your fleet aligned with your strategic needs.
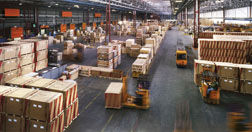
Lift truck fleet management is as much about the management as the vehicles in the fleet. Pat DeSutter, the director of fleet management at NACCO Materials Handling Group, Inc. offers 10 ways to get your fleet aligned with your strategic needs:
1. Understand your asset mix: Short-term rentals that are kept for extended periods can be a sign that you are over-spending and may need to invest in additional equipment.
2. Seek out opportunities to consolidate service providers: Most large material handling service providers are capable and qualified to work on multiple types and makes of assets. Rationalizing service providers can help leverage your purchasing power, gain more consistency and reduce costs through actions such as consolidated service calls, etc.
3. Establish an enterprise-wide mindset when it comes to fleet optimization: Consider shifting assets from site to site where practical to balance equipment utilization. This will improve uptime, help to compress maintenance spend and ensure optimized value and usefulness of the asset for its full economic life.
4. Implement a dynamic replacement program: A sound replacement program identifies the specific break-even point where the maintenance costs of the asset exceed the ownership costs. This is when it is more economical to replace the asset. Numerous factors drive this decision including the severity of the application, rate of usage, type of truck and the type of maintenance it receives.
5. Have a maintenance program in place: At a minimum, you should have a periodic maintenance program established that ensures that all critical areas of the truck are maintained to manufacturer recommendations and specifications.
6. Know your maintenance costs: You cannot manage what you do not measure. Having good baseline data is the first step toward understanding your real maintenance costs at the asset level, which enables you to set specific goals for cost reduction.
7. Leverage technology where practical: Telemetry solutions are more affordable than ever. While there are upfront costs involved, the simplest of solutions can track true utilization in real time, help you manage operator accountability and provide accurate data to monitor maintenance spend.
8. Don’t turn a blind eye to avoidable damage: Avoidable damage associated with operator abuse can be as much as 40% of the total cost to maintain the lift truck. Use of maintenance tracking software and telemetry will provide the insights needed to attack and reduce this cost. An operator training program or review of processes will reveal corrective action opportunities to reduce these costs.
9. Aged assets and downtime: Not only will the maintenance spend increase as the asset ages, but factors such as parts obsolescence and increased opportunity for major repairs can contribute to significant downtime resulting in lost productivity. This is often overlooked.
10. Consider partnering for competitive advantage: Consider enlisting the services of a quality fleet management partner. A provider can work as an extension of your operation to address and provide recommendations for each of these areas. Additionally, a quality fleet management provider can perform work order review and assessment, as well as help you compress administrative costs through providing centralized service call management and invoicing, among other services.