There are many choices to assemble the right supply chain solution.
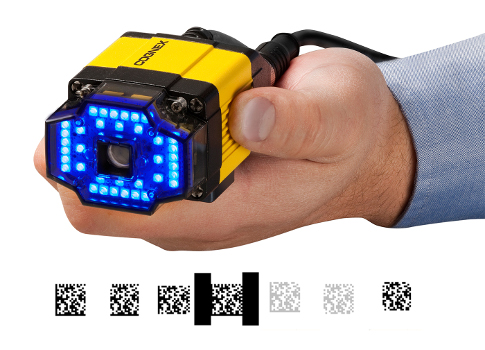
For manufacturers, effective inventory management is a key piece of supply chain efficiency and accuracy. Yet, with numerous solutions on the market, evolving technology, and increased emphasis on running “lean,” plant managers and materials handling professionals face the challenge of determining which inventory management method to implement.
From a very basic level, there are three chief methods of managing and controlling inventory. The first and most rudimentary method is manual data entry (essentially, pencil and paper), while the other two—barcodes and RFID (radio frequency identification)—involve automated data capture technologies.
But, before we dive into each of these methods, we need to take a step back. With so many new and exciting technologies on the market, it is easy to get wrapped up in a trend and say something like, “RFID is the latest and greatest way to track our inventory, so I’m going to put RFID tags on all of my products.” Force-fitting a solution just because it sounds like a viable option, or because everyone else is using it, is a detrimental idea.
Before you purchase a new infrastructure, stick on a barcode label, or sharpen a fresh box of No. 2 pencils, you often need to start at the very beginning. It is vital that you first perform an operational assessment or process review to define your business objectives and identify exactly what you are trying to achieve.
Perform an operational assessment
In performing your operational assessment, you must look at three pieces of the puzzle: process, people, and technology. Think of these pieces as a three-legged stool. All three are of equal importance to your overall operation. So, if your process is defective (for example, you have multiple touch points for outbound transactions, like separate packing and shipping stations), implementing a piece of technology will not fix it and will only reinforce the existing poor practices in your supply chain.
Also, while you are observing your processes, make sure to pinpoint any steps that are superfluous. If a process does not add value to your intended end result, remove it. Your customer only cares about receiving the order in a timely and accurate manner, so all other steps in the process are just “noise” to the customer. The steps you take should ensure proper delivery.
Next, consider your people. If you are going to end up introducing new technology to your process, like adding barcode scanning to your process for taking inventory levels, you need buy-in from not only upper management, but those who will be using the technology. Getting everyone on the same page, giving them a voice, and demonstrating why you are introducing these changes will position you for a successful implementation.
Once you have an understanding of your problem and your business goals, you can begin to look at the technology to support your efforts.
Pencil and paper
Despite the breadth of technology available today, some manufacturers still manually manage their inventory with pencil and paper, and then input data into Excel spreadsheets. Manual systems are typically used by organizations that have a smaller footprint.
These manufacturers have smaller facilities (perhaps a single parts room), fewer SKUs, and lower IT budgets, so manual data entry is sufficient. Of course, manual methods open up a greater possibility for human error, and backend data entry can be extremely time consuming and tedious. There is no way of knowing how much inventory is on hand at any given time, where it is, and whether you are picking the right item. There is little to no visibility into inventory levels and materials’ movement, placing greater pressure on employees to operate as accurately and efficiently as possible.
Barcodes
Barcodes were a major step up from manual systems, and with many options and price ranges, even the smallest organization could implement some kind of barcode system. The greatest advantage of a barcode system is that everything tagged has a unique identification number. With 2-dimensional (2-D) tags, it is possible to embed additional information specific to that item (serial number, lot number, production date, etc. ). When the barcode is scanned, the embedded data ties back into a backend systems and other databases to help the manufacturer keep accurate tabs on inventory, improve visibility and create a chain of custody throughout the manufacturing lifecycle.
Obviously, barcodes reduce the need for manual data entry, therefore, increasing productivity and accuracy. The main downside to barcode systems is that they require a line of sight—someone must still aim the scanner at the code, within a certain distance, to obtain a reading.
RFID
RFID has picked up speed as the automated data collection tool of choice for many manufacturers. RFID holds many of the same benefits as barcodes, but does not require a line of sight or human intervention. RFID tags also can hold much more detailed information than barcodes,have a typical read range of 10-20 feet, and can be read at high speeds (800 tags per minute). However, RFID tags are more expensive than barcodes (although their costs have come down in recent years), but they are reusable.
There are two types of RFID tags: passive and active. Each have very specific use cases in the manufacturing world. Which type you use depends on the type of asset you are tracking. Passive RFID tags rely on readers to pick up their signal in order to supply the power for broadcasting data. Passive tags are used for tracking hundreds or thousands of smaller parts with a standardized material flow. These items exist within an area where chokepoint or gateway detection and a limited read range are adequate. For example, instead of tagging hundreds of individual bolts, an automobile engine manufacturer would affix a passive tag to the bin that holds these bolts. This allows the manufacturer to track the bin’s movement through various touch points.
On the other hand, active RFID tags draw from their own power supply to transmit signals that provide real-time location data. Therefore, active tags are best suited for tracking larger, high-value assets that have a varied material flow. A good use case for active RFID is to tag engines as they are assembled throughout the plant. From a software interface, manufacturers can see where each engine is located and how many they have within the facility at any time.
Creating a solution
One single method may not be the answer. More often than not, organizations find that there is nocookie-cutter solution. Some manufacturers require a hybrid solution.
For instance, after a thorough process review, you might find that a combination of passive and active RFID is your best bet, since you are tracking both high-value and high-volume assets. Or, you may incorporate a mix of barcodes and RFID, or barcodes and manual data entry. There are endless possibilities.
Just remember: no matter which solution or blend of solutions you select, everything begins at the top. Throw the technology out the window until you hone in on the problem at hand and identify a roadmap that will best solve it. Then, you’ll be on track to effectively utilize the solution to improve your overall accuracy, efficiency, and connectivity throughout your inventory and materials handling processes.
Chase Sowden is supply chain architect for Barcoding, Inc. (www.barcoding.com).