Navigating site viability to meet multi-stakeholder goals requires clearly articulating needs and requirements.
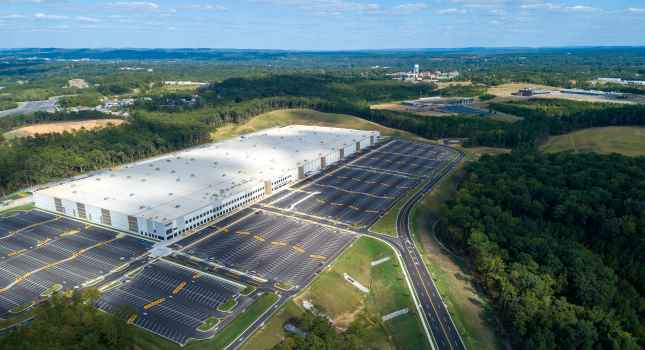
Environmental Health Insights
- Choosing a site for a new company comes with plenty of tasks to ensure that the location is a good fit for the company.
- It is important to understand the impact of NDAs, research local utility capacity, investigate environmental impacts and consider the people factor when selecting a site location for a company.
Site selection for a new corporate headquarters, distribution facility or manufacturing plant can be a daunting task for stakeholders, selection teams and end users.
The process poses a series of challenges and requires navigating many different levels and sources of information. A well-organized site selection process can provide an efficient, and more competitive, process among the different communities while minimizing operating costs and risk. Here are key challenges, insights and solutions to ensure a successful site selection strategy that strikes the right balance between granular data and strategic goals.
Understand the impact of NDAs
Recognizing that confidentiality is a critical factor in selecting a new site, Non-Disclosure Agreements (NDAs) are standard protocols for all parties involved in the site selection process.
However, be aware that the strict parameters of NDAs can constrain the process unnecessarily. Due to fears of information leaks, often only generalized information is shared, resulting in insufficient information regarding utility needs, building configurations, employee counts, the daily number of trucks, required trailer storage, etc. Having an appropriate level of detail allows site selection consultants and engineers to accurately evaluate potential locations.
To ultimately select an optimal site, vital information must be shared from all involved parties to execute and even accelerate the process. With speed to market being a critical factor in today’s environment, it is a given that site selection has become more time-sensitive and, as businesses react to ever-changing markets, site selection “inner circles” are more willing to share information on the front end to keep the process moving in an effort to avoid mistakes and costly delays.
Navigating site viability to meet multi-stakeholder goals requires clearly articulating specific needs and requirements, and making communication the key to success. Even though parameters are fluid from stakeholder to stakeholder, consensus regarding the crucial parameters and significant priorities is important.
These include the breadth and depth of the overall project, such as utility needs and required capacity on water and sewage, available capacity of power and gas, accessibility (road and rail), required speed to market (how fast the project needs to move to completion), site constraints/configurations, and the nature of the facility. A clear and concise project understanding is crucial for the site selection process.

Research local utility capacity
A key priority in site selection for a manufacturing facility is how a specific site can accommodate industrial discharge.
While the manufacturer may pre-treat the discharge, the local sewage receiving entity must have sufficient average daily flows for dilution and capacity to process the additional discharge. This means the size and the capacity of the sewage treatment, along with the line travel distance from the plant, are critical points to ensure that the local POTW’s infrastructure and treatment facility won’t be negatively impacted by and can the discharge from the process stream.
The end-user can always treat more before they discharge, but in seeking to minimize the infrastructure costs on their processes, they often push the limits with the receiving utility. In turn, the receiving utility doesn’t want to take on more risk of an environmental failure because state and federal agencies will cite them should a failure result due to discharge from the manufacturer. The utility is seeking to balance a revenue stream from the industry, help the local area attract the manufacturer to their community, while minimizing any risk of an environmental failure. Research must be conducted into capacities and the calculations must be accurate for both the discharge from the manufacturer and the processing capacity from the utility and the challenge is synthesizing the two.
Investigate environmental impacts
Local environmental constraints can pose significant challenges, particularly if a US Army Corps of Engineers permit is required or the project is federally funded.
The needed documentation is complex and local environmental codes can conflict with or supersede federal codes. Local politics often come into play and local codes are often waived, especially when multiple communities are vying for a project. While most cities and municipalities will make accommodations for large industries, not all do, making the understanding of state and local permitting processes and approvals crucial. Remember to review corporate environmental ethics statements, as they can influence the site selection process.
Tax implications are another example of a parameter that is a factor as corporate tax structures can affect site selection. Though it doesn’t impact making the project work on the potential property, it can be a significant consideration for the end-user especially when some municipalities charge taxes on stock stored for a lengthy period of time in their facility. Â
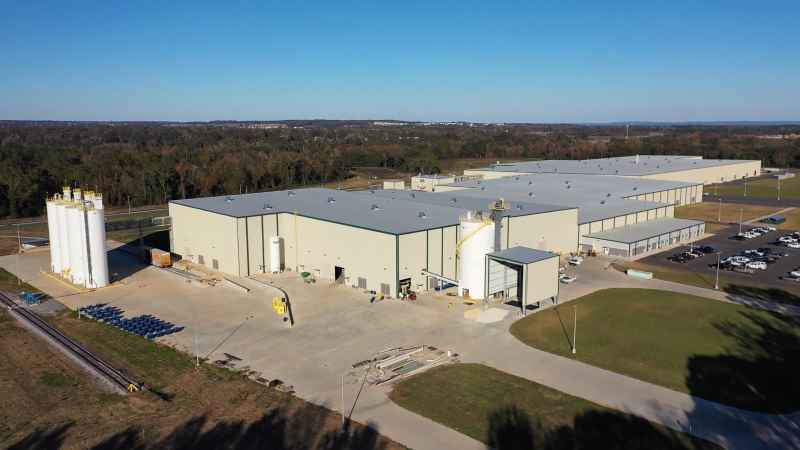
Consider the people factor
While access/delivery of raw materials and distribution capabilities of finished product are critical drivers in the site selection process, workforce availability and community amenities often are at the top of the list for many companies looking for a new site.
One leading national distributor considers locations based on the availability and size of potential employee pools, making population heat maps significant in their site selection. Recognizing the need to recruit and retain top talent, this company researches where potential employees live, how they will get to work, making public transportation a decisive factor in their site selection matrix.
Detailed information regarding project parameters and priorities are critical if an accelerated site selection process is desired.
Stakeholders must articulate their needs, describe their processes, and provide crucial information at the beginning of the process to speed up site selection. The ability to speak to their highest priority and articulate the parameters helps site selection and other consultants zero in on a preferred site. Identify key milestone/target dates such as date to close, date to break ground, date of completion, and the date of opening—are crucial to the permitting, design, and construction process.
Experienced site selection teams are able to quickly understand the parameters articulated to them, allowing such teams to expeditiously evaluate and address sites under consideration. Site selection teams can leverage this data to accelerate the site selection process and avoid costly delays.
A smooth site selection process can be achieved through clearly defined parameters, good communication and excellent analysis. The team should be made up of a cross section of skill sets that include expertise in real estate, environmental issues, engineering, construction, tax law, logistics and financing. While the process may be challenging, with the right team, it can be a rewarding and decisive experience.