What every plant manager must know about today’s sensing systems
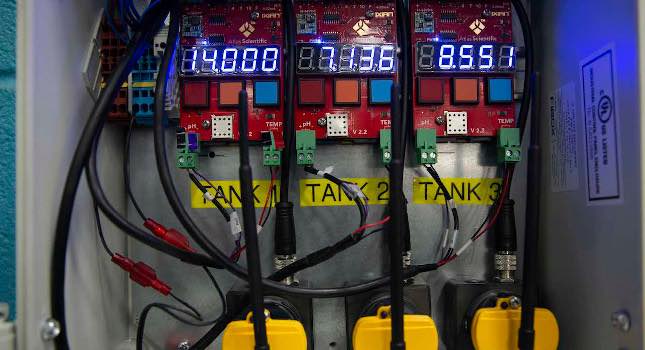
Many manufacturing companies struggle to keep pace with market demands due to production inefficiencies, unplanned shutdowns and delays. Machine performance often is the difference between delays and on-time delivery.
Many — if not most — plant performance issues can be addressed by adopting predictive maintenance strategies that identify problems before they result in broken equipment, flawed products, reduced output and costly delays. While preventive maintenance was widely adopted and embraced over the past decade, relatively few manufacturing operations have implemented predictive strategies and tactics.
Advanced sensing systems that monitor plant machinery condition are the key to modern predictive maintenance strategies. Manufacturers who have the requisite conditioning-monitoring equipment and systems in place can develop predictive maintenance strategies and put them to work to realize uptime and productivity gains.
Performance controlled
Technology is the servant of today’s manufacturing plant operators. Advances are being made in the development of sensing systems, not only in capabilities to measure and gauge, but also information is delivered to those needing it.
The stakes are too great to not consider installing condition-monitoring systems. Many variables come into play, all with the potential to cripple a manufacturing line. Irregularities in temperature, humidity and mechanical pressure can lead to breakdowns, costly to repair and impacting uptime. Operating without advanced condition monitoring increases production headaches and negatively impacts bottom lines.
However, productivity is improved when operations management is aware of possible machine failures before they fail. Conditioning monitoring is gaining wider usage as plant managers come to understand and appreciate the benefits sensing equipment delivers.
Modern condition monitoring requires a digital platform and is made possible by the Industrial Internet of Things (IIoT). Factory connectivity is possible thanks to intelligent networked equipment that transmits data from the machines. This information is stored on the cloud, securely, and is manipulated in whatever format required by managers and technicians. Information is accessible for those who need to keep plants running smoothly, producing efficiently and delivering on-time.
Safety and security
One way to reduce safety risks is to keep maintenance technicians measuring performance or conducting diagnostics away from running machinery. Managers and operators can mitigate risk by measuring machine performance remotely. Thanks to conditioning-monitoring equipment, tests and diagnostics is done by sensors that record data and send it to the cloud, where it can be conveniently retrieved and analyzed. People no longer need to go into harm’s way to analyze machine performance.
Data security must also be considered. It is important to understand the benefits associated with cloud-housed conditioning monitoring systems. Cloud access is password protected and available 24/7 via any device with an internet connection.
The cloud enables secure storage of proprietary information transmitted directly from sensor-enabled machines, without requirements for human gathering, recording and transcribing. Cloud-based condition monitoring can deliver information automatically. A clear advantage exists in receiving exception-based alerts.
Look ahead
Continuous condition monitoring equipment can be easy to install and operate. Systems are affordable for virtually any manufacturer whose managers and operators have access to Internet-connected laptops, desktops, smartphones and tablets.
IIoT-based condition monitoring systems provide a continuous flow of information that indicates the condition of production lines and specific pieces of equipment, and help manufacturers realize improvements in operational efficiencies.
Parker Hannafin’s sensors and software are at work in a variety of manufacturing plants. Experience demonstrates that they support manufacturers seeking to operate machinery efficiently and keep their plant production on schedule and on time.
Success stories include a recent example provided by a manufacturer of washing machines and dryers. Its operations included a plastic injection-molding machine paired with a stamping press, both operated by the same hydraulic power unit (HPU).
At one point in the recent past, the manufacturing setup began producing defective parts. Safety also was a concern, as it was typical for two technicians to be stationed, working as a team, around the machines. One used a manual diagnostic tool at a high-pressure unit while the other was on the floor to cycle the machine and observe its operation. All the tasks involved required considerable setup time, creating safety risks by requiring the technicians to be close to hot machines with moving parts running at speed.
Today, after the installation of sensors at five points on the injection molding machine, a single technician runs the machine and uses custom software to track pressure measurements and watch machine functions from a safe area. Troubleshooting is simplified, downtime is minimized, and costs are reduced.
A wide variety of manufacturing companies that have installed advanced condition monitoring systems realize similar productivity and plant uptime gains.
Parker Hannafin’s cloud-based condition monitoring system supports accurate and reliable predictive maintenance data gathering. Benefits include reductions in:
- Maintenance costs. Many have seen 50% reductions in costs for labor, overhead and materials.
- Mean time to repair. Operators can better plan and make decisions about when and where to repair.
- Spare parts costs. Reduce costs by up to 30%. Instead of ordering and stocking spare parts, conditioning monitoring provides enough lead time so parts can be ordered only as needed.
- Downtime. Reduced up to 40% due to maintenance performed only as needed. This results in fewer planned shutdowns and assets remaining in service longer.
- Machine failures. Expect 55% reduction in the two-year period after implementing a predictive maintenance program with conditioning monitoring sensors.
Other gains include:
- A 30% extended asset life. Based on five years of operating with predictive maintenance, condition monitoring helps prevent damage to machinery and systems and extends their service life.
- A 30% increased asset availability. Realized by monitoring equipment and systems in real time.
- A 25% increase in production. Thanks to reliable condition monitoring, plant operators avoid unplanned downtime.
Custom engineered
Smart sensors are the brains of a continuous condition monitoring systems. They enable more frequent asset monitoring with minimal staff, offsite downloading and analyzing of data, access for multiple personnel in multiple locations, more parameters to collected data and application of the analytics so as to establish a predictive maintenance schedule.
A continuous condition-monitoring system should measure a variety of performance metrics that affect a machine’s output and reliability. These include temperature, humidity, vibration, pressure, strain and current. Each continuous condition monitoring system is engineered to work with a customer company’s proprietary software.
Vibration is a critical area. Your condition monitoring system should include ways to measure your machines’ vibrations, as this often is an important early indicator of problems.
Sensors also should monitor pressure critical to quality control and process efficiencies. Temperature is an obvious area of concern for manufacturing operations. Continuous conditioning monitoring systems detect irregularities that can result in costly downtime and reduced revenues.
Humidity problems also can result from increased operating temperatures. Maintaining optimum temperature and humidity conditions helps ensure machines perform at a high level, improving their length of service.
Your condition-monitoring sensors also should be able to measure stress and displacement while enduring the rigors of millions of cycles. As manufacturing machinery’s electrical components wear, they often require more power to drive operations. Your equipment sensors should be capable of monitoring amperage so that maintenance work can be done before problems develop.
Your condition monitoring systems will work hard for you and deliver numerous advantages.
Final words
Features and benefits of a condition monitoring solution should include easy setup and operation, convenient web-based interface and no software to install or update. Formulating alert notifications should be possible, whether these arrive via email, text or in-system, and they should be customizable. Data can be reviewed anytime, anywhere. Safety is improved because measurements can be taken without interrupting production. Time savings can be significant, as maintenance departments can do more with less. Identifying problematic machines can be the focus.
Plant managers are moving beyond preventive maintenance practices and embracing predictive maintenance strategies built around continuous condition monitoring systems powered by advanced sensors. Their return on investment is significant as they experience fewer breakdowns and headaches, and thereby deliver major gains in plant uptime and productivity.