To cut costs and reduce carbon footprints, manufacturers have turned to variable frequency drives (VFDs) and switched reluctance (SR) motors, which offer energy savings and environmental compliance benefits.
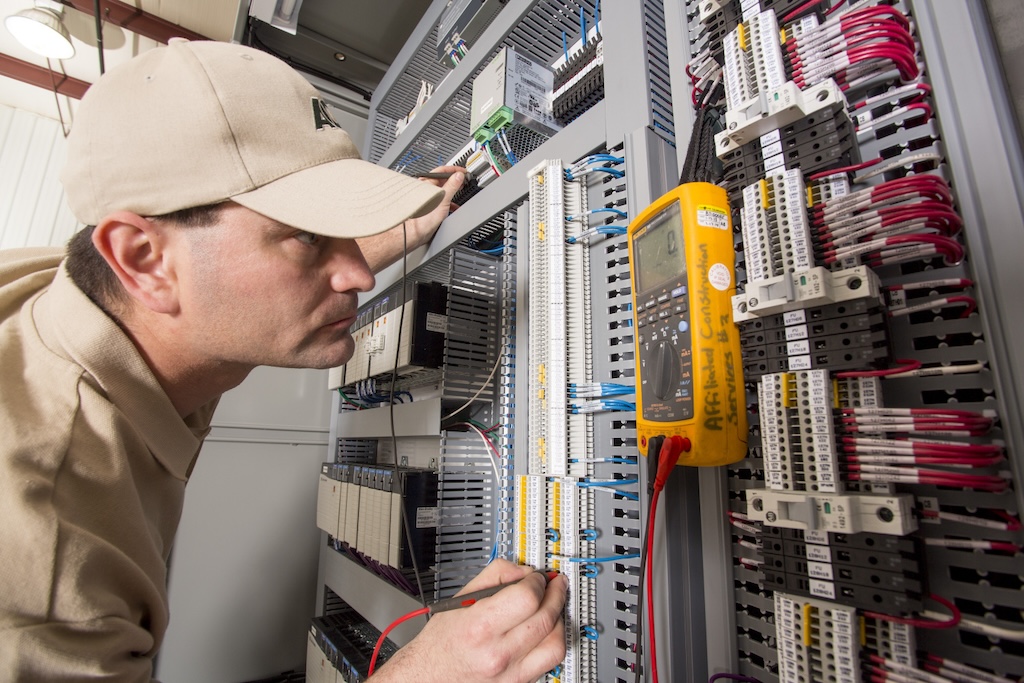
Learning Objectives
- Understand the importance of energy efficiency in manufacturing for cost reduction and environmental sustainability.
- Identify key technologies, such as variable frequency drives (VFDs) and switched reluctance (SR) motors that improve energy efficiency in industrial operations.
- Recognize the challenges and benefits of upgrading to energy-efficient systems and the role of incentives in facilitating these transitions.
Energy insights
- Energy-efficient motors can save manufacturing facilities electricity usage, which translates into cost savings.
- Switched reluctance (SR) motors are highly energy efficient and capable of producing up to twice the power of traditional alternating current motors.
The manufacturing industry is undergoing a significant transformation, increasingly focused on improving energy efficiency and reducing the carbon footprints of the motors and drives essential for daily operations. As manufacturers seek to lower costs and meet sustainability goals, the need for more efficient power generation and distribution systems has become a priority.
Whether you’re responsible for maintaining motor-driven systems in heating, ventilation and air conditioning (HVAC), or in conveyors, pumps or other equipment, enhancing energy efficiency is key to staying competitive in today’s industrial landscape.
Meeting the demand for energy-efficient drives
Manufacturers are being driven by rising energy costs, environmental regulations and the need for operational efficiency. Industrial motors, which account for a significant portion of energy consumption in manufacturing environments, offer an opportunity for improvement. One of the most effective ways to achieve energy savings is using variable frequency drives (VFDs). These drives control motor speed and torque in response to the specific demands of the task at hand, allowing motors to operate more efficiently and consume less energy.
VFDs are particularly effective in applications where motors run at less than full capacity for extended periods. For example, pumps and fans in HVAC systems often operate below their maximum output and adjusting motor speed using a VFD can lead to significant energy savings. With energy consumption representing one of the largest operating costs in manufacturing, these savings can add up quickly. As companies aim to meet stricter environmental standards, VFDs are also helping reduce carbon emissions by lowering the overall energy demand of industrial operations.
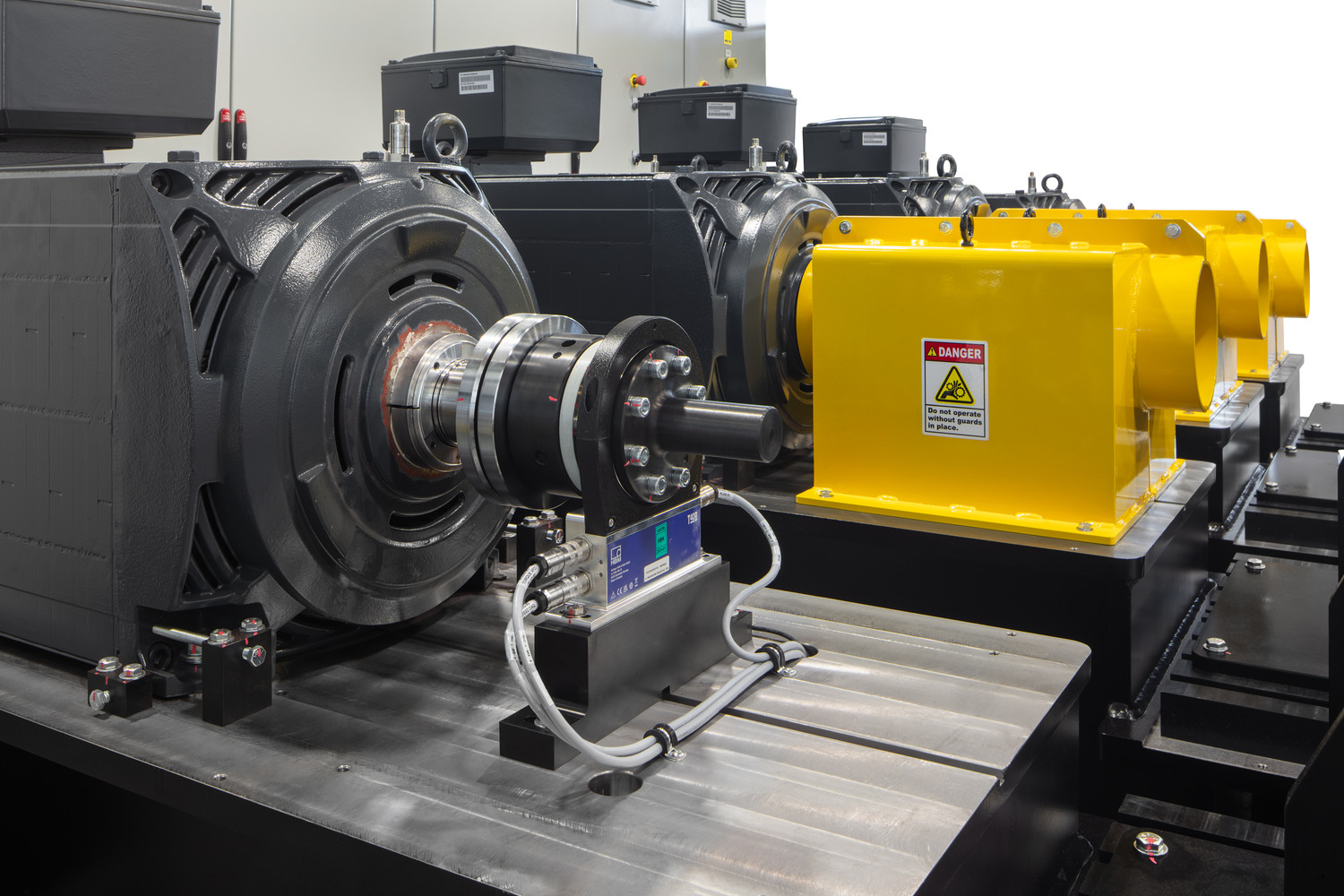
Switched reluctance (SR) motors, though based on an older design, are also emerging as a leading technology due to advancements in cost-effective electronics. Unlike permanent magnet motors, which rely on rare-earth materials and come with environmental concerns, SR motors use a simpler, magnet-free rotor made from shaped iron. This design makes them highly efficient and robust, capable of producing up to twice the power of traditional alternating current motors. Their rugged construction and efficiency make them ideal for electric vehicles and with electronics now more affordable, SR motors are being viewed as a strong alternative to induction motors, particularly in high-demand applications like compressors, pumps and industrial systems.
The benefits of energy-efficient motors and drives
The push for energy efficiency is not just about cost savings; it’s also about reliability and long-term sustainability. More efficient motors and drives offer several benefits for those who work in manufacturing environments, including:
- Reduced operating costs: Energy-efficient motors can lead to significant reductions in electricity usage, which translates into lower energy bills. This is especially important in large facilities where motors run continuously.
- Extended equipment lifespan: Motors that operate efficiently experience less wear and tear, leading to a longer operational life. This reduces the need for frequent repairs and replacements, saving both time and money.
- Improved system performance: VFDs and other motor control technologies allow for better control over system performance, improving the accuracy of operations and reducing waste. This leads to more consistent production processes and higher-quality outputs.
- Environmental compliance: Many industries are facing stricter regulations around energy consumption and emissions. By upgrading to more efficient motors and drives, manufacturers can meet these standards while minimizing their environmental impact.
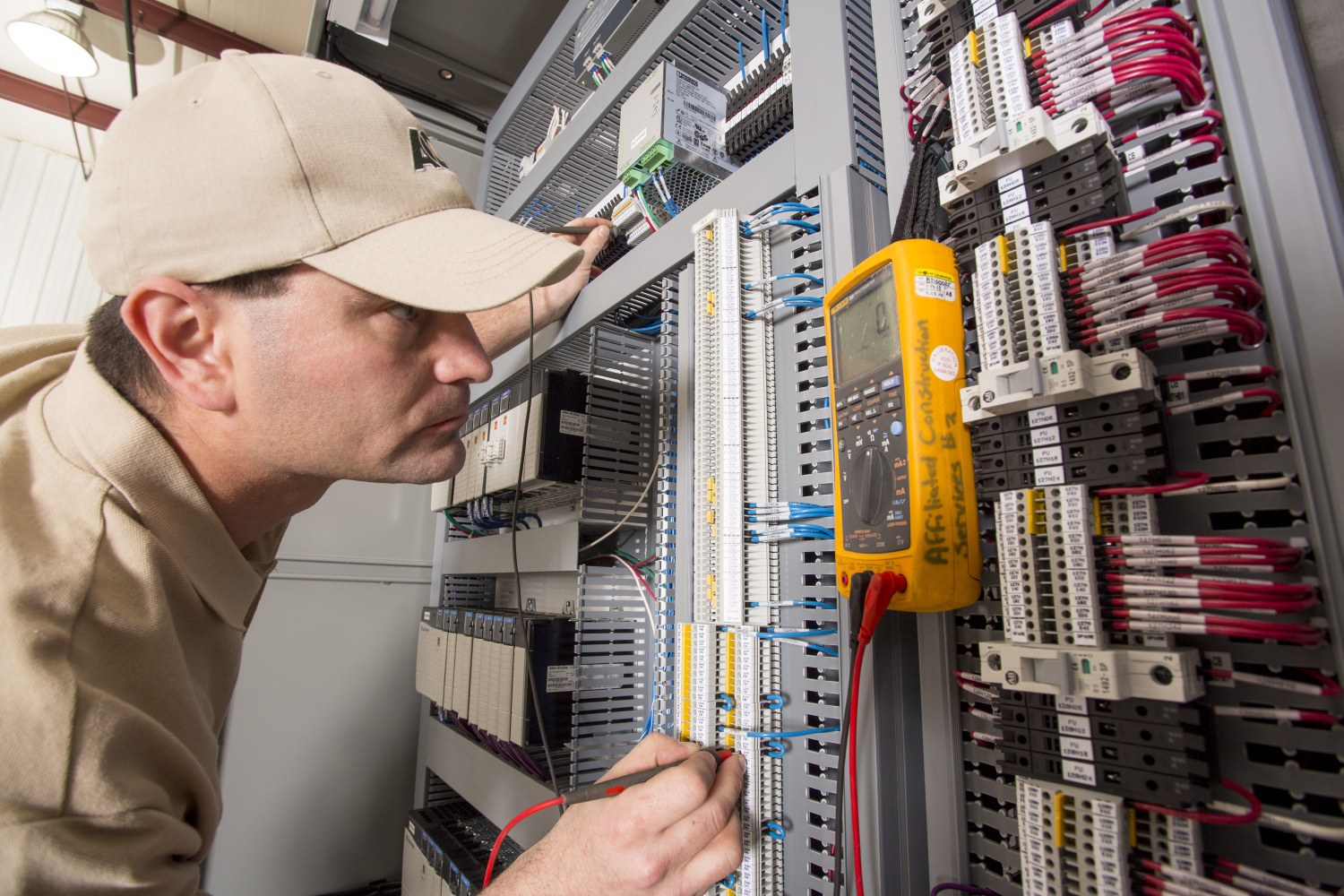
Addressing the challenges of upgrading industrial power systems
 While the benefits of improving motor efficiency are clear, the transition to more energy-efficient systems presents some challenges. One of the main hurdles is the initial cost of upgrading equipment. Although the long-term savings from reduced energy consumption can offset these upfront costs, many manufacturers are hesitant to make the investment without clear financial incentives or regulatory pressure. Additionally, some facilities may face technical challenges when integrating new systems into existing operations.
For example, older motors may not be compatible with modern VFDs, requiring additional upgrades to ensure smooth operation. This is particularly relevant for SR motors, which can experience high torque ripple due to phase switching, complicating their integration with legacy systems. Ensuring that these upgrades are properly planned and executed is critical to minimizing downtime and disruptions to production.
Government incentives, such as tax breaks or grants for energy-efficient technologies, can help offset the cost of upgrading industrial systems. Additionally, utilities in many regions offer rebates for businesses that invest in energy-saving equipment. Taking advantage of these opportunities can make it easier for manufacturers to justify the cost of upgrading to more efficient motors and drives.
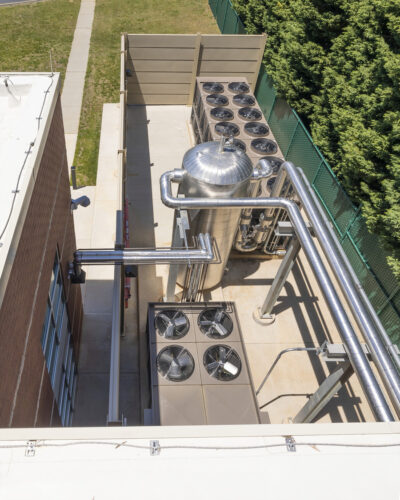
The future of energy efficiency
As the manufacturing industry continues to evolve, energy efficiency will remain a key focus for those who work with motors and drives, including SR motors. Technological advancements, such as improved VFDs and the development of smart motor systems, are expected to drive further efficiency gains. These systems, along with the inherent advantages of SR motors — such as their durable, low-maintenance design and enhanced thermal capabilities — will offer improved monitoring and control, allowing for real-time adjustments that optimize energy usage even further.
Workers responsible for maintaining motor-driven systems must stay informed about the latest technologies and best practices. Understanding how to implement and maintain energy-efficient systems can make a significant difference in the overall performance and sustainability of your operations.
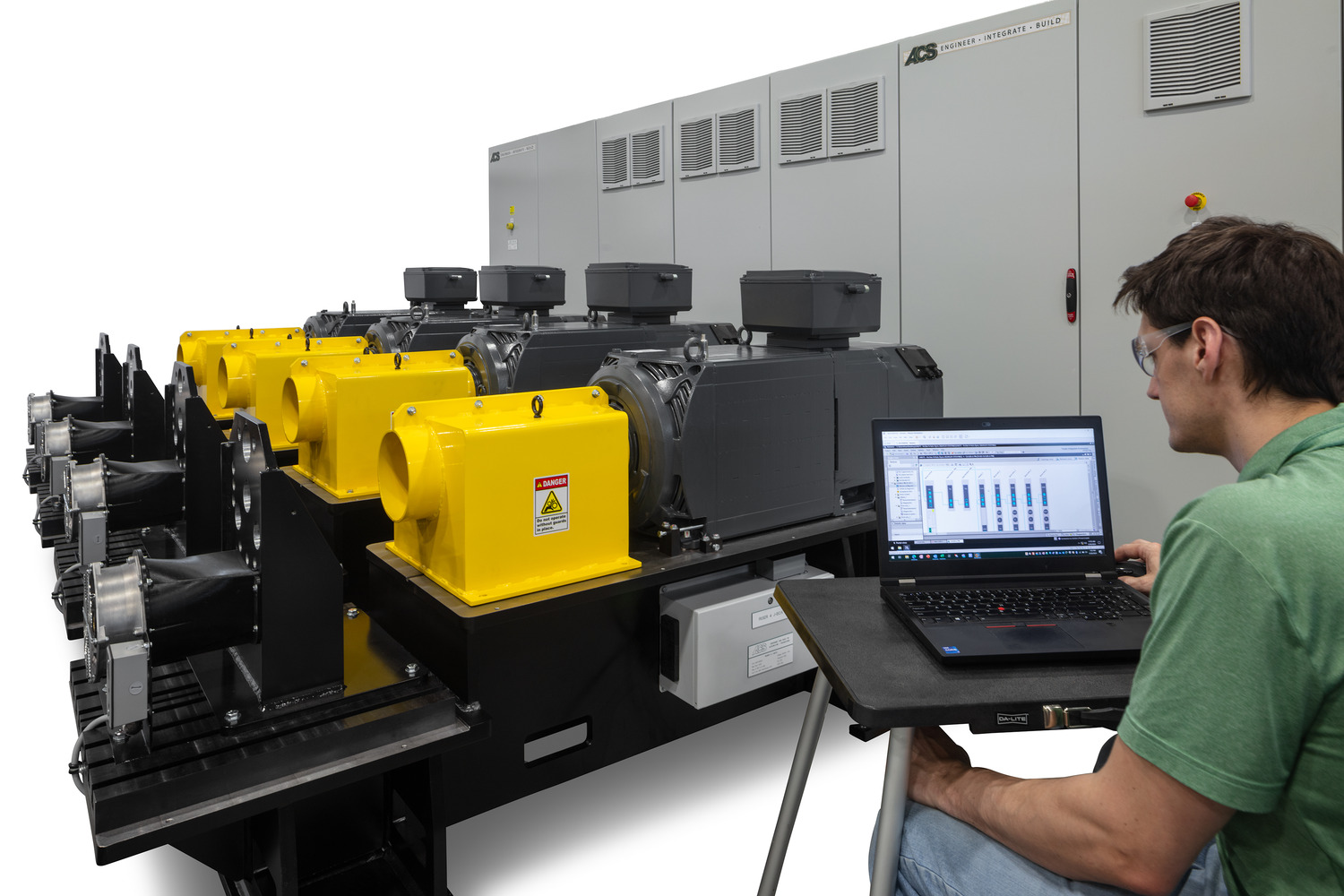
The path to more efficient power systems is a critical one for all industries. By investing in energy-efficient motors and drives, facilities cannot only reduce costs but also contribute to a more sustainable future. Whether you’re operating equipment in an industrial plant or managing systems across multiple facilities, the steps you take today to improve energy efficiency will have lasting benefits for your operations and the environment.
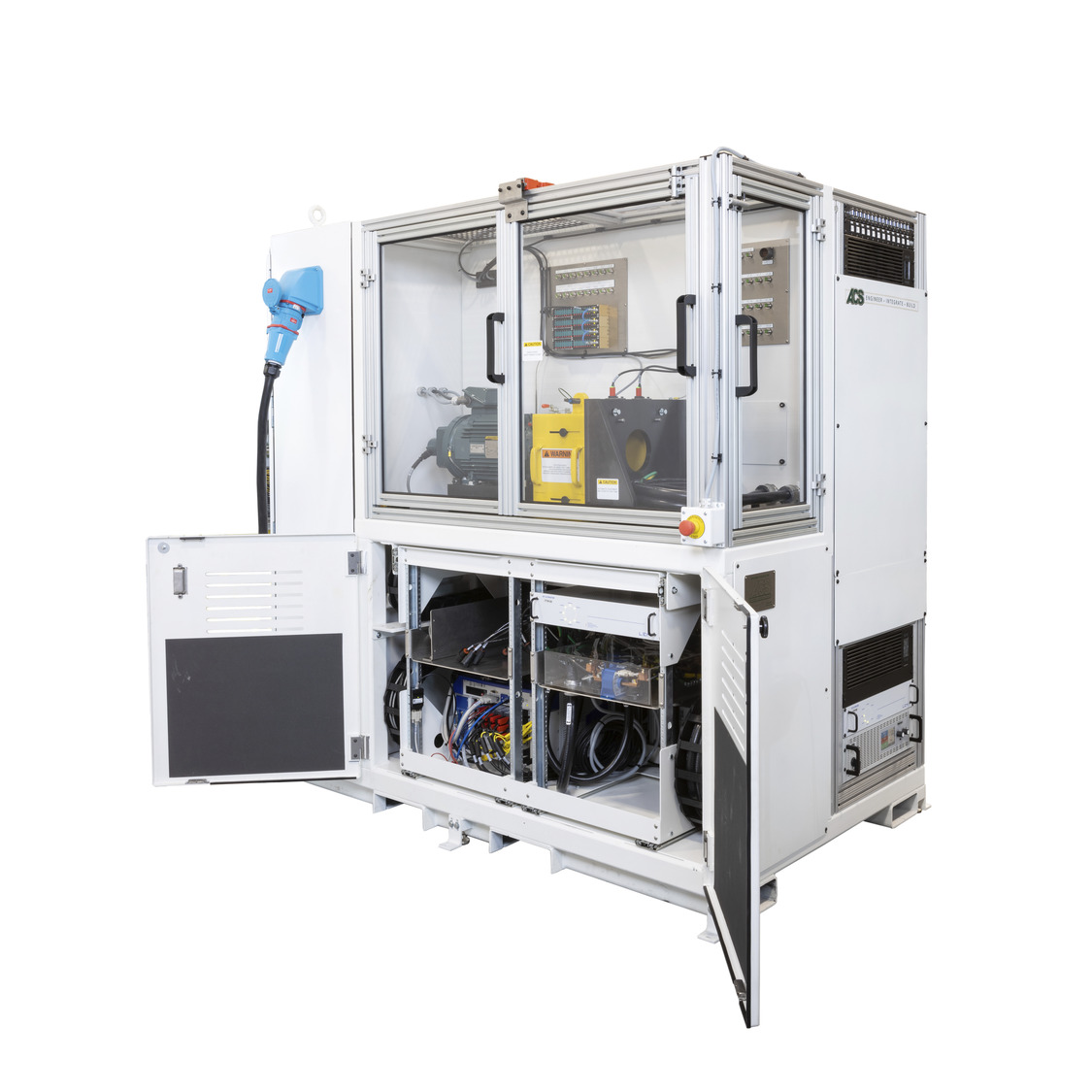