Lockout/tagout procedures for plants, mines and manufacturing facilities can help ensure electrical safety
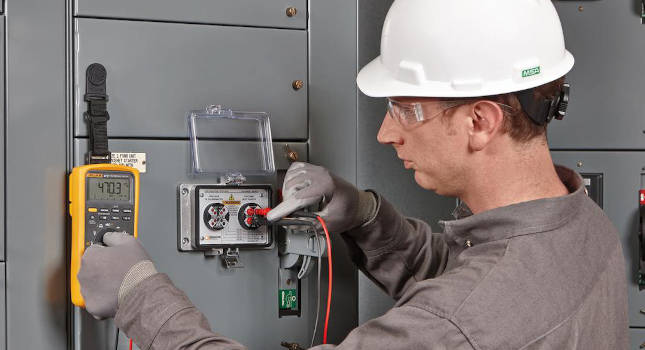
Learning Objectives
- Understand how to avoid Occupational Safety and Health Administration citations for lockout/tagout by making compliance easier.
- Learn how the electrical safety by design philosophy can mitigate risks and increase productivity.
- Review a perspective of one of the most extreme environments for electrical safety.
Electrical safety insights
- Electrical safety hazards can be minimized by having a proper lockout/tagout (LOTO) procedure, and by following NFPA 70E requirements.
- Electrical safety incidents are among the highest in the mining industry. Power and electrical system accidents were cited frequently.
Performing lockout/tagout (LOTO) safely requires the answer to one question: Is there voltage? NFPA 70E: Standard for Electrical Safety in the Workplace requires an absence of voltage test to verify an electrically safe work condition. The traditional process requires electrical equipment that could pose arc flash and shock hazards to comply with NFPA 70E Article 120.5: Process for Establishing and Verifying an Electrically Safe Work.
Lack of adherence to NFPA 70E is one of the Occupational Safety and Health Administration’s (OSHA) most cited violations each year, but some industries have more challenging electrical safety obstacles than others.
Mining workers often face unique electrical hazards compared to most industries that requires a unique approach to electrical safety. These challenges make the mining industry one of the most dangerous to perform routine electrical maintenance tasks due to the extremely harsh conditions that personnel operate within. Exposed wiring and cables necessary to power mining operations are also hindered by wet and damp climates and require the utmost care for electrical safety precautions. Dust and gases generate a combustible and deadly combination that can quickly turn small electrical accidents into deadly fires or explosions.
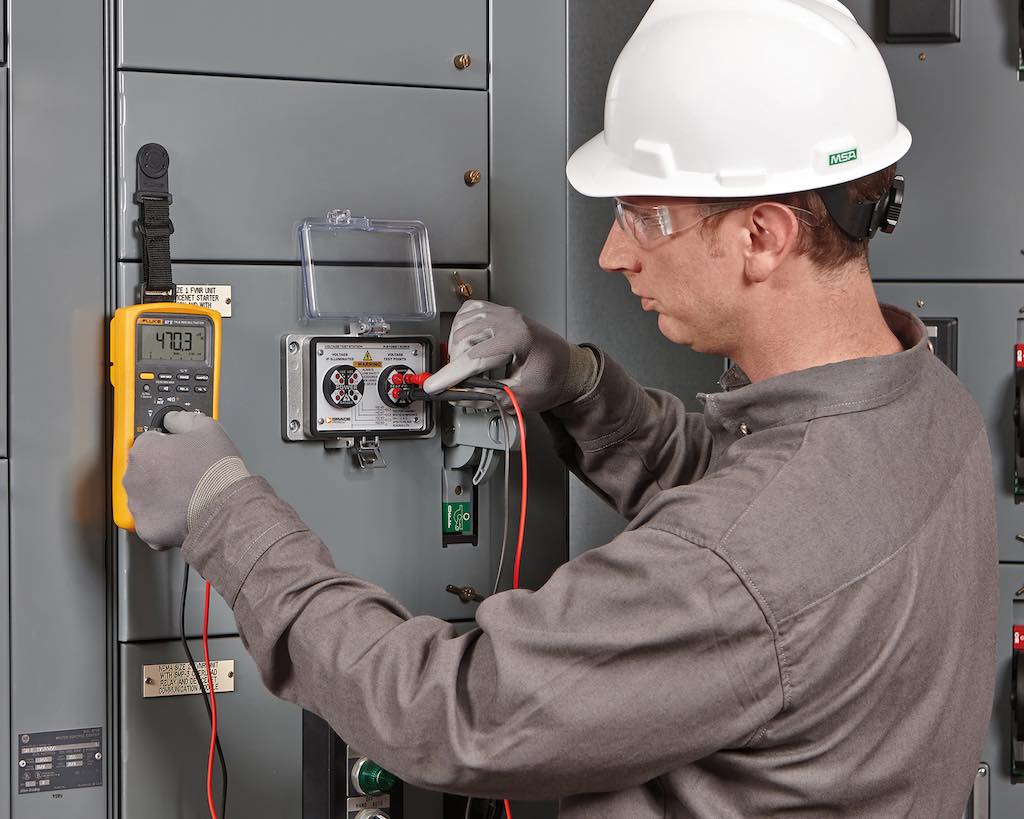
Mining electrical safety hazards by the numbers
When electrical hazards began to present themselves as one of the greatest threat to mining safety, the U.S. National Institute for Occupational Safety and Health (NIOSH) Office of Mine Safety and Health Research (OMSHR) conducted a study between 2000-2009. The study included three things:
-
A direct review of mining industry occupational injury data compiled by OMSHR.
-
An interpretation of the narrative descriptions available for the injuries (from OMSHR data).
-
A separate examination of fatal electrical injuries. During this time period, 865 electrical injuries were reported, with 39 of those being fatalities.
The U.S. Bureau of Labor Statistics reported that 1,573 workplace fatalities between 2003 and 2009 had an electrical cause and an estimated 18,260 nonfatal electrical injuries, resulting in days away from work, occurred over the same period. The NIOSH OMSHR study concluded,
“There were 125,594 mining injuries reported to Mine Safety and Health Administration (MSHA) for 2000 through 2009 and electrical was the 10th most frequently listed cause, with 853 injuries. Of the 853 mining electrical injuries for that period (those with the cause listed as electrical), 39 were fatal, making electrical injuries the sixth most prevalent cause of death in mining.”
Of these injuries, 42% among them were electricians and mechanics. Contractor employees had a much greater chance of an electrical injury being fatal than did mine operator employees due to their unfamiliarity with the equipment and/or industry. Routine electrical and machine maintenance/repair activities were involved in 69% of electrical injuries. The investigators identified the top three root causes for fatal electrical injuries as:
-
Missing or inadequate LOTO.
-
Failure of power system components.
-
Contact of overhead electrical power lines by mobile equipment.
In 2019, three electrical-related fatalities occurred that prompted the MSHA to issue an alert on electrical hazards. According to MSHA, these fatalities occurred when:
-
An electrician contacted an energized component of an electrical circuit while adjusting the linkage between the disconnect lever and the internal components of the panel that supplied power to the plant feed belt motors.
-
A contract electrician contacted an energized conductor while working inside a fire suppression system’s electrical panel.
-
An electrician contacted an exposed energized connector while troubleshooting a flooded bed scrubber motor circuit onboard a continuous mining machine.
As part of the alert issued by MSHA, the administration offered electrical safety best practices consisting of the following:
-
LOTO circuits before working on electrical equipment.
-
Do not rush. Never work alone. Talk to co-workers and confirm if a plan is safe.
-
Identify and control all hazardous energy sources before conducting any task and follow safe work procedures.
-
Train miners on equipment they may use.
-
Electricians must know how to de-energize and disconnect electrical systems and equipment.
-
Always troubleshoot without power first.
The MSHA alert’s best practices, while necessary to raise alarm, offered nothing new in terms of an employer’s and a qualified electrician’s responsibility when it comes to The Control of Hazardous Energy (OSHA 29 CFR 1910.147). This faithful reminder is simply a condensed and informal outline of the steps for performing LOTO. When LOTO is performed correctly, electrical hazards that may result in injuries or fatalities should be mitigated. However, that is not always the case.
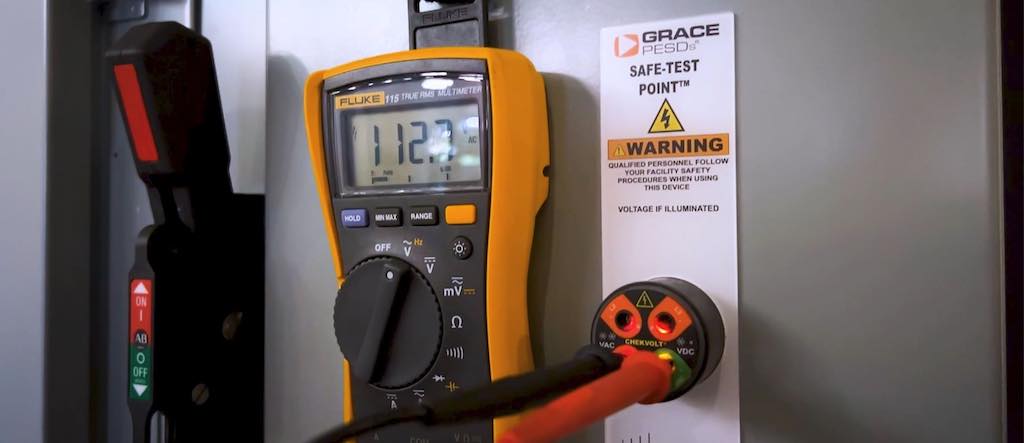
How can you avoid electrical safety citations?
Two of the top 10 most cited OSHA violations are related to the control of hazardous energy and the use of electrical work practices. These are covered under the following OSHA regulations:
-
CFR 1910.147 covers the servicing and maintenance of machines and equipment in which the unexpected energization or startup of the machines or equipment or release of stored energy could harm personnel.
-
CFR 1910.333 covers the safety-related work practices to prevent electrical shock or other resulting injuries from direct or indirect electrical contact when work is performed around the electrical equipment and circuits.
Failure to perform proper mechanical or electrical LOTO can lead to electrocution, electrical shock, arc flash and other hazards. In addition to OSHA fines and penalties, these hazards often result in lost time wages, compensation claims, permanent disability and fatalities.
In 2020, the U.S. Bureau of Labor Statistics reported 126 electrical fatalities in the United States alone, 94% of which were from private industries. The BLS also reported 2,220 nonfatal electrical injuries involving days away from work, a 17% increase from the previous year.
Permanent electrical safety devices (PESDs) are developed through safety by design to mitigate the risks of electrical exposure that result in fatalities and injuries by substantially improving personnel safety and productivity in mechanical and electrical LOTO procedures. PESDs also assist facility personnel by providing preventive measures for integral and repetitive electrical maintenance tasks.
In 2022, OSHA revealed that The Control of Hazardous Energy standard was the sixth most violated citation, receiving 2,175 violations in 2022, 505 more than in 2021. The following is a breakdown of each of those violations:
1910.147(c)(4): Energy Control Procedure: 638 violations
Procedures shall be developed, documented and utilized for the control of potentially hazardous energy when employees are engaged in the activities covered by this section.
Companies can find that by providing a documented LOTO procedure and ensuring employee training and compliance, they will see a reduced risk that directly results in greater efficiency and productivity while complying with OSHA regulatory requirements.
“Lockout” procedures refer to written steps that are taken to bring the machine to a zero-energy state. Once a de-energized condition is established, locks are placed on energy isolation devices that enable personnel to maintain control over the hazardous energy. “Tagout” devices are meant to show that the equipment is in a de-energized state and maintenance is being performed on it.
When combined, the procedure “Lockout/Tagout” refers to lockout devices and identification tags being used in conjunction to indicate that a qualified person is safely performing an energy-isolated task. When employees follow the LOTO procedures enforced by the companies they work for, they are able to better protect themselves from unexpected re-energization or the release of stored energy.
1910.147(c)(7): Training and Communication: 434 violations
“The employer shall provide training to ensure that the purpose and function of the energy control program are understood by employees and that the knowledge and skills required for the safe application, usage and removal of the energy controls are acquired and demonstrated by employees and documented by the employer.”
While OSHA requires that all authorized and affected employees receive periodic training, the implemented training program at any organization can be customized to meet precise needs. However, companies training their employees to meet the minimum compliance standards does not result in achieving maximum safety and productivity.
Today, it is possible for the implementation of a LOTO program to complement OSHA standards by enhancing compliance using PESDs. By installing PESDs wherever LOTO procedures are performed, companies can facilitate these additional safety measures into their written LOTO training program to ensure even further reduced risk and increased productivity.
1910.147(c)(6): Periodic Inspection: 338 violations
“The employer shall conduct a periodic inspection of the energy control procedure at least annually to ensure that the procedure and the requirements of this standard are being followed.”
The three steps to a successful audit program include meeting the appropriate frequency of annual periodic inspections at a minimum, ensuring authorized employees are competently trained to audit and certifying that the inspections are being performed with proper documentation. An environment that is highly productive and efficient is a culture where employees are secure, safe and cared for.
According to the U.S. Department of Labor, a safe and healthy workplace not only protects workers from injury and illness, but can also lower injury/illness costs, reduce absenteeism and turnover, increase productivity and quality and raise employee morale. In other words, safety is not just good practice, it is good for business.
1910.147(c)(1): Energy Control Program: 199 violations
“The employer shall establish a program consisting of energy control procedures, employee training and periodic inspections to ensure before any employee performs any servicing or maintenance on a machine or equipment where the unexpected energizing, startup or release of stored energy could occur and cause injury, the machine or equipment shall be isolated from the energy source and rendered inoperative.”
The purpose of the Energy Control Program is to provide written policies and rules within a safety management system. This regulation addresses the practices and procedures necessary to disable machinery or equipment that will prevent the release of hazardous energy while employees perform servicing and maintenance activities.
If procedures include PESDs, the plant or safety manager can document and provide training on the use and interpretation of these devices as part of the LOTO procedure for the specific equipment they are installed on. PESDs also are available to be installed with custom warning labels. This greatly assists employees when performing LOTO on equipment that features voltage indicators and/or portals by decreasing the risk of exposure to hazardous energy.
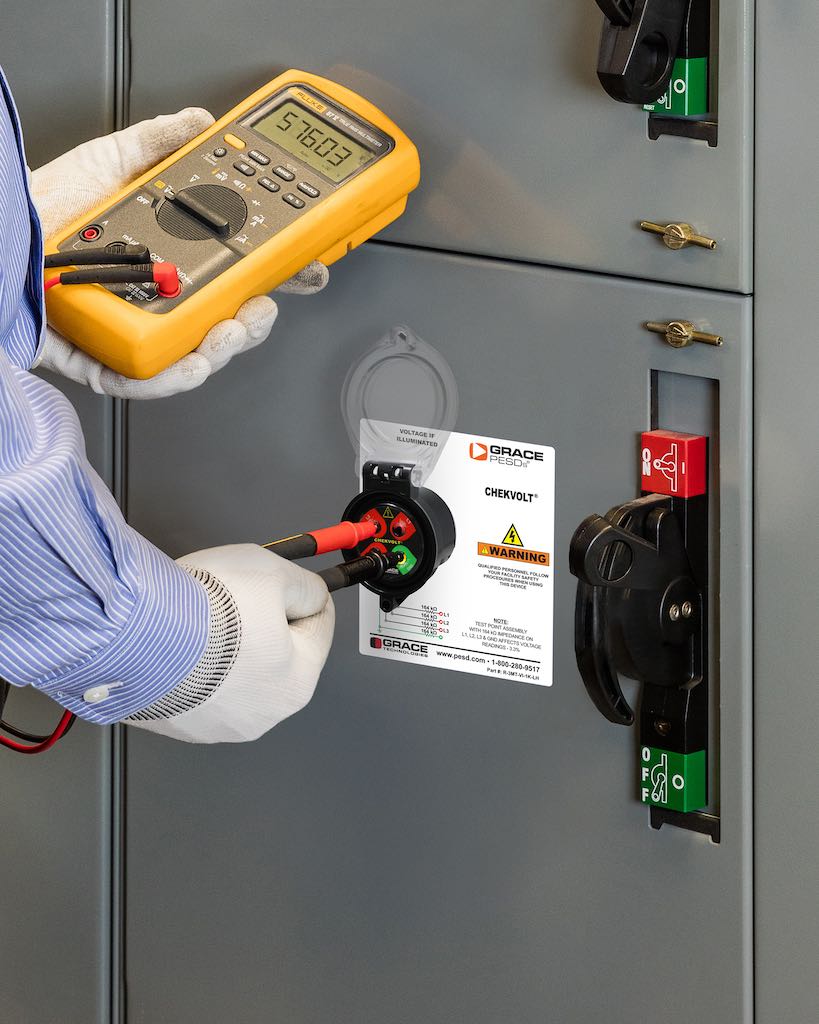
How the electrical safety by design philosophy mitigates risks
Electrical safety by design works to confront common LOTO procedural and implementation issues, user error, compliance and productivity by providing innovative safety solutions that mitigate or eliminate various task risks. When properly incorporated into a facility’s Electrical Safety Program, through-door voltage indicator and test point PESDs inherently reduce risk by providing a safer and more efficient method of performing verification of hazardous energy isolation. In addition, PESDs are designed to improve the ease of compliance with NFPA 70E and OSHA energy isolation principles.
In mining sectors, a small spark may result in a deadly combustion. Contractor electricians unfamiliar with equipment would benefit from PESDs providing a safer method of performing LOTO. Voltage presence LED indication will warn personnel when hazardous energy is present, preventing accidental contact. The return on investing in electrical safety will provide increased safety, reduced downtime and peace of mind.