Manufacturing has changed a lot due to the COVID-19 pandemic as technologies thought to be happening down the road are happening now. Five key drivers are highlighted.
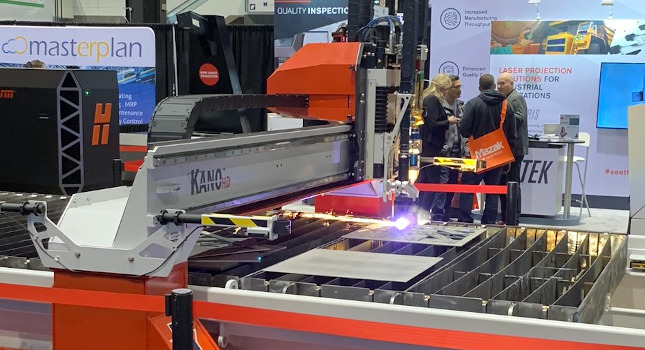
The COVID-19 pandemic and government-mandated shutdowns had a significant impact on our lives. Supply chain disruptions became part of regular news debates and discussions. Manufacturers had to pivot their operations according to the new reality. The change in industry leaders expected to happen by 2025 are happening now. Industry 4.0 is now closer than ever with widespread adoption by industry leaders across the world.
Let us take a look at how manufacturing is changing for good in the post-pandemic world.
Future of manufacturing
Multifaceted changes are happening in the manufacturing industry. They address the various inefficiencies in manufacturing facilities. The focus is on process improvements for the current industry landscape. There are five key drivers in the change:
- Automation and robotics
- IoT and artificial intelligence
- Upskilled workforce
- Localized supply chain
- Digital supply chain.
1. Automation and robotics
Automation was the hallmark of Industry 3.0. The introduction of programmable logic controllers (PLCs) and supervisory control and data acquisition (SCADA) systems in manufacturing facilitated this. The rise of microprocessors and associated software has increased access to automation. It also made it easier to implement automated manufacturing facilities. It led to the rise of versatile robots, like six-axis robots. The cost of implementation is also dropping every year.
The lockdowns due to the pandemic gave an edge to manufacturers with automated facilities. They ensured a socially distanced work environment and worked with a smaller workforce. Manufacturing facilities will move to an automated production line. It will use programmable robots and control systems. Turnkey assembly line solutions help manufacturers to install automated production lines.
2. Upskilled labor force
The workforce of the future needs a completely different skillset from that of today. Today forklift operators are prevalent in almost all manufacturing facilities. Forklift drivers will become redundant with automated guided vehicles (AGVs) and other automated moving technologies.
However, it necessitates the need for labor force with other specialized skill sets. Automated factories will need maintenance technicians more than operators. Production loss is costly in an automated manufacturing facility. Maintenance technicians are the ones who have to ensure the machines run according to the specifications. They will also need to conduct predictive maintenance.
There will be an increase in demand for other technical services. These include troubleshooting, equipment assembly, researchers, engineers, and operations executives. There will also be a shift in industries that demand more labor. The pandemic increased the reliance on e-commerce for everyday shopping. This led to a higher requirement for labor in warehouses and distribution centers. The workforce has to adapt to the changes by investing in improving their knowledge and skills.
3. IIoT and the data economy
The Industrial Internet of Things (IIoT) will be widespread in manufacturing facilities of the future. The basic tenet of IIoT is that every device in a manufacturing facility will have sensors that collect data round the clock. The data thus collected is relayed through a low-latency, fast network for automation control and analysis. Automation control systems will work faster with 5G and Wi-Fi 6E coming up soon.
The vast amount of data collected can be analyzed using artificial intelligence. Machine learning algorithms can draw insights from data. Traditional analytics would not be able to handle the large volume of complex data. Cloud computing enables big data analysis using artificial intelligence. Edge computing helps to analyze data faster on devices within the premises of the factory.
The vast amount of data collected is useful for predictive maintenance. Machine learning algorithms analyze various streams of data to predict machine failure. IIoT data is also useful in implementing digital twins. Digital twins help OEMs monitor all their assets while in operation. Data from assets in one part of the world can be used to improve assets in another facility. They also can be used for predictive maintenance.
4. Localized manufacturing capability
COVID-19 exposed the vulnerabilities in the global supply chain. This was aggravated by the blockage of the Suez Canal. Manufacturers are now aware of the danger of concentrating their production capabilities in one part of the world. They are setting up localized supply chains for a robust logistics infrastructure.
U.S manufacturers will move more manufacturing facilities to the United States. This will reduce the dependency on production facilities in Asian countries. Strong political and social pressures are also factors in the change. Consumers also view goods produced in China negatively. Various states in the United States are giving businesses incentives for setting up manufacturing facilities in the U.S.
Manufacturers shifting production facilities to the U.S will have to balance the need for a strong supply chain and cost concerns. Automation with the use of specialized robots is the way forward for them. This will be complemented by recruiting skilled labor from within the country. This helps the businesses to have a reliable and robust supply chain. Also, provides an economic boost to local communities.
5. Digital supply chain
The supply chain is the complete infrastructure from sourcing raw materials to delivering products to the end consumer. Supply chain shocks experience due to coronavirus disruptions made companies rethink the entire supply chain function. Supply chain visibility became important in managing it.
Supply chain visibility is the capability to track movement in the entire supply chain from one location. This includes monitoring a lot of moving parts. These include,
- Suppliers
- Vendors
- Warehouses
- Distribution centers
- Point of sale data
- Manufacturing data
- Live transport data
- Employee information
- Macroeconomic data
- Geopolitical news.
The variables are limitless as every stakeholder has to be monitored. Supply chain visibility is enabled by software integrations with all the stakeholders. Another aspect is the trust between various parties that leads to open and transparent communication.
The future of manufacturing awaits
The changing trade landscape necessitates a change in the approach to manufacturing in the future. Automation, skilled labor, local US manufacturing facilities, and a robust supply chain will form the bedrock for the future of manufacturing in the post-pandemic world. RedViking is a pioneer in bringing solutions to challenging manufacturing problems. RedViking has turnkey solutions for assembly lines, robotic applications, and other challenging engineering problems.
This article originally appeared on RedViking’s website. RedViking is a CFE Media content partner. Edited by Chris Vavra, web content manager, Control Engineering, CFE Media and Technology, [email protected].