A case study of how a Spirax Sarco audit led to an optimized condensate collection and return for improved control and energy savings.
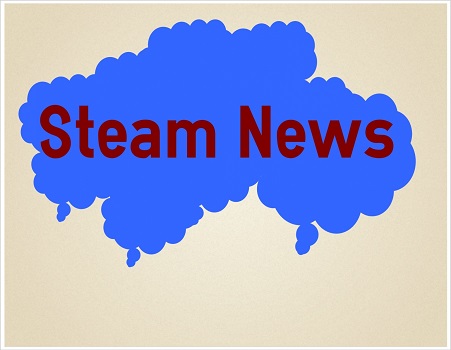
Expansion can be a mixed bag. With the satisfaction of increased production and revenues often come the headaches of rate limiting process stages and capacity ceilings. Such was the case at a North Carolina dairy operation, where growth had served to highlight serious deficiencies in the facility’s steam operations. The dairy operation called Spirax Sarco for an audit of its steam and condensate system.
Initial Observations
The dairy operated one 200-hp boiler, which could normally handle the load, yet was approaching capacity. The Spirax Sarco audit showed operational costs to be excessive, especially boiler treatment chemicals, fuel and water. The first task was to reduce makeup water by returning condensate before looking at upsizing the boiler.
Some heat exchangers (HEs) had traps that dumped straight to drain, not returning condensate back to the boiler. Other HEs had small float and thermostat (F&T) traps on the coil outlet, with a 10′ head to discharge, making the HE operate inefficiently in a "stall" condition. The only condensate return pumps were small, vented cast iron electric pumps. With the large head, these pumps cavitated frequently, exhibiting short life-spans and causing maintenance burdens.
Pasteurizing Improvements
The pasteurizing room had three HEs for milk and buttermilk. To correct condensate blocking and pump cavitation, Spirax Sarco recommended 1-1/2" Model APT14 Pump-Trap Systems be installed on each HE, positioned to remove condensate by gravity and eliminate the flash steam venting necessary with the old single electric condensate pump. Operating at temperatures above 212°F, the APTs could cycle more heat back to the boiler in the hot condensate, saving considerable energy.
Clean-In-Place (CIP) Heating Improvements
For heating clean-in-place solutions for ice cream, milk, and raw milk processing vessels, the dairy used four shell and tube HEs served by 1" or 1-1/2" solenoid operated (on/off) steam valves. The ice cream CIP HE had a 3/4" thermo-dynamic trap; the others had 1-1/2" F&T traps.
With closure of the steam valves, condensate formed in the HE tubes, and the gaseous phase went to vacuum. There were no vacuum breakers installed in the system. With the opening of the steam valves, significant stresses were forced upon the traps and the electric condensate pumps. Spirax Sarco recommended installation of 1-1/2" Model APT
Pump-Trap Systems for the four units. Two would handle condensate from the paired milk CIP units. The APTs would function as F&T traps, eliminating steam blocking when the steam valves opened.
Draining by gravity, they would remove the hot condensate more efficiently than the small electric condensate pumps they would replace. They would also conserve energy by eliminating both stalling in the HEs and the wasteful flash steam venting required to protect the misapplied electric condensate pumps. The pump traps were configured as skid-mounted package based on the benefits of simple, three connection installation and single-point responsibility by Spirax Sarco.
Based on the success with the processing vessels, attention moved to the case washer, milk production HE, raw milk CIP and orange juice heat set applications experiencing similar stalling and inefficiency problems. These problems were solved by the same pump-trap modules.
The Results
Conservative estimates of losses in pasteurizing and CIP solution heating totaled about $22,000 per year. Adding maintenance and spare parts costs, payback was estimated to occur in about 2 years. Next-phase optimizations included a hot water HE system with pneumatic control valve, pump-trap and controller; a pneumatically actuated KEA Control Valve, SP2 Positioner and a PN663 Controller; and drip leg traps for the main steam header.
– Content provided by Spirax Sarco, originally published in Steam News Magazine.
– Edited by Jessica DuBois-Maahs, Associate Content Manager, CFE Media, Plant Engineering, Control Engineering