Solving the Industrial Boiler Replacement Riddle
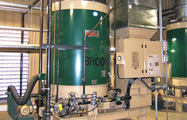
It’s a familiar story. Your plant has a need for steam that changes throughout the day, or from day to day, or with different seasons of the year. You have an existing boiler plant, but it’s getting old and unreliable. Sometimes your older boilers are still running fine, but you know their efficiency isn’t very good. You need to keep them running when you aren’t using steam at all, but need it to be readily available. Does this sound familiar?
An Attractive New Approach
For many owners, the solution has been to install one or more compact, efficient coil tube natural gas-fired boilers, often called steam generators. This approach is attractive because these packaged units take up little floor space and can either supplement or replace an existing traditional boiler. Units are factory engineered, skid mounted, and many can fit through a standard double door. Most offer efficiencies in the 85% area, far exceeding most older firetube or conventional watertube boilers.
Andy Wales is the Western Regional Sales Manager for Clayton Industries, a manufacturer of a line of coil tube steam generators. Wales notes that these units are being used in a wide variety of industrial plants. “They almost always offer both operational and installation savings over more traditional designs. Over the past years we have seen a multitude of installations, both batch and continuous duty profiles, where these steam generators have replaced traditional designs.”
Numerous Inherent Advantages
The Clayton design uses a helically wound coil design in its main heat exchanger sections. According to Wales, its main advantages are compact size, high thermal efficiency, rapid startup and good load-following characteristics. He also cites low blowdown volumes and its high level of operator safety. A very attractive feature of the coil tube boilers is that because they have a very low volume of feedwater to be heated, they can be on line from a cold start in ten minutes or less.
For this reason they are ideal for intermittent steam uses and for plants that do not operate around the clock. In many plants, it has been necessary to keep a conventional boiler in warm standby status, often with a licensed operator on duty, to assure that steam is quickly available when needed. In most cases, this warm standby requirement can be eliminated by installing a coil tube boiler.
Shut Down Main Boiler Plant
Industrial operators are also increasingly appreciating the value of a “pony” boiler, which can meet all of the plant’s steam requirements during summertime operations, or during off-shift hours. Again, this is an ideal application for the compact and efficient coil tube boiler. The heavy main boiler plant can be shut down for the season, or until greater steam volumes are required for manufacturing loads.
Because the typical coil tube boiler does not include a pressure vessel, in many areas it does not require a licensed attendant to be on duty. According to Bryan Heppell, President of Thermogenics Boilers, his company’s product is exempt from licensed operator requirements in Ontario, Manitoba, Quebec, Newfoundland and in the U.S. in Ohio, Detroit and several other areas.” According to Heppell this attribute, along with the Thermogenics coil tube boiler’s quick steaming, small footprint, 10:1 turndown ratio and high efficiency, are attributes that make it a popular choice for industrial and institutional applications.
The main reason why operator licensing is often waived is that steam generators have a substantially lower water volume than traditional firetube designs (around 5% to 10% of the water volume) and have no pressure vessels full of water at high temperatures and pressures. This makes them inherently safer to operate. In all cases, owners should check with their local boiler code authorities and insurance agencies.
Look at Total Operating Efficiency
In looking at operating efficiency, it is useful to look at the overall load profile and include all operating costs in the buying decision. This includes both direct costs and operator costs. A steam generator with a quick startup characteristic can save a significant amount of operating labor for a plant that operates less than 24 hours per day or fewer than seven days per week.
Andy Wales from Clayton points out that a plant that has a large difference between summer and winter steam loads can save by having a smaller summer unit or by using multiple units to handle varying loads. He adds, “Fuel is not the only operating cost. Blowdown can also be a large expense if the user is not able to easily dispose of it in the municipal sewer system.”
Every Application Different
Each industrial application has different characteristics and drivers for a boiler replacement or addition. The size and condition of condensate return systems can influence what type of system is the best fit. Vendors offer a wide range of systems, using either single or multiple units. Choosing the right control package will help units follow load conditions.
According to Marc Dupuis, National Sales Manager for Vapor Power, coil tube boilers are proving to be the best choice for a wide variety of industrial and institutional applications, including food and beverage industries, pharmaceuticals, universities and hospitals, and more. “Basically, any type of process or heat and process steam application can utilize these boilers.” Vapor Power offers two types of coil tube boilers.The Modulatic® is available in sizes from 18 bhp to 300 bhp and design pressures to 3200 psig, and the Circulatic® has sizes from 75 bhp to 600 bhp with pressures to 530 psig.
Payback for Higher Initial Cost
Dupuis feels that its operating efficiency is a driving force for the choice of coil tube boilers over other designs. “In many cases a coil tube boiler will be more costly for the initial purchase of the equipment than other boiler technologies. However, when overall life cycle costs are considered, such as installation costs and operating costs, there is a payback for the coil tube technology. This can far offset any difference in initial purchase cost.” Dupuis explains that other advantages for the coil tube boiler are fast startup, compact size, low weight, full range modulation, available high operating pressures and safe operation.
Support after Installation
In selecting a boiler, it is valuable to consider all of these points, as well as such issues as availability of parts and service, how well it will match up with the existing steam plant and feedwater system, and whether it can be included in the present steam plant control scheme. Other low volume designs, as well as high efficiency condensing boilers can also be considered. A qualified mechanical engineer can help find the answers to these questions, using the technical assistance of manufacturers.
Although coil tube boilers are not the only option for boiler replacement or addition. they are certainly an important option that should be considered. They may match up well with your steam plant needs, and save your company energy and money as well.
More Info
Clayton Industries
www.claytonindustries.com
Gasmaster Industries
www.gasmaster-ind.com
Thermogenics Boilers
www.thermogenicsboilers.com
Vapor Power International
www.vaporpower.com