Automation projects come with many challenges that seem daunting because of their complexity. Learn about six common automation project management challenges and learn about five tips to overcome them including planning ahead and leveraging available technology on the plant floor.
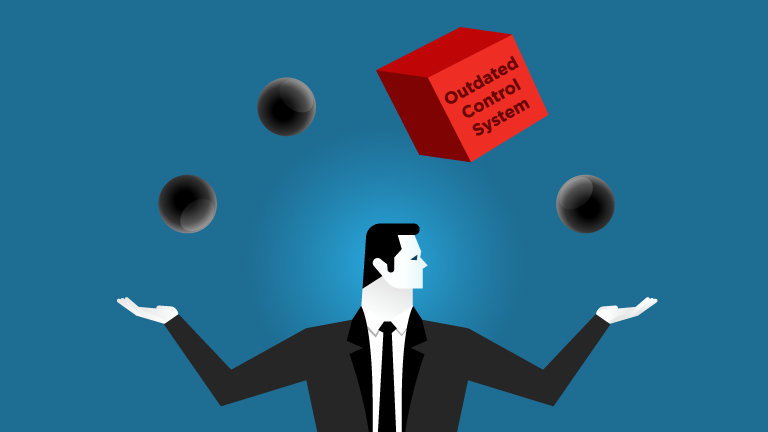
Advances in control system technology and smart field devices are changing the way manufacturing companies view their process automation. Opportunity abounds for those who want improved asset utilization, access to real-time data, improved control and enhanced connectivity. For many companies, maintaining the status quo is no longer an option. They must change or face the risk of becoming uncompetitive in their markets.
Many companies, however, find automation projects difficult to execute with their inherent complexity, evolving scope, rapidly changing technology and human interaction. How can project teams get past these numerous challenges and leverage innovative technologies to improve operational efficiency and performance? There is no easy answer, but recognizing there are many challenges and working to manage and overcome them is a good start.
Six automation project challenges
While not all projects have every one of these challenges, these are characteristics that do crop up often enough. Project teams embarking on an automation project should be on the lookout for these potential issues.
1. A fragmented market. The process automation market is highly fragmented; a typical control system can contain thousands of individual components from numerous suppliers. The project team must bear the responsibility to integrate these disparate components and ensure they work together. Considerable engineering and coordination is required to ensure everything comes together to form an integrated, high-performing control system.
2. Rapidly changing technology. Automation equipment is based on rapidly changing computer, software and electronics technology. As the underlying technology advances, it can be a considerable challenge to keep project personnel proficient in implementing the latest best practices. The ongoing education needed to keep pace with this technology change presents a strain on employees who have limited bandwidth outside of their daily workload.
3. Third-party interfaces. Control systems are becoming dependent on information from smart field devices and subsystems, which can use multiple interface protocols because there is no one communication standard. Implementing these third-party interfaces requires an understanding of each subsystem and smart device in addition to learning the characteristics and limitations of the various communication protocols. Getting access to this specialized knowledge and experience for the particular combination of interfaces on any project can be a daunting task.
4. Documentation requirements. Automation projects require extensive documentation to define the requirements and maintain the resulting assets. Simple changes can affect multiple documents. Just changing an instrument tag, for example, affects the piping and instrumentation diagram (P&ID), input/output (I/O) list, instrument spec sheet, distributed control system (DCS) database, field junction box drawing, marshalling cabinet drawing and loop sheet. Keeping documentation current and accurate throughout a project is challenging.
5. Scope evolution. Automation scope is difficult to define as it encompasses all the thousands of components and numerous operational states. Unlike mechanical and civil projects, expecting to define exact functionality up front is not practical as the scope changes and evolves throughout the life of the project — even through commissioning and startup. Knowing what scope should be nailed down up front and what scope should be allowed to evolve is a key component to successful automation project execution.
6. The operator interface (OI). The automation system serves as the primary interface between the collection of equipment that makes up a plant and the operator who is trying to run it. It is critical for operators to get an accurate and complete view of how the process is behaving and how the equipment is working to achieve successful operation. If the automation system is contributing to process upsets or not communicating an accurate picture of unit operation, the lost opportunity costs can be massive. To further complicate the matter, because the OI is a tangible item, it seems everyone has an opinion on how they should look and function. Getting operator acceptance while incorporating the latest technology can be difficult.
Five steps for mitigating project risk
With these challenges, how can project teams mitigate risk and achieve company objectives for greater operational efficiency and performance? Consider these five best practices and strategies to help ensure success.
1. Plan early. As with any complex project, companies need an upfront plan developed before jumping into execution. Engaging the right team early in the process and performing appropriate front-end loading/front-end engineering design (FEL/FEED) is key. Risk increases without a scope that has been defined and agreed upon by the various stakeholders. Performing an appropriate level of upfront engineering without being too rigid on an evolving scope is critical to getting the project started on the right foot.
2. Standardize. Because automation equipment is used in different industries and applications, it has a huge amount of flexibility to be customized for many different needs. A downside of this flexibility is some guidance needs to be established to ensure it is applied properly for the particular application. It is also likely the automation platform will be in place for more than 20 years with multiple personnel performing modifications along the way. Without some way of defining how these modifications are applied, the project team could end up with the same functionality being implemented different ways, creating a maintenance nightmare. Using appropriate standards is critical to getting the most out of the automation investment and ensuring it is consistently applied to meet the project’s needs.
3. Leverage technology. Modern control systems contain valuable technologies that can make a significant improvement to operations. Unfortunately, many companies fail to take advantage of these potential improvements because of their desire to minimize the change imposed on plant personnel. When the primary objective is to make the new control system look and feel like some legacy platform that was installed 20 years ago, it places a severe limitation on the company’s ability to improve. Recognize and take advantage of modern technology, and don’t be bound by false limitations by being averse to change.
4. Test and commission. Rigorous testing and commissioning procedures executed by qualified personnel are critical for safe and efficient startup. Shortcuts here will lead to operational problems, costing many times the minimal savings from reduced commissioning time. Take the time to create thorough procedures with input from subject-matter experts who have experience with automation and to follow the procedures carefully using personnel who have done it successfully before.
5. Execute with discipline. Applying robust project management discipline is beneficial for all projects, especially for large and complex ones. A detailed project execution plan (PEP) includes defined roles and responsibilities, risk matrix, quality plan, testing plan, training plan, resource-loaded schedule and other appropriate items are all important for effective execution. Best practices like holding effective, regular project team meetings and following a proper communication plan will help keep everyone on the same page and performing well. Also, creating proper documentation that is updated and controlled so the latest revisions are in the hands of the people using them will improve efficiency during construction and commissioning.
With so many challenges unique to automation, it is inadvisable for project teams to execute without the knowledge and experience on how to overcome them. When extensive multi-platform and technological expertise is needed, engage a partner with the familiarity and skills required to integrate and implement automation system components and technology. The right partner can help guide the project to success and maximize the return from an automation investment.
Lee Swindler, industry manager, Maverick Technologies, a CFE Media content partner. Edited by Chris Vavra, production editor, Control Engineering, CFE Media, [email protected].
MORE ANSWERS
Keywords: Automation engineering, project management
Automation companies must change and adapt to a rapidly evolving market or run the risk of being uncompetitive.
Challenges companies face for an automation project include a fragmented market, scope evolution, and third-party interfaces.
Steps for mitigating these challenges include planning early and leveraging technology on the plant floor.
CONSIDER THIS
What is the biggest challenge you face in an automation project and how do you overcome it?