The proper fit for fall protection harnesses can help employers better protect their employees when falls occur.
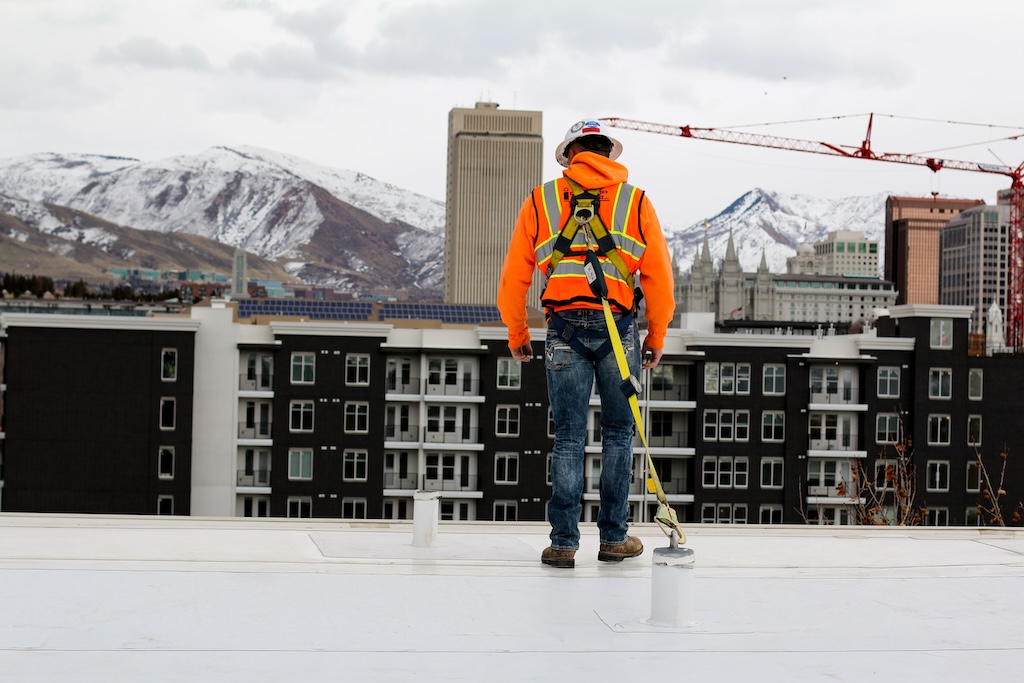
Learning Objectives
- Discover the proper fit techniques for fall protection harnesses.
- Find out what two inspections are required by Occupational Safety and Health Administration for fall protection equipment.
- How to conduct pre-use inspections for fall protection harnesses.
Fall protection insights
- Ensuring best practices for fall protection harnesses will protect workers from catastrophic accidents.
- Employers need to know about the minimum Occupational Safety and Health Administration requirements regarding body harnesses and how to encourage workers to use these harnesses to protect themselves.
- When employees know how to use their fall protection harnesses and feel confident in their safety, they can do their jobs without fear.
Falls are the third leading cause of injury and fatality among general industry workers. Additionally, fall protection violations have been the most cited Occupational Safety and Health Administration (OSHA) violations for the last 14 years.
According to the National Safety Council’s most recent data from 2022, 865 workers died in fall-related incidents with more than 80% of those deaths occurring after falls to a lower level. The U.S. Bureau of Labor Statistics has shown an average increase in fall fatalities since 2010.
While many organizations have joined OSHA’s efforts in raising awareness of the risk of workplace slips, trips and falls, the current data suggests that more must be done to decrease the number of falls that occur. If fall injuries can be mitigated or prevented, then unnecessary deaths can be avoided.
There are many strategies organizations can employ to make their workforce safer. This article will highlight how focusing on training employees on how to properly fit, inspect and use their fall protection harness is an effective strategy to protect their workers.
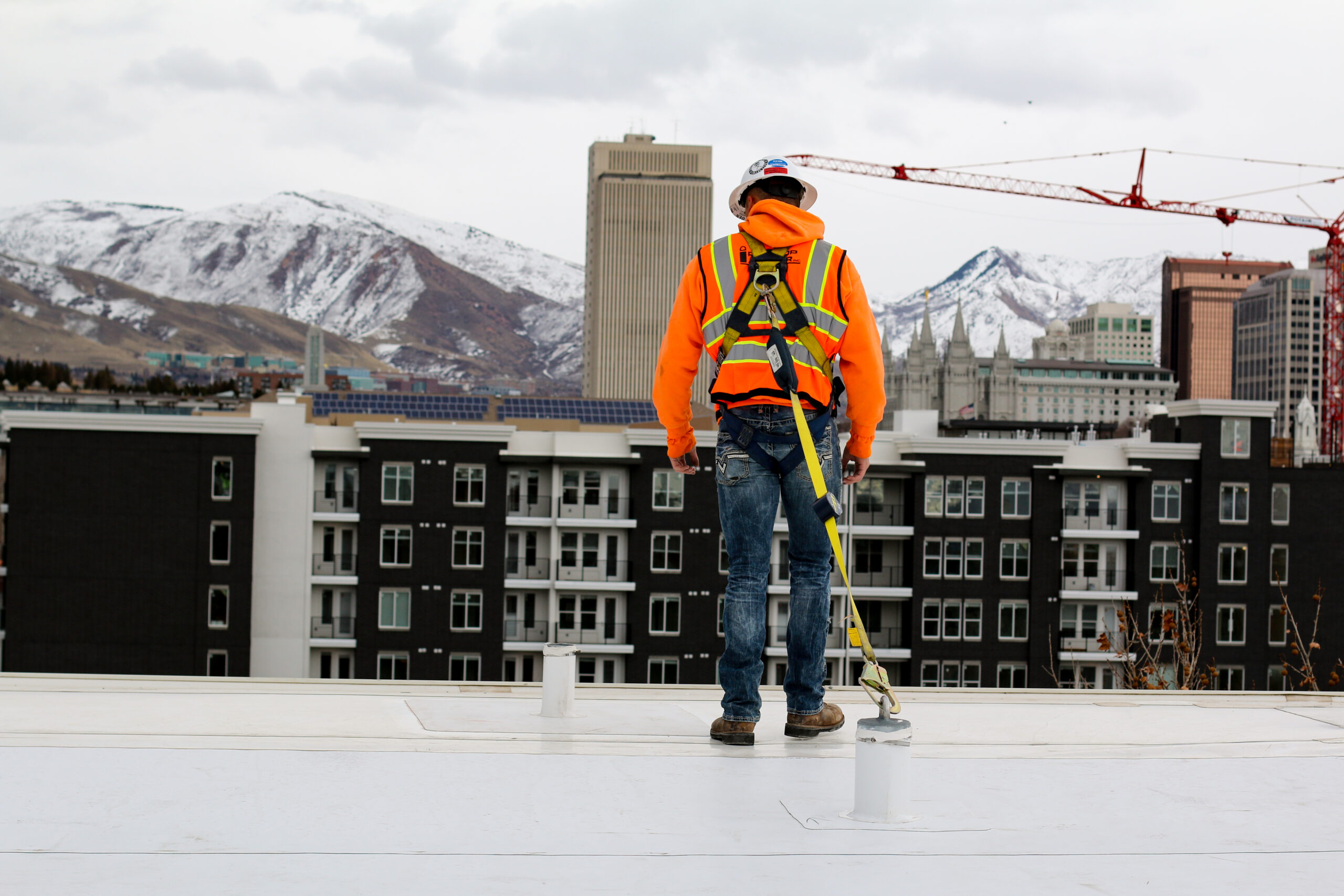
Ensuring a perfect fit for fall protection
Many harness manufacturers advertise body harnesses with a universal size, but each person must ensure their harness is properly adjusted to their body. Every OSHA and American National Standards Institute (ANSI)-approved fall protection harness will have five points of adjustment — two leg straps, two shoulder/torso straps and one chest strap.
The leg straps should be adjusted tightly enough to remain stationary on the user’s leg but not so tight as to cut off circulation. One common rule to determine leg strap tightness is called “flat hand, not fat hand.” This is where a user’s extended palm (flat hand) but not their fist (fat hand) can comfortably slip under the leg strap when tightened.
The shoulder and chest straps should then be fitted in unison. Users should ensure their shoulder straps fit snugly by pulling on the tensioners located near their torso. The user should feel slight tension on their shoulders from these straps and they shouldn’t be able to slip off while moving around. If the shoulder straps are properly tensioned, they should help the chest strap sit in its proper place, which is aligned with the creases created by a user’s armpit when they hold their arms flat against the side of their body.
It is important to have the chest strap set at the proper height. If it’s too high, the user risks being choked by the chest strap, as it may elevate when the user is suspended during their fall arrest. A strap that’s too low could cause the worker to not remain upright during fall arrest. If a user is not properly positioned upright during fall arrest, the user’s spine may incur more force and resulting in a greater risk of severe injury. Most chest straps are adjustable and should be tensioned to sit flat against the user’s chest.
Proper tension is crucial to ensuring a worker remains safe during fall arrest. A properly tensioned harness encourages the user to maintain a proper, upright posture. It keeps the body stationary during fall arrest, which best mitigates the fall forces that the harness can partially absorb during fall arrest. If a harness fits loosely, the harness will suddenly become very tight in crucial areas, like the groin or pelvic region. This sudden tightening of the harness can cause unanticipated injury and will not properly absorb forces from the user.
Fall protection manufacturers must ensure no more than 1,800 pounds of force are felt by a user in their harness. However, this can only be performed if the user wears the harness correctly, according to the manufacturer’s instructions.
Conducting pre-use inspections to ensure workplace safety
While proper harness fit is one of the most important things users can check while donning the equipment, OSHA also requires users to inspect their harness before every use. This is often referred to as the pre-use inspection. These inspections do not have to be documented each time they occur, but the existence of them and training workers to perform them should be documented in the organization’s fall protection program. In these inspections, users should check inspect three main components of their harnesses:
-
Product tag
-
Deployment indicators
-
Damage and defects
First, users must ensure the harness’s original product tag is intact. If no manufacturer tag is present, OSHA does not permit the harness to be used. On most harnesses, this is located under an enclosed pouch either on a front torso strap or one of the back straps. After locating the tag, users must make sure the tag is legible and in good condition. The tag should contain confirmation that it complies with the latest OSHA and ANSI standards, date of manufacture and make and model of the harness. While it’s not required, it is best practice to write the date of first use on the product’s tag.
Second, users must ensure the deployment indicators do not indicate a fall has occurred with the harness they are about to use. All pieces of fall protection equipment – anchors, body harnesses and connection devices – are only rated for one fall. After they experience a fall, they must be removed from service and replaced with new equipment, per OSHA and ANSI requirements.
Most harnesses now have two deployment indicators on the two back straps of the harness. They typically look like a piece of the webbing stitched over itself in a “Z” shape with stitches that are rated to break after about 400 pounds of pressure are applied, which is common in any fall arrest. Many manufacturers conceal a small tag that is revealed once these stitches break apart, which communicates that the harness should be removed from service. In the odd case that these stitches tear and the user has not experienced a fall, the harness still must be removed from service. This can suggest the harness has somehow been exposed to extreme forces and may not perform as expected during a fall. When it comes to fall protection equipment, being prudent can be the difference between life and death.
After the user has confirmed the product’s tag and the harness’s deployment indicators are still intact, they now must inspect the entire harness for any physical damage or defects that could hinder its performance during fall arrest. Users should check for any tears, cuts, holes, burns, burrs or damage done to the harness webbing. Harness webbing should have a smooth, sheen feeling to it if it’s in proper condition.
Overexposure to sunlight’s ultraviolet rays will not only discolor the harness but make the webbing more brittle, give it a rougher texture and erode its elasticity. If the webbing becomes too brittle, it won’t stretch properly during fall arrest and run the risk of breaking. If a harness strap breaks during fall arrest, the user could be accidentally ejected from the harness and suffer severe injury.
The user should check all the metal components of the harness, like the D-rings, buckles and grommets, for any rust or signs of corrosion. And while it is uncommon, they should pay extra attention to any area where metal comes in direct contact with webbing material because over time, the friction could deteriorate that portion of the webbing. They should also ensure all connections and fasteners function properly before donning the harness and going to their elevated work location.
If a harness or any piece of equipment fails its pre-use inspection, the item must be taken out of service and delivered to the organization’s “competent person,” defined by OSHA as someone who has the knowledge, training and experience to identify and correct hazards in the workplace. The user would then have to be provided with another piece of equipment before their at-height work can safely be performed.
Here’s why annual inspections are critical for safety
In addition to pre-use inspections, OSHA also requires annual inspections of all fall protection equipment. These inspections must be documented when they occur and be performed by the organization’s designated competent person. Annual inspections should note the date of manufacture, serial number, manufacturer and model and indicate whether the equipment passed or failed the inspection.
These inspections can be performed by a third party, and that third-party inspector must be trained to a competent person level. This person assumes liability for the proper functioning of the system if used according to the manufacturer’s instructions.
In theory, if users perform diligent pre-use inspections of their fall protection equipment, the competent person should have almost no equipment fail their annual inspection. High failure rates during annual inspections can indicate to safety leadership that workers should be retrained on what to look for during pre-use inspections. Workers using defective, damaged or faulty equipment could be subject to injury but might think their equipment will protect them.
Best practices can ensure fall protection safety
Focusing on best practices for fall protection harnesses is just one strategy organizations can deploy to better protect their workers from falls. The simple reinforcement of corporate safety policies and encouraging workers to use their equipment properly is extremely effective in keeping workers safe.
Studies have found that employees are eight times more likely to use fall protection equipment if they believe their employer requires it. If we educate workers on the hazards they will encounter in their workplace, provide them with the resources to work safely and empower them to use their equipment every time, we can prevent falls — and avoid tragedies.