Streamline systems to drive down costs
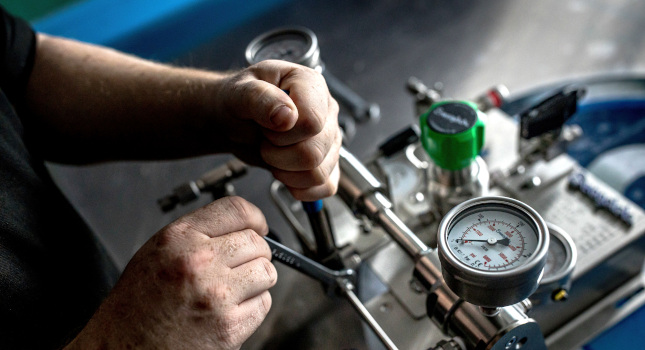
Ensuring a safe, continuous supply of primary and specialty gases to support critical processes is important to many laboratories, test centers and industrial sites. Responsibility for making sure gas distribution systems are functioning at peak performance often falls to lab and reliability managers, engineers and operations staff. Unfortunately, many operations face limited internal resources and inefficiencies that can make it difficult to properly maintain these systems.
If gas bottles are used inefficiently or leaks remain undetected, for example, facilities can accumulate unnecessary costs (see Figure 1). Some facilities also do not have accurate line drawings of the systems, which can make it difficult to diagnose problems. Finally, untimely setbacks and costly delays can occur if tests must be repeated or the results are deemed inaccurate.
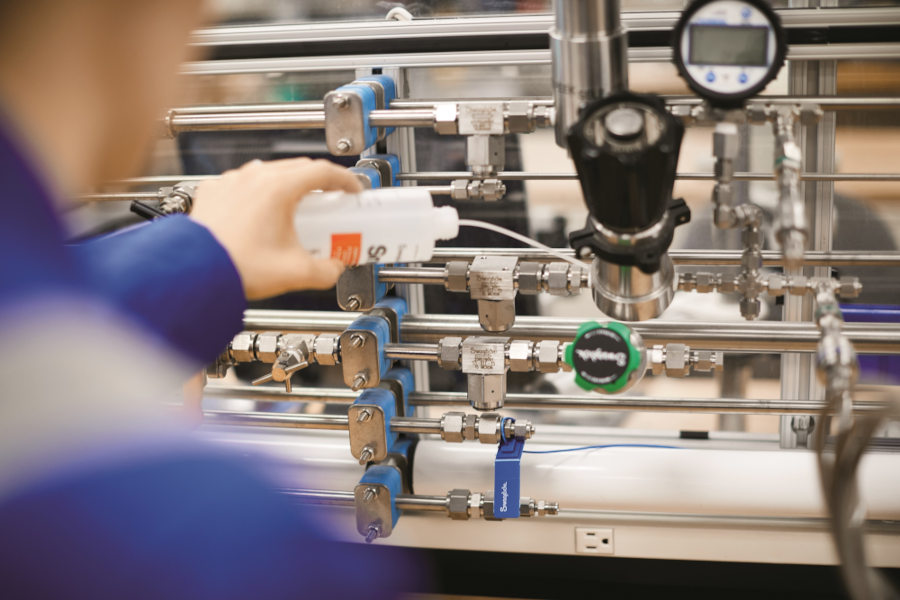
To improve evaluations of gas distribution systems and identify any problems, facilities can hire experienced outside consultants to look at the systems with an unbiased eye and locate areas for improvement. Having this fresh perspective will often lead to the discovery of trouble spots that otherwise might be overlooked. The practice provides an opportunity to eliminate all previous assumptions and evaluate how a system has been built from the ground up.
Why challenges occur
Design inefficiencies, malfunctioning components or other factors can prevent a system from operating properly. For example, improper regulators can have an enormously negative effect on system performance. Choosing the right regulators is a specialized skill that not all facilities might have onsite, so it can be helpful to work with a supplier to ensure these components are right the first time.
Since systems are complex, it is often difficult and time-consuming to address all of the issues facing gas distribution systems. Plant managers may be addressing other, more obvious challenges that need immediate attention, or they may not be aware of the issues the systems are facing altogether. This can lead to lingering issues that can cost facilities money in the short and long term. To keep that from happening, an experienced outside field engineer can help build the system properly by specifying the best components and alerting plant managers to inefficiencies that may be present.
Systems and savings advice
Most gas distribution systems focus on regulating the pressure of the gases they transport and usually are made up of four subsystems: a source inlet connection, a primary gas pressure control, an automatic changeover and a point-of-use control.
The source inlet (See Figure 2) connects the high-pressure gas source to the gas distribution system. Importantly, the inlet must be built with appropriate cylinder connections, hoses, tubing, filters, vent, purge and relief functions. Some gas panels may not include a standard source inlet. Always verify componentry and that panels will use the correct cylinder connector. Some high-pressure and/or hazardous gases (including oxygen) also require the use of special construction materials.
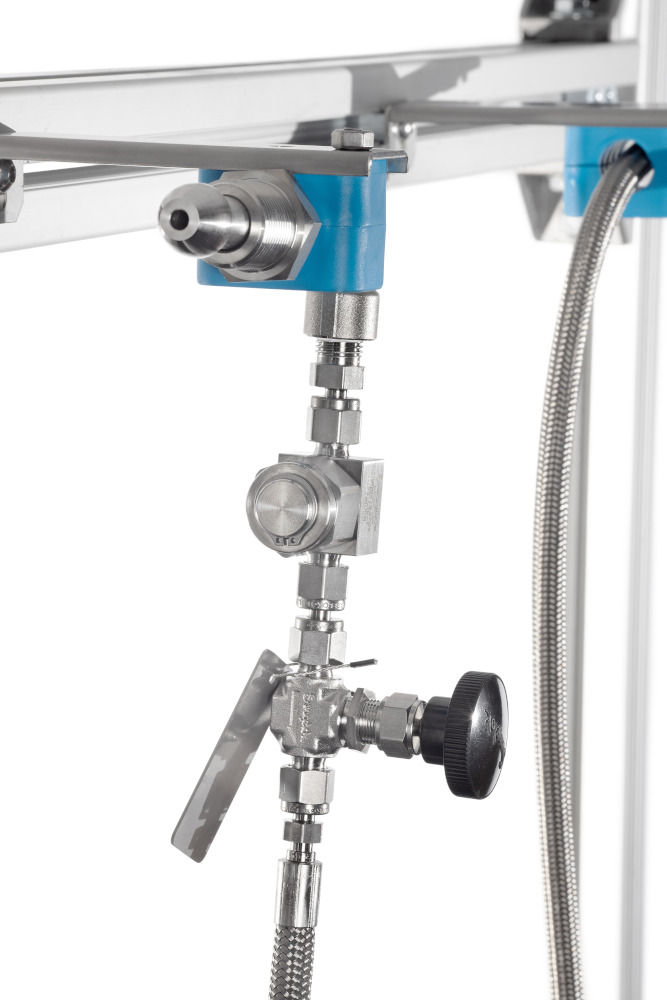
The primary gas pressure control (see Figure 3) completes the first pressure reduction and ensures the source gas is delivered at the correct flow rate to the next stage of the system. Reduction is accomplished with either a single pressure regulator or through a dual pressure regulator arrangement. Pinpointing correct inlet and delivery pressures is challenging. It is important, for example, to consider the differences between media, such as ammonia that is bottled around 116 psi (8 bar) and nitrogen that can be bottled at 4351 psi (300 bar). Meanwhile, many bottles that use a two-stage pressure regulator may not, in fact, require one. This can be a cost-saving opportunity.
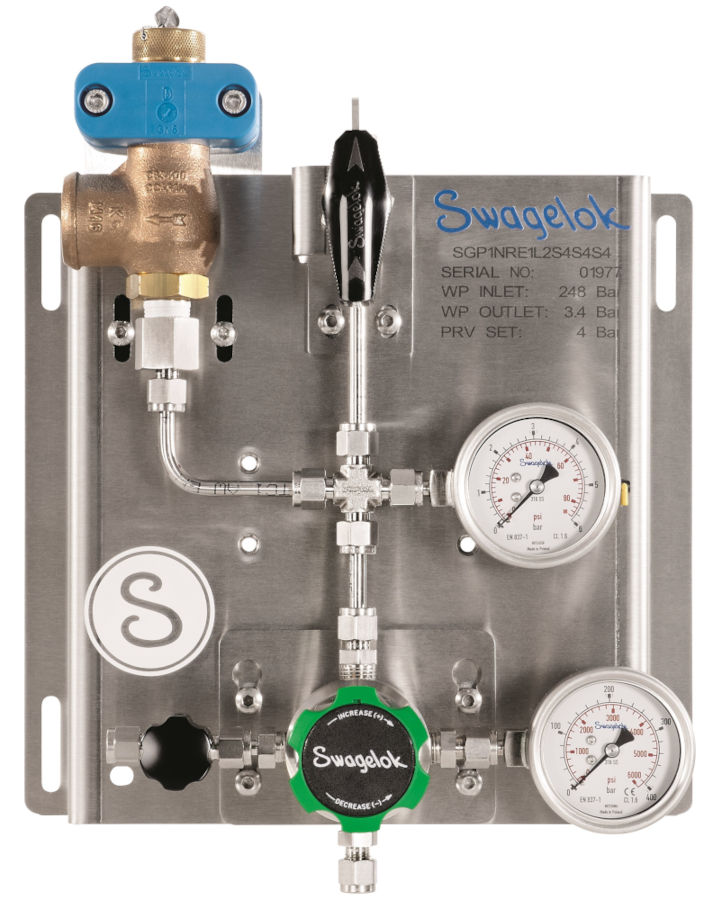
The automatic changeover (See Figure 4) seamlessly switches from one gas source to another to ensure an uninterrupted supply. This is performed through staggered set points of two pressure regulators, allowing the system to continue to operate as the primary gas source is changed. It is advisable to look for a solution that allows for varying changeover pressures to get the most use from gas bottles.
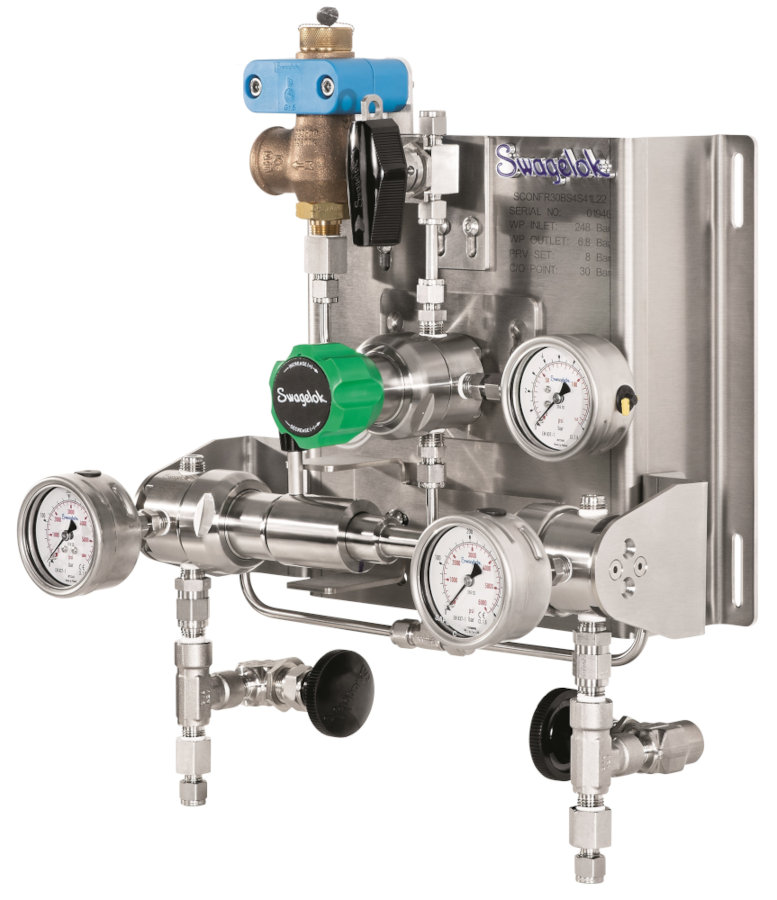
The point-of-use (see Figure 5) provides the critical last stage of control. Typically having a pressure regulator, gauge and isolation valve, these subsystems give operators a convenient and accurate method for adjusting pressure. Where varying line pressure between the primary gas pressure control and point-of-use is acceptable, a single-stage pressure regulator might be used to reduce cost and complexity.
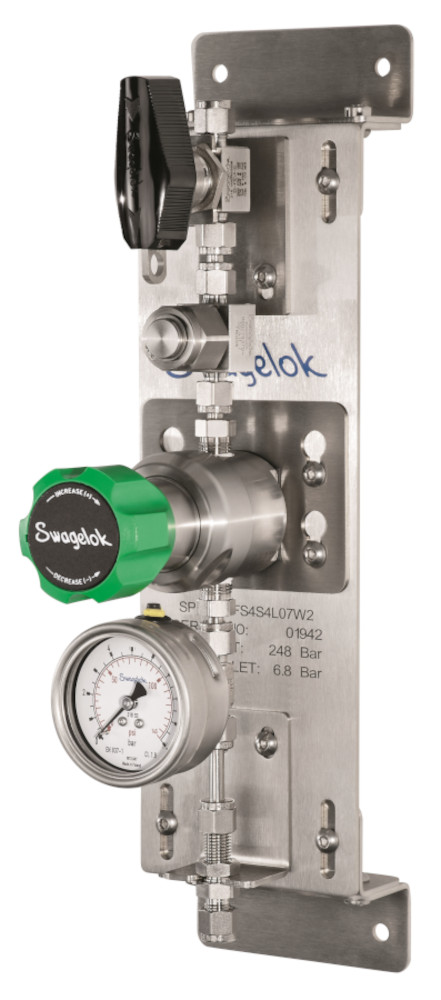
Quality parts, fewer interruptions
Choosing quality components for gas distribution systems is critical to their operational success. If systems are constructed from high-quality components, the cost of maintenance-related labor will decrease, thereby increasing a facility’s overall profitability.
Gas distribution systems should also be designed so they can be serviced more easily. To reduce the amount of time it takes to access components for repair or replacement, facility managers should use compression fittings in place of threaded fittings. Not only do these fittings allow the flexibility to change components instead of replacing entire panels, they provide technicians with the ability to work more efficiently while also reducing the possibility of doing accidental damage to components as the repairs are being done.
In addition, facilities should emphasize the need for high-quality regulators because they are such critical parts of gas distribution systems. The best quality regulators have been tested and rated for millions of cycles and can last as long as the system is in operation. Installing proper regulators can eliminate the need to replace them at all, lowering labor costs and potential downtime while simultaneously improving the performance and safety profiles of the systems.
Specialists add value
When in doubt, it may make sense to bring in professional pressure control advisors to evaluate the system for upgrade opportunities, provide guidance on proper regulator sizing and selection, and oversee the design and assembly of engineered solutions. Advisors who have familiarity with the particular challenges of gas delivery can offer:
• Suggestions for how existing systems can be modified to meet new requirements (often, old panels are disposed of unnecessarily – be sure to ask about solutions designed to last)
• Options for easy procurement of gas panels built and tested by experienced installers working in suitable facilities (potentially reducing time, cost and risk as opposed to panels assembled onsite by less-practiced installers)
• An unbiased recommendation that puts the needs of the business first (an advisor having no prior ownership stake in the system or its operation can offer impartial advice)
Advisors can also help prevent the leakage of toxic and flammable gases, as well as make sure the panels are clearly labeled and the instructions are clear. Finally, they can offer guidance on how to design systems properly, so they are easy to operate and troubleshoot (See figure 6).
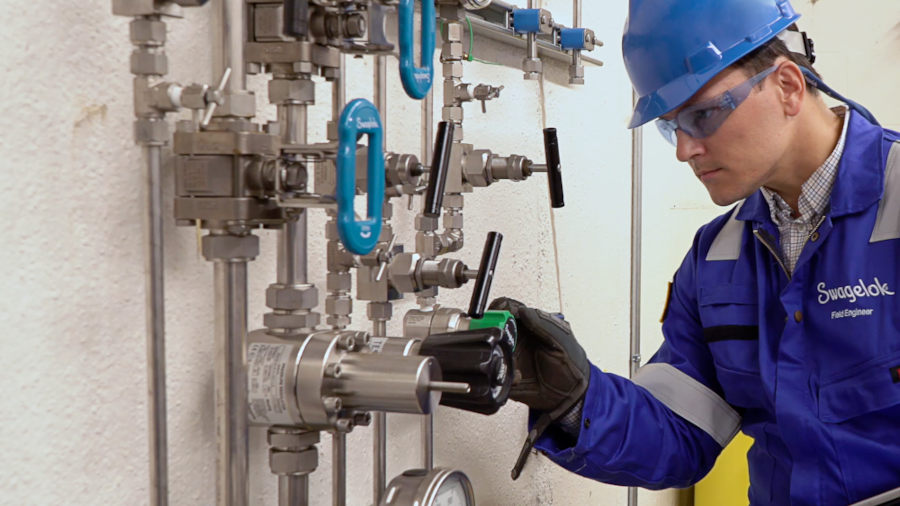
No matter what needs to be accomplished with a facility’s gas distribution system – whether it is a complete replacement or just trying to understand why the facility is replacing gas bottles before they are empty – external pressure control specialists can help diagnose problems and suggest cost-effective solutions. These contributions will help facilities maximize their investments in gas distribution systems and protect their bottom line.