Quality finished products begin before raw materials are ever combined
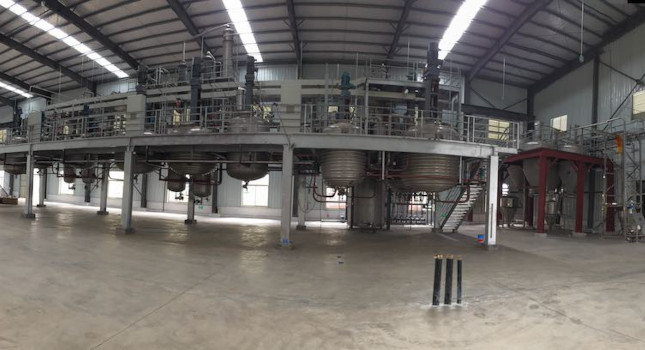
Engineering excellence insights
- Weighing is critical to the quality of the finished product and original equipment manufacturers (OEMs) depend on them to making sure each application’s materials mix perfectly.
- Dongguan Hangda’s synthetic rubber customers’ products need to reliably measure outputs from the feeding station because otherwise the resulting rubber recipe could be compromised.
Original equipment manufacturers (OEMs) depend on reliable weighing technology so they can deliver to their customers systems that will ensure high-quality products, reliable monitoring, and intelligent diagnostics.
Located in southeast China, Dongguan Hangda Industrial Measurement and Control Technology Co., Ltd. has been designing and building high-precision weighing and mixing/batching systems since 2018.
The company specializes in equipment for industries that manufacture rubber and plastic, food, and chemicals. The majority of Dongguan Hangda’s clients are located in China, with specific applications in these process industries that include, small and ton bag feeding stations, loss-of-weighing feeders and conveying and metering integrated machines, and other equipment.
In each of these manufacturing systems, weighing is critical to the quality of the finished product—making sure each application’s materials mix perfectly before being shipped to end customers worldwide.
Engineering the right mix
So how does Dongguan Hangda engineer quality assurance into a piece of equipment like their integrated conveying and metering machine?
It starts with the right mix of raw materials coming from the system’s feeding station. The company’s engineers use their years of experience and technical expertise to design and then assemble the right system of components, resulting in tailor-made applications specific to a particular customer’s process requirements.
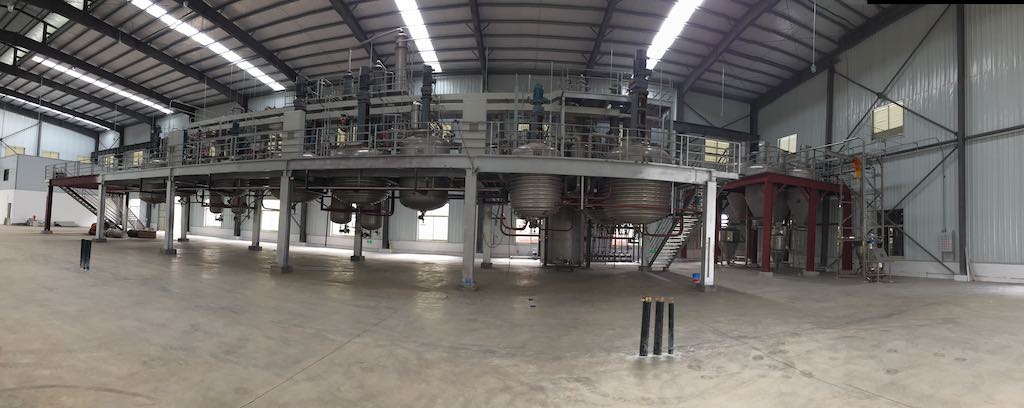
Once the system is up and running, the integrated conveying and metering machine automatically extracts raw materials from each feeding station and then sends these materials to the next level of equipment such as the reactor or internal mixer.
To improve accuracy, avoid raw material waste, and meet strict environmental protection requirements, the integrated conveying and metering machine is also equipped with automatic purging and dust collection devices. All of this helps ensure the right mix, every time.
And Dongguan Hangda knows how important the right mix is for their customers’ finished products. Any instrumentation—like the machine’s integrated weighing system—must therefore have powerful diagnostics and alarm functions to avoid the wrong measurement.
Take synthetic rubber, for example. The substance is made of raw materials like butadiene, styrene, and isoprene—small molecules called monomers which join with others to become the polymers that form the basis of the finished rubber.
Product qualities like elasticity, hardness, and moisture content are critical to Dongguan Hangda’s synthetic rubber customers’ products. If weighing technology doesn’t reliably measure outputs from the feeding station, the resulting rubber recipe could be compromised.
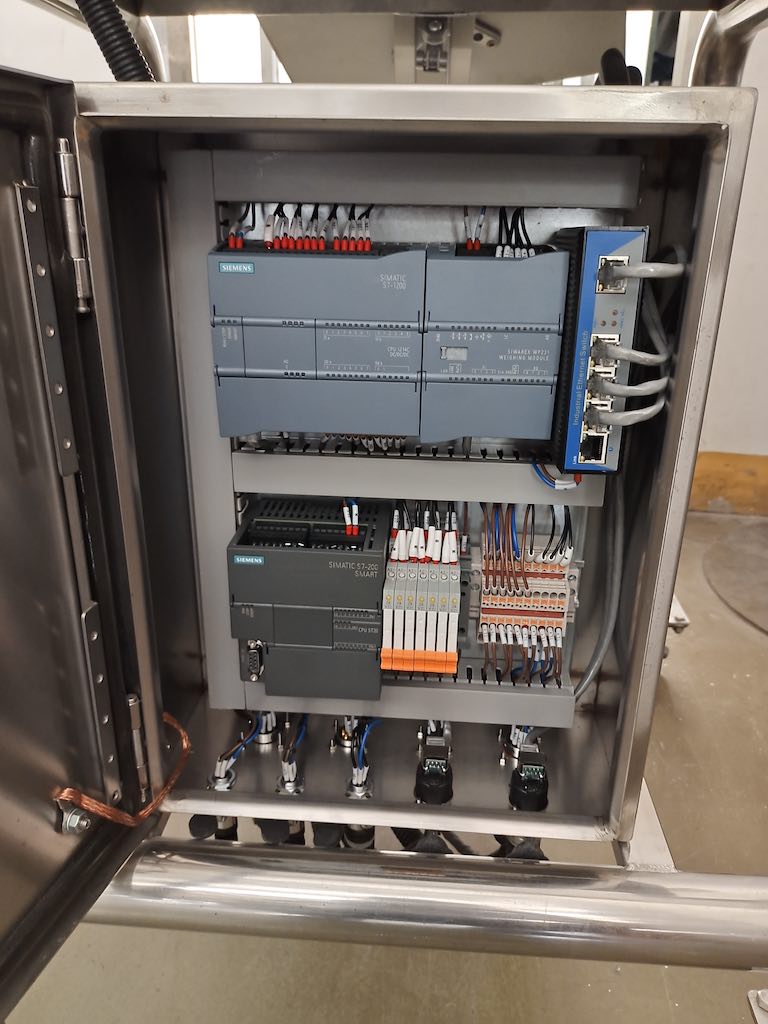
Delivering accuracy and reliability
Built into Dongguan Hangda’s systems is reliable, accurate weighing devices from Siemens. The programmable and integrated SIWAREX weighing technology enables customers to independently monitor the operation and fault status of each weighing sensor, providing diagnostic functions that technicians depend on.
Installing the weighing system is straightforward and quick: technicians connect the integrated conveying and metering machine’s load cells to a SIWAREX DB digital junction box, allowing for targeted monitoring of weighing processes as well as enhanced diagnostics. The junction box is then connected to a SIWAREX WP2x1 weighing module. Thanks to automatic adjustment, the application is up and running in only a few minutes.
Finally, operators integrate the weighing solution into the SIMATIC S7-1200 control system, delivering high-speed data communication and control between the instruments and control room through this seamless, integrated system.

The benefits of a solid build
Why do Dongguan Hangda’s engineers choose SIWAREX weighing technology? Siemens understands the needs of OEMs, supporting its customers through all steps of development, from planning to maintenance of components and manufacturing systems.
This solution’s high-speed weight data and control signal are integrated between the weighing equipment and control system so operators can access the status information of each weighing sensor to ensure reliability in the weighing and batching process. If raw material feeds supply the wrong mix of ingredients, the SIWAREX WP2x1 will send an alarm directly to the control room to stop production and alert technicians that a problem has occurred.
The programmable and integrated SIWAREX weighing technology enables customers to use the SIWAREX WP2x1’s extension module in a variety of weighing applications. The device offers four digital inputs and outputs and one analog output, with extensive diagnostic functions for commissioning and operation like trace of weight or monitoring of limit values.
“With the weighing modules connected to the SIWAREX DB digital junction box, our customers can now independently monitor the operation and fault status of each weighing sensor,” said Lv Yang, General Manager, Dongguan Hangda. “This provides them with the best in diagnostics and real-time monitoring of their production processes.”
With its decades of experience with OEM builds like this at Dongguan Hangda, Siemens ensures product quality, reduced waste, and adherence to environmental regulations—delivering intelligent, accurate weighing that works.