Webcast presenter Lanny Floyd explains what causes an arc flash event and how to prepare for them. He and co-presenter Bibek Karki also answer audience questions.
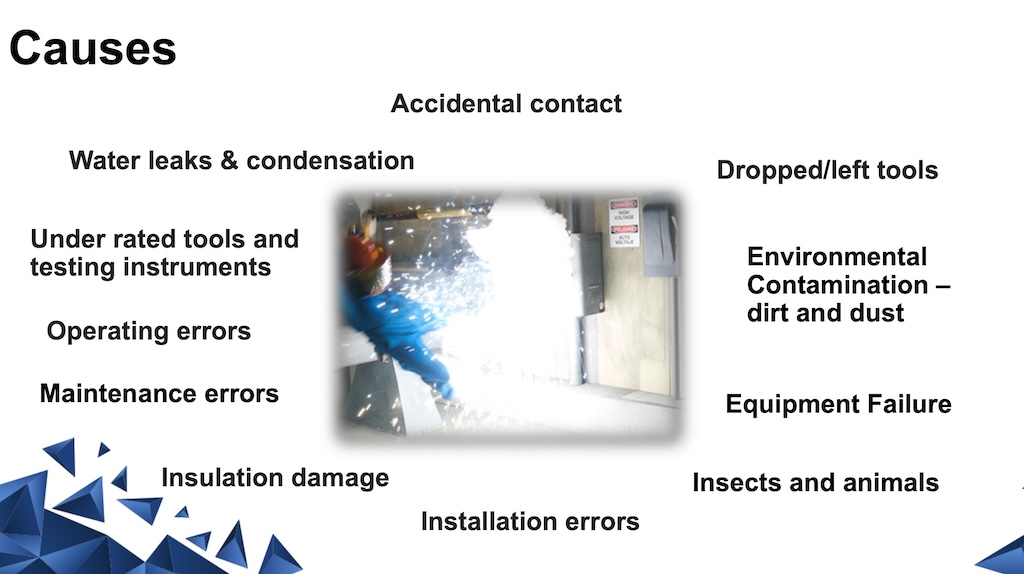
Arc flash and electrical safety insights
- Fundamentals and prevention: Understanding arc flash fundamentals is vital for safety. Regular arc flash studies can significantly reduce risks by identifying opportunities for engineering design changes, thus decreasing exposure severity.
- Causes and consequences: Arc flashes can result from human error, equipment failure, and environmental factors. They pose severe risks including burns, equipment damage, operational disruptions, and potential fatalities, emphasizing stringent safety measures.
- Mitigation strategies: Implementing maintenance reduction switches and zone selective interlock systems during the design phase are effective strategies to mitigate arc flash hazards by reducing fault clearing times and incident energy.
Arc flash and electrical safety are critical aspects in a manufacturing facility. Knowing and understanding the fundamentals often mean the difference between life and death. Companies and workers need to stay on top of the electrical codes so they can better protect themselves from a potential accident.
In a manufacturing facility, an arc flash is a dangerous release of energy caused by an electrical fault that occurs in equipment such as circuit breakers, switchgear and other electrical components. This can happen during normal operation of the equipment, as well as during maintenance or repair. The intense heat and bright light generated by an arc flash can cause severe burns and other injuries to workers, as well as damage to equipment and facilities.
An arc flash event can be triggered by several factors such as human error, equipment failure, corrosion, dust, moisture and others. Such an event can happen in several ways, such as a short circuit, a ground fault, a loose connection or a failure of insulation.
Lanny Floyd, partner and principal consultant, Electrical Safety Group and Bibek Karki, power systems electrical engineer for IPS, discuss arc flash and electrical safety and what engineers need to know from the June 20, 2024, webcast: “Electrical safety: Know the fundamentals of arc flash mitigation.” This has been edited for clarity.
Lanny Floyd: What I’d like to do now is give some examples of what causes an arc flash event. How do they start? These are not in any order other than alphabetical order. They all can cause an arc flash event. Depending on your work environment, the industry you’re in, some of these causes may be more prevalent than others. But one thing I’d like to mention also, going back to something Bibek said, he gave it the case history of where through an engineering design change, you went from 137 calories per square centimeter to about 6.9. It’s important to understand that when you do your arc flash study, it’s not just about figuring out what PPE you need to wear, it’s also about looking for opportunities to apply concepts like that. I mean, reducing the severity of the exposure by orders of magnitude is not unusual.
That is probably, I view it as one of the most valuable outcomes of an arc flash study is learning where you can reduce exposure to changes in design. All right, so let’s go to look at the causes. At the top, again, in the center here we see an arc flash event, we see a person, they’re wearing a blue coverall there is being blown away. And so what caused that event? Well, it could have been accidental contact and that is where a person while they’re performing work in and around exposed parts unintentionally or maybe intentionally thinking that it may be de-energized, but they come in contact with an energized part and that initiates an arc flash, that creates a path to ground for an arc to start. It could be someone left a tool in or drop the tool into energized parts.
It may be environmental contamination. That could be either dirt, dust, we’ll talk about water leaks in a minute. It could be equipment failure. The equipment fails in such a way that an arc flash is initiated. It could be insects and animals building nests, building a home inside electric equipment that can be in a position to initiate an arc flash event. It could be an installation error, something that was installed incorrectly and maybe it’s been there for a long time just waiting for the right opportunity and the right set of circumstances for something to go wrong and create an event. It could be insulation damage, it could be a maintenance error. In other words, if someone left a part out, put a part in backwards, left it loose, didn’t tighten it properly. It could be an operating error where a person does something while they’re operating a switch or a piece of equipment that is not the intended way to do that and it could cause an arc flash event.
It could be caused by using tools or test instruments that are not rated for application in that work environment. It could be water leaks and condensation. And what I’d like to do is we’ll look at a couple of these specific items here in the next slide. Over on the left, if you can see my cursor, if not, just take my word for it. Here’s a screwdriver that’s laying on top of a 480 volt termination block. It was left there by either during installation, it would be an installation error or during maintenance, that would be a maintenance error. And just because it’s laying there may not be a problem in itself. However, things happen in that equipment that can cause that tool to move.
Contractors are banging in and out, switch handles are being thrown open and closed, doors are being open and closed. All of that creates mechanical energy that could translate into causing that tool to fault down and short out, initiating an arc flash at the time a person is standing there at the equipment. That’s a bad time for it to happen. Over the right we see this is an infrared photograph or infrared image I guess you would say of three terminal connections. And we can see one is glowing, brilliant white, yellow, and that’s indicating a loose connection. Okay, this slide illustrates a couple of things. One, that infrared tomography is a great maintenance tool to identify things such as loose connections or hotspots in your equipment. And also this is when a connection is loose, it means that it is moving toward a position where it’s going to start arcing and that could be arcing from the conductor parts or it could be arcing from the conductor parts to ground, then that can initiate an arc flash event.
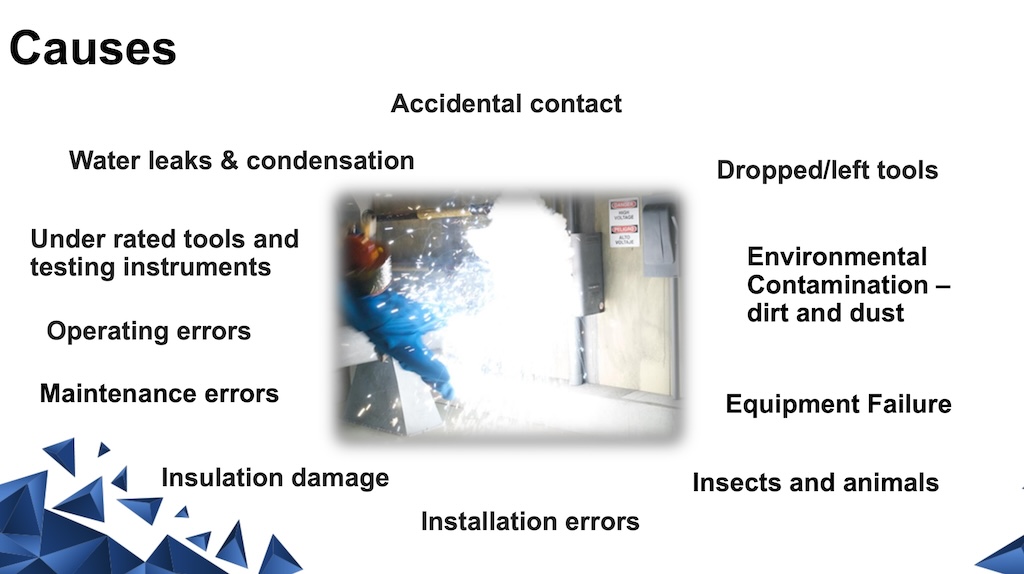
It could be using, I realized after I did this that underrated tools could be interpreted several ways, maybe best to say improper tools. Now over on the left we see two fellows that are doing some testing in an electrical panel. And you could ask the question, what’s wrong with this picture? Well, if the equipment is de-energized and in an electrically say, work condition, just the fact that they don’t have on PPE is not a problem. However, we don’t know that, maybe they don’t know that. If that equipment is energized then there’s a lot wrong with this picture. Now what I’m showing here on the right is the results of a test instrument that was improperly applied to some electrical equipment and it didn’t have the proper, it’s commonly referred to as the CAT rating. And what that CAT rating means on voltage testing instruments is the ability of the instrument to withstand voltage transients that are coming from the electric utility supply or voltage transients can also be caused by equipment internal to the industrial facility.
If the voltage transients exceed the rating of the instrument, you can end up with an instrument failure like this that it would initiate an arc flash event. It’s very important that you have properly rated instruments. In industrial facilities a CAT rating one or two is what you need to be doing, using. And let’s see, next slide we’re looking at some water leaks. Over on the left, may be hard to see in the slide, but you can see the bottom of this cabinet is brown, that’s corrosion. That’s an indication that water is getting into that and sitting in the bottom, it’s running down, there’s a little corrosion there on the top of some hardware there on the right-hand side. And water and electrical equipment just do not work well together if it’s not rated. You can have enclosures that are designed to protect the equipment from water intrusion.
They have to be installed properly and conduit fittings have to be installed properly to maintain that rating. Over on the right, this is not a leak. This is, what we’re looking at here at the bottom, sort of in the center of on the right is an electric heater that’s in medium voltage switch gear. That electric heater is designed to maintain the internal temperature of the equipment a little higher than the external temperature on the outside of the equipment. And that’s important to prevent condensation. Now when I investigated this failure, I found out that the heater had never been connected. It had been installed and the wiring taken out to a terminal block, but no electric power had ever been connected to the heater. It had been there a long time, but you can see it eventually failed due to condensation and tracking on some insulating boards or insulating parts.
You can see the rust. These space heaters are very critical to preventing electric arc flash events. All right, and let’s see. Okay, here’s an example of catastrophic arc flash event. In the picture there in the center at the bottom, we’re looking at 480 volt switchgear draw out circuit breakers. The entire set of switch gear is wrecked, it’s destroyed. Every compartment, every circuit breaker is damaged beyond refurbishing. We can see in the little single line diagram on the left that an arcing fault developed in one of the circuit breakers. Now when this arc initiated, what was supposed to happen is the 15 KV circuit breaker on the primary, there were secondary CTs on the secondary of the transformer to look at faults on the secondary bus that was supposed to trip the primary breaker. However, over on the right-hand side you can see the arrows pointing to a trip coil.
What we found was the trip coil had failed. So this photograph at the top of the 15 KV circuit breaker was taken after the fault. It’s in perfect condition, there’s no damage at all. The only thing wrong is that the trip coil was burned out, it didn’t work. And what that meant was that the fault on the secondary side in the 480 volt side was not limited to just one circuit breaker. It was allowed to arc for seconds, many seconds engaging the entire lineup of 480 volt circuit breakers. You can see that, imagine now that it is not only the cost of the repair but the interruption to the manufacturing operations that was more than two weeks, very costly. All right, so here we have a hidden failure and a catastrophic consequence. All right, this is why maintenance is so critical to preventing arc flash events.
So let’s talk about the consequences. What happens if an event happens, if an arc flash event happens? In the center, we see some medium, this is actually 480 V circuit switch gear. This event happened while a person was racking in the 480 volt circuit breaker here, where most of the black marks are there on the front, on the right-hand side. In the center of the photograph, maybe it’s hard to tell in the slide, but that’s a three-inch hole that has been melted through the sheet metal of the switchgear. At the time this arc event happened, a person was standing in front of this gear racking the circuit breaker in with the door closed.
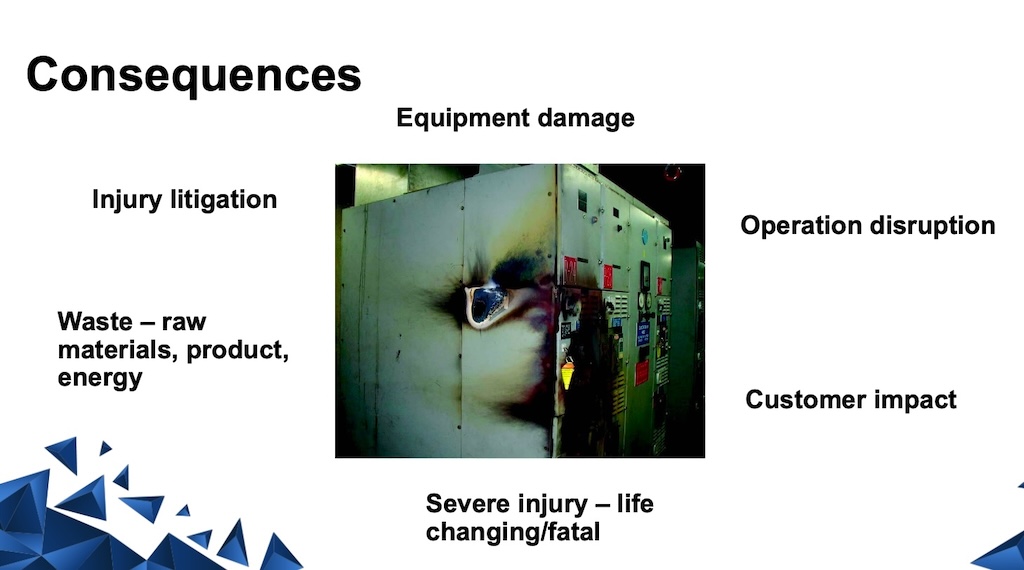
That person was also wearing properly rated flash arc rated gear, but still received some minor injuries. It’s important to recognize that PPE doesn’t necessarily prevent injuries. It can serve to reduce the severity of injuries. But let’s look at the consequences of this. Certainly you can see that we have equipment damage. This is critical equipment, part of the power system infrastructure critical to the plant operations. So we have operations disruption. How long was the operation disrupted due to the loss of this equipment? That could vary. There were customers impacted because due to the operations disruption, unhappy customers.
We also had the potential for a very severe injury. Life-changing long-term permanent disabling injury, could have been fatal, especially if the clothing had ignited. If this person was not wearing arc rated protective clothing, if he was wearing flammable clothing when the clothing ignites, that creates horrible burns. So that could be a consequence. A lot of waste associated with this failure. Raw materials, product wasted, energy wasted. The plants, there’s still lights on and lots of things going on in the plant, but they’re not making anything because of we don’t have the power to run our manufacturing equipment. You can also have injury litigation, the cost of litigation, especially if the injury results in life-changing permanent disabling injuries.
So there are many consequences and it’s important to recognize that PPE does not prevent the equipment damage, does not prevent operation disruption, does not prevent the customer impact, does not avoid the waste of raw materials. The PPE is about protecting the person after the event is initiated and that’s where it comes in. And preventing injury and minimizing any injury litigation you may have half.
Question, answer session
Question: Are there examples of when miscoordination would be acceptable to avoid lower arc flash incident energy and what kind of arc flash requirements do you expect to see in NFPA 70 in the future?
Lanny Floyd: Excellent question. I think the miscoordination is when you sacrifice reliability of operations for the benefit of reducing exposure. That’s where one, I don’t know if Bibek covered this, but one of the techniques is a maintenance reduction switch. And that’s when you install a switch that temporarily while you’re performing a task, whether you’re racking in a circuit breaker or operating a switch or something that you place the maintenance reduction switch in the reduced exposure mode and that changes the coordination setting of protective relays for the short period of time of when the exposure occurs.
When you finish the task, you put it back into the normal operation so that you restore your coordination. That would be one thing to do. If you’re not able to do that, then you need to have a discussion with the operation maintenance and safety management involved on what are the trade-offs we are willing to accept? Are we willing to trade off miscoordination? Are we willing to trade off possible exposure to a more severe exposure to arc flash? So that requires a dialogue and I can’t say that’s always the same answer. It depends on the circumstances. Excellent question. But again, the maintenance reduction switch is a technology that’s been developed to address that question.
Bibek Karki: Yeah, again, agree with Lanny, Excellent question. On that 50P slide that I had mentioned about the maintenance mode switch that Lanny just talked about. So that is very, like Lanny said, it’s one of the most effective ways of mitigating arc flash hazard and again, sacrificing the coordination for the time duration of maintenance. I think that goes a long way. Good question.
Question: The next question actually is talking about 50P. Do you want to expand a little bit on that, Bibek?
Bibek Karki: So 50 is a ANSI device number that pretty much ANSI provides for instantaneous settings. Basically what 50 says is it’s instantaneous function, which means there is no intentional delay. So basically, I know that a lot of devices these days, you can program a delay to it, but 50 is basically if something were to happen on a protective system, you just trip. That’s it. So no incident on delay. That’s what I would say on 50.
Question: What are your thoughts on the two second arc time limit for trip times greater than two seconds?
Bibek Karki: So basically that’s a standard IEEE rule. Like Lanny had mentioned about IEEE 1584, that’s the standard all the softwares used to calculate fault current, previous trip clearing time. I mean, I understand it’s, we like to call it runaway rule because it’s basically if something were to happen, you have two second to get out of the hazard. I kind of like the rule, I would say personally, because like I said, it gives you enough time for operator to get out of hazards way. Also helps quantifying the calculations. Lanny, I could use some thoughts on this.
Question: How can zone selective interlock (ZSI) be used to mitigate arc flash?
Lanny Floyd: I think that is one of the engineering design solutions, I think. I’m not sure if Bibek actually addressed that specifically, but I’m pretty sure he has experience with that. It’s one of the significant engineering solutions to reduce incident injury. Bibek, you want to give some more details on that?
Bibek Karki: Yeah, so pretty much that’s something I did not include. However, like Lanny said, it’s excellent solution. You are basically decreasing your fault clearing time into few cycles. So it’s a very fantastic concept that can be implemented during the design phase and it’s an excellent solution, especially for 480 V system. A lot of the circuit breakers, any original equipment manufacturer (OEM) circuit breaker have capabilities of doing that. So it’s a very effective tool, yes.