It’s important to understand the advantages and disadvantages of flexible screw, aero-mechanical and vacuum conveyors when it comes to dry bulk material handling choices.
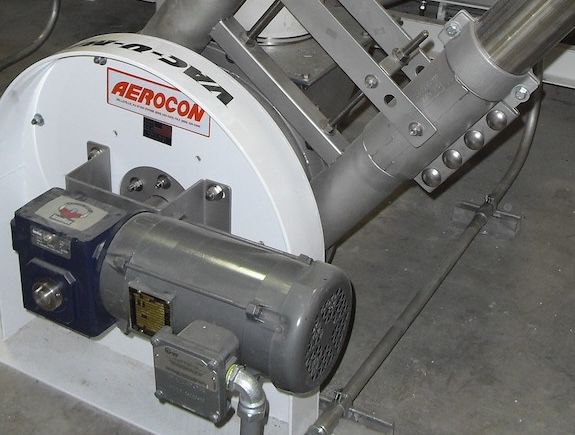
Learning Objectives
- Learn how automating dry bulk material transfer benefits for manufacturers.
- Understand the difference between mechanical and pneumatic conveyors.
- Learn how expert advice and thorough inspections can improve these conveyors.
Material handling insights
- Automating dry bulk material transfer enhances margins by reducing labor, increasing uptime, improving product quality and eliminating safety hazards.
- Expert consultation in dry bulk powder transfer is crucial for selecting the optimal system, considering factors like material characteristics and organizational needs.
- Mechanical and pneumatic conveyors each have distinct advantages: Mechanical systems are energy-efficient and less costly while pneumatic systems offer versatility and are easier to maintain.
With the right equipment, automating dry bulk material transfer delivers many benefits that translate to higher margins. These benefits include labor reduction, increased uptime, higher product quality, elimination of safety hazards, and preservation of expensive ingredients.
To reap the full benefits of automating materials transfer, facilities should seek out an expert in dry bulk powder transfer and not just the cheapest solution that may not deliver higher margins.
Handling powder and bulk solids is a specialized field with no two conveying applications quite the same. While two manufacturers might use the same material, utilize similar types of equipment or have similar processes, factors unique to each manufacturing facility and organizational objectives require considerations distinctive to the process. For one manufacturer a vacuum conveying system may be the solution, for another it may be a flexible screw conveyor, or the solution may be an aero-mechanical conveyor or the combination of both mechanical and pneumatic conveyors.
Conveyor manufacturers steeped with experience designing both mechanical and vacuum conveying systems to transfer dry bulk materials help processors and manufacturers weigh upfront cost, system benefits and down-the-line costs including maintenance, utility usage, cleaning, downtime and safety savings between systems.
There is a science to dry bulk material handling with formulas that determine system design based on factors including particle size, bulk density, conveying distance and rate. However, after all the science and spreadsheets, the success in designing a system that delivers peak performance while preserving product quality lies in the ability to understand powder characteristics and how those characteristics interact with equipment design. This type of tribal knowledge is not formulaic and draws upon decades of experience with tens of thousands of materials and their behaviors to augment scientific principles.
Working with a conveyor manufacturer that offers mechanical and pneumatic conveying technologies expands the range of solutions available for each unique application. This includes the ability to deliver fully integrated systems that combine mechanical and pneumatic conveyors, such as using a flexible screw conveyor to deliver product to a mixer and then a vacuum conveyor to convey product from the mixer to a packaging machine.
Automating dry bulk powder transfer eliminates the fundamental drawbacks of manual transfer such as heavy lifting, scooping, climbing and dust clouds created with manual dumping. Those innate safety hazards of manual materials transfer have the potential to whittle away profits through workman’s compensation claims.
In addition, manual transfer of materials often requires two operators working in tandem to reduce ergonomic risk when loading materials into process vessels. Automating the process eliminates the need for two workers, reducing economic pressures caused by manufacturing labor shortages.
Understand the difference between mechanical and pneumatic conveyors
Three of the most used technologies for automating bulk dry powder transfer are flexible screw conveyors, aero-mechanical conveyors and pneumatic conveyors.
The principal differentiator between mechanical and pneumatic conveyors is mechanical conveying uses a mechanical device which is in direct contact with transferred material. Pneumatic conveying uses gas (usually air) to transfer suspended material through tubes.
Another distinctive characteristic between pneumatic and mechanical conveying is pneumatic conveyors have virtually no moving parts, which makes cleaning and maintenance a breeze. Mechanical conveyors, with an array of moving parts, require more maintenance and more complicated cleaning procedures than pneumatic conveyors.
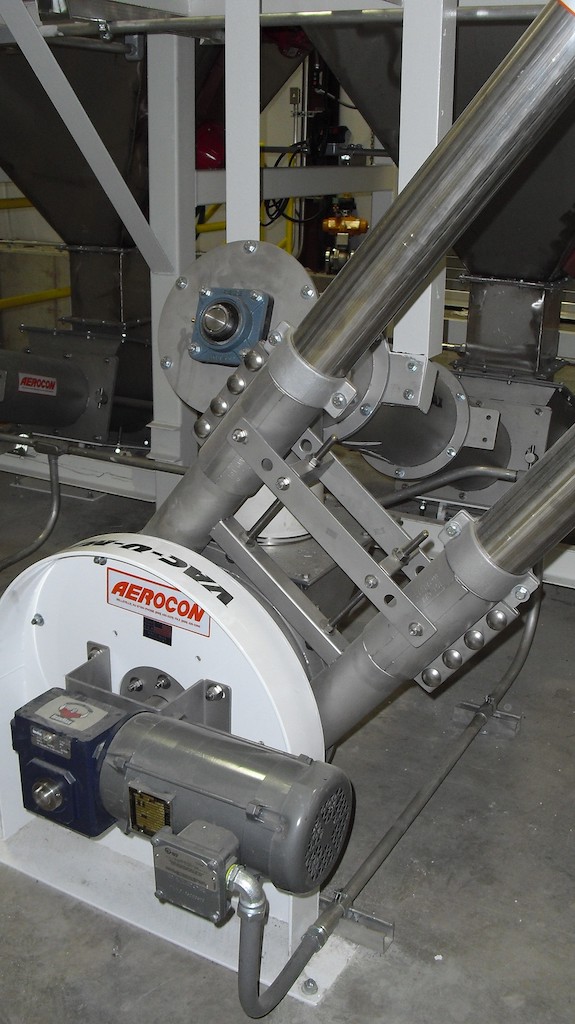
The advantage of a mechanical conveyor over pneumatic is the ability to move large amounts of material with minimal energy consumption. In mechanical systems, there is only a motor driving the system. On the other hand, a pneumatic system requires a motor and air to move the material. Due to the additional power components needed in a pneumatic conveying system, and the lack of a dust filtration system in mechanical conveyors, the dollar-to-dollar comparison makes the mechanical system less expensive to operate.
Control panels on mechanical conveyors are about as simple as it gets, requiring minimal integration. Unless a company is working with a level controller or load cell, the control panel is often just a fancy motor starter, which reduces initial costs further.
In a pneumatic conveying system, the control panel includes a programmable logic controller (PLC), or programmable relay, which dictates the sequence of events that are to occur, can handle complex information and provides customers the ability to download data for evaluation.
Benefits of aero mechanical and flexible screw conveyors
Aero mechanical conveyors are regularly used as an alternative to pneumatic conveying using two parallel tubes with a sprocket on each end, and a drive motor on one end. Inside the tube is a cable with discs on it, often called a cable assembly. As the cable assembly moves, it displaces air and material, thus fluidizing the material, carrying it in suspension along the conveyer to the outlet using centrifugal force.
Aero mechanical conveyors move material at approximately 20 ft3 per minute with a 3 HP motor, contingent on material bulk density. Depending on the design of the conveyor, the cost of a mechanical conveyor vs. a pneumatic conveyor for the same output can be one third the cost.
Flexible screw conveyors provide many of the same benefits, such as speed, as aero mechanical conveyors. Flexible screw conveyors, however, utilize only one tube and instead of a cable assembly, they contain a metal spiral that rotates. The spirals look like a stretched slinky or spring (that doesn’t compress), having the same diameter from end to end.
Flexible screw conveyors move less material than aero mechanical conveyors, but they operate continuously, unlike aero mechanical conveyors. A common use for aero mechanical systems is batch processing; and, a flexible screw is ideal for continuous, batch or intermittent processing. Both can convey 2000 lbs of material into a mixer in 10 minutes, but the flexible screw conveyor can continuously operate. Aero-mechanical conveyors require a metered infeed, and they must start-up and finish without material in the tubes. Flexible screws also can be started and stopped with a headload of material at the feed end.
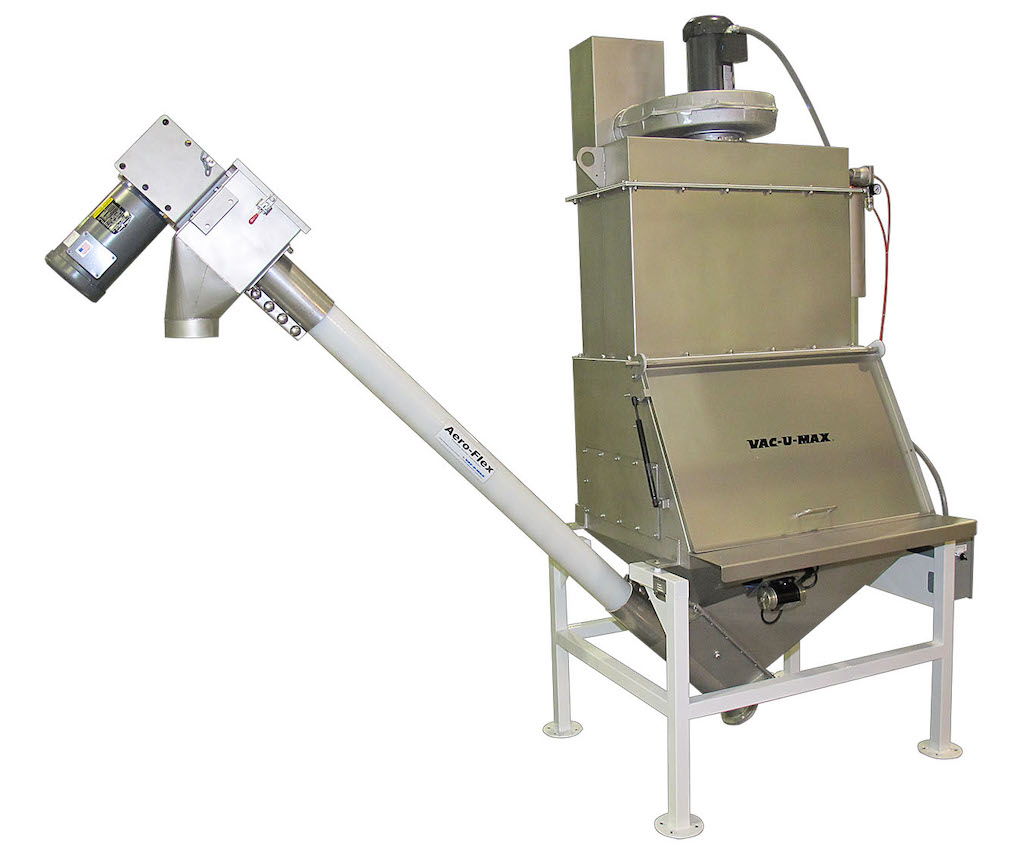
Conveying with flexible screws is common, which leads some to look at the equipment as a commodity item, which is not true. Heavy-duty flexible screws are more rugged than the standard and last longer, meaning less maintenance and downtime, and therefore lower replacement expenditures. Rugged flexible screws often come with two-year guarantees against twisting out, unraveling or breaking.
Where mechanical conveyors fall flat is the life of the equipment. Because mechanical conveyors contain more moving parts than pneumatic conveyors, maintenance costs are much higher, and machinery is more susceptible to unscheduled downtime. More moving parts also means more difficult to clean, making them less desirable in sanitary conditions. High-purity applications which cannot accept any foreign contamination, will not utilize flexible screw conveyors due to the plastic conveyor tube which can degrade over time. Aeromechanical conveyors can be equipped with food-grade components, but nevertheless have disc wear over extended periods of time.
Regardless of the potential downfalls, mechanical conveyors are sometimes the better and more cost-sensible option.
Benefits of pneumatic conveyors
In contrast to mechanical conveyors, pneumatic conveyors are more versatile and available in a wide range of configurations to integrate into production lines and meet facility specific requirements. Pneumatic conveying systems integrate into existing processes by routing conveying lines between floors, through partitions, around machinery, and are re-routed to accommodate process modifications.
Pneumatic conveying systems can be either negative or positive pressure systems. Negative pressure systems suck the material through the lines, while positive pressure systems blow, or push, material down the line. Factors other than material characteristics, such as conveying distance and the need for higher conveying rates, dictate the choice between negative and positive pressure systems.
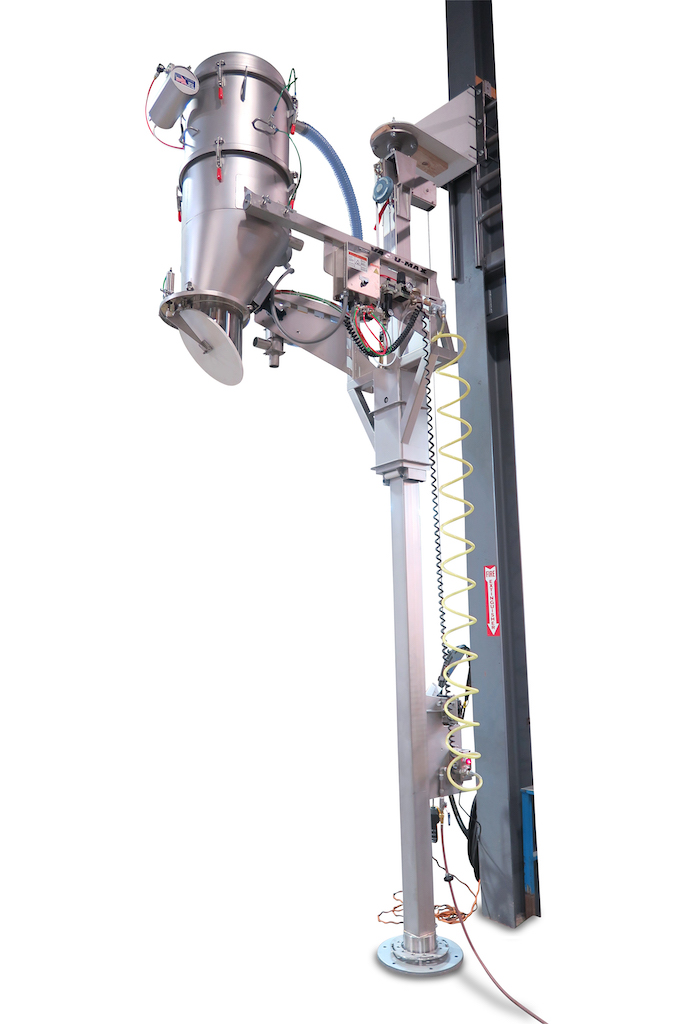
Dilute phase conveying injects more air into the conveying line and dense phase injects less air and more product into the conveying line.
Most pneumatic conveyor applications are negative pressure (vacuum) dilute phase systems, but dense phase systems are used as application dictate. There are some instances where semi-dense or semi-dilute systems are appropriate. Dilute phase systems employ higher velocity rates than dense phase systems.
A standard vacuum conveying system consists of five basic pieces of equipment that come together to work as one — a pick-up point, convey tubing, a vacuum receiver, a vacuum producer and a control module. From the pick-up point, material flows through convey tubes to the vacuum receiver which transfers material from above process or packaging machinery through discharge valves on the bottom of the receiver. Vacuum producers are the core of pneumatic conveying systems and work with the control panel to manage the flow of material through the convey tubes to the vacuum filter receivers.
Vacuum conveying systems can accommodate an assortment of vacuum producers (such as air-powered, electric, regen blowers and vacuum pumps), based on application, configurations, and utility requirements such as compressed-air, one-phase and three-phase.
Safety reasons for automating dry bulk powder transfer
One of the most common reasons to automate dry bulk powder transfer is to eliminate climbing to load materials. Most packaging and process machines need to be filled from the top, with a feed opening that could be as high as 10 feet above the ground. While that can be achieved with a vacuum conveyor, if it’s permanently installed above the packaging machine, all maintenance must be performed at that elevated location requiring the use of a ladder, scissor lift or mezzanine.
Even with the most sophisticated vacuum conveying systems, equipment located out of reach still poses hazards for operators who need to clean or service vacuum conveying equipment permanently installed above process machinery.
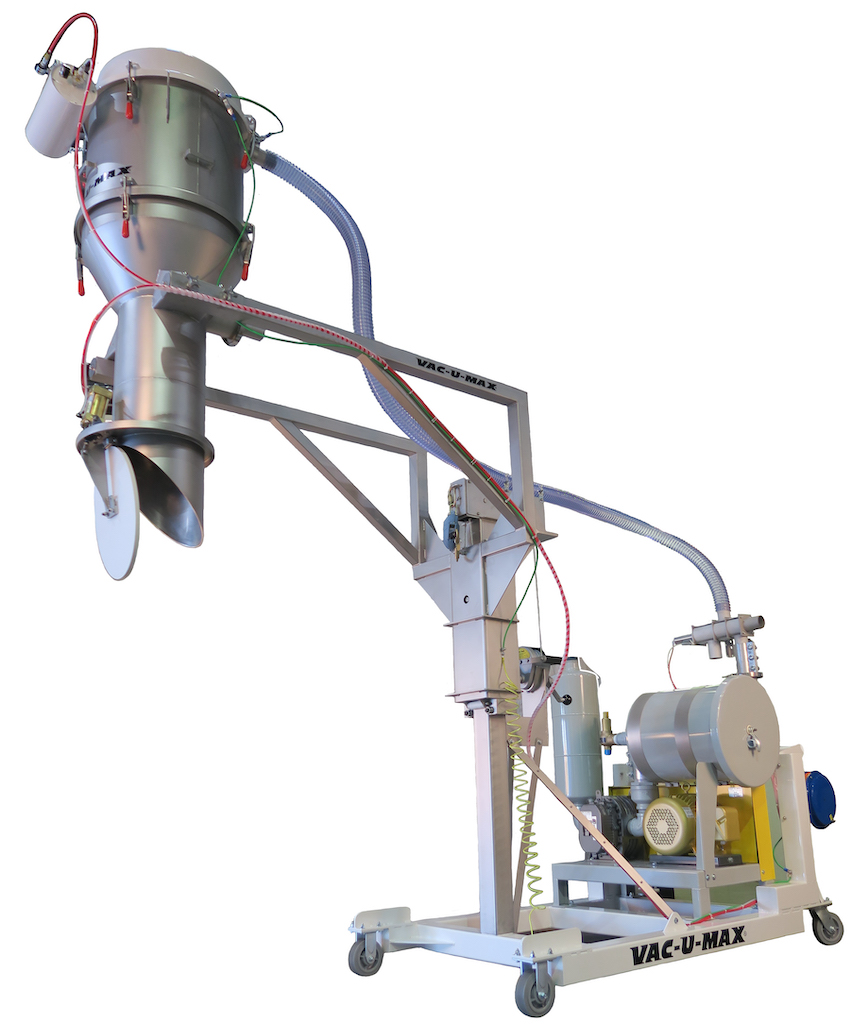
With mobile vacuum conveying units, rolling the conveyor away from other machinery and lowering the receiver allows simultaneous cleaning of both the conveyor and machine, instead of one after the other.
Mobile and column lift conveyors are complete conveying systems that raise and lower vacuum receivers in order to load mixers, reactors and other processing equipment and then bring the vacuum receivers back down to ground level for cleaning or sanitizing.
Mobile and column vacuum conveying systems, when constructed within Food Safety Modernization Act (FSMA) sanitation regulations, are ideal for food, nutraceutical and pharmaceutical applications.
Column conveyors utilize an electric lift mechanism with a remote pendant, controlled by an operator standing a safe distance away, to raise and lower vacuum receivers above mixers, blenders, reactors, and other process vessels with fill ports 15 ft or more above the floor.
These systems, with top and bottom anchors can load side-by-side process vessels from paper bags, drums, IBC’s, boxes, bulk bags, silos, storage containers and feed bins.
Mobile conveying systems operate in the same fashion as column lift conveyors, but are portable, movable with one operator, and able to service multiple process vessels at varying discharge heights. When not in use, operators can roll these vacuum conveying systems from the work area to save on floor space.
The ability for operators to bring equipment down to floor level for cleaning reduces downtime, labor costs and potential injury costs.
These types of units are compatible with OSHA’s Walking-Working Surfaces standard to protect against falls and slips; and back injuries from repetitively carrying bag and boxes up the stairs to load or clean equipment.
Another unique adaptation of vacuum conveying systems is direct charge blender loading, designed for the direct charge loading of blenders, mixers, reactors and any vessel capable of withstanding a vacuum.
With a facility’s blender or mixer as the primary receiver, the conveyor manufacturer configures systems specific to each application, providing the power source, filters, controls and adapters.
Direct charge blender loading reduces safety and ergonomic concerns from excessive ladder climbing for manual loading, increases blender throughput by reducing the loading time and it is a much cleaner operation than manually dumping ingredients into the blenders from a mezzanine.
With the right equipment, automating dry bulk material transfer delivers many benefits that translate to higher margins. Sometimes factors dictate which type of technology is used, but when given the choice, upfront costs should not be the only deciding factor between a mechanical or vacuum conveying system. Users also should seek advice from experts in bulk dry powder handling for an automated system to achieve cost savings.