Modern technology and creative thinking are enabling many impressive projects using human-machine interface software and supervisory control and data acquisition software. HMI and SCADA software help with OT and IT convergence. See six SCADA software advantages, applications.
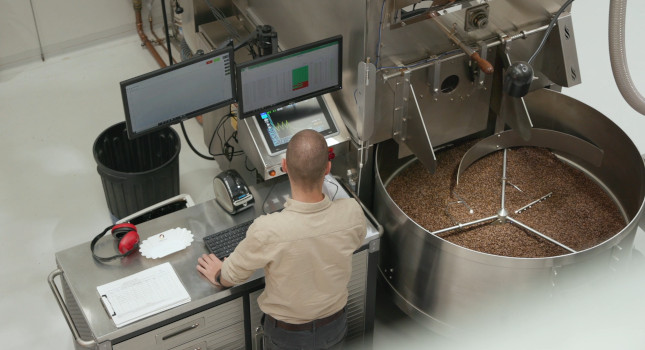
Learning Objectives
- Human-machine interfaces (HMIs) and supervisory control and data acquisition (SCADA) systems can provide real-time information to operations technology (OT) and information technology (IT) teams.
- On top of linking people together, they improve overall information access and can help manufacturers become more efficient.
There is no question human-machine interface (HMI) and supervisory control and data acquisition (SCADA) systems are crucial for industrial organizations. SCADA, in particular, allows industrial organizations to:
- Control industrial processes locally or at remote locations
- Monitor, gather, and process real-time data
- Directly interact with sensors, valves, pumps, motors and more through HMI software
- Record events into a log file.
SCADA systems have undergone substantial evolutionary changes over the years, allowing industrial organizations to do more. With the introduction of smart machines, Big Data, and the industrial internet, operations technology (OT) and information technology (IT) departments are finding they need to solve the same problems: accessing industrial data, integrating more systems and solving business challenges. Modern SCADA systems aim to solve these problems by leveraging the best of controls and IT technology.
Six SCADA software advantages
Companies are embracing modern industrial application platforms and technology, creating new and innovative industrial systems in all industries. SCADA is in the middle and offering capabilities including:
- Combining data and integrating with disparate systems
- Eliminating paper and clipboards
- Running advanced logic engines and calculations
- Getting data to more people
- Leveraging mobile devices
- Linking plants and people.
SCADA is excellent at communicating with programmable logic controllers (PLCs) and field devices. Traditional SCADA systems often have limitations on the brands of PLCs they can communicate with. It’s incredibly important to be able to pull data from multiple disparate PLCs into one platform for a “single pane of glass” for operators. Thanks to modern standards such as OPC UA, users can connect SCADA to these devices.
Along with PLCs, several other data sources and integrations are important to SCADA, such as computerized maintenance management systems (CMMS), enterprise resource planning (ERP), manufacturing execution systems (MES) and others. There’s enormous benefit in connecting these systems and adding more context to the operator’s screen.
SCADA connects customer and supplier
The team at ESM Australia helped YourCoffee connect its Shopify e-commerce platform to the factory floor. Using SCADA with RESTful web service APIs and a programmable automation controller (PAC)-based factory automation platform, ESM Australia delivered YourCoffee the Industry 4.0 tools to connect, evaluate, structure and control information and physical processes. This enabled the company to achieve their production goals.
YourCoffee’s customers order their desired custom-made blends as well as selecting the bag size, type and label type. Using web service calls, SCADA harnesses the JSON data returned from Shopify. Orders are then divided into product-based objects where the users can collate several products from separate orders and produce a production run optimized to reduce changeover times. The production system automatically calculates when, where, and how much coffee is needed to produce the blends and then creates a roasting and packing schedule. The combination of Shopify and SCADA has closed the gap between the customer and the supplier, increasing the quality, speed, and efficiency of the supply chain.
By combining functions and using modern technology, industrial organizations can eliminate paper and clipboards. Using SCADA that supports structured query language (SQL) databases, paperwork now can be digital. Microsoft Excel sheets or Access programs also can be converted to a central shared application.
SCADA for recipes, barcodes, historian, MES
JLG Industries, which develops aerial work platforms, wanted to standardize on one software platform in its manufacturing plant. This platform would unify existing applications and devices, eliminate paper forms, provide historical data storage and provide MES capabilities.
System integrator Multi-Dimensional Integration (MDI) helped JLG by developing a new system utilizing JLG’s ERP system, barcode technology and recipe management. The clients acquired weight samples from scales via Bluetooth and print barcode labels upon completion. The labels are then scanned at a downstream station and the data is used by the recipe-management system to automatically set up machine calculations and load in a recipe. All the data is saved in MSSQL server and generates reports at each manufacturing station. JLG eliminated paper statistical process control charts, paper production schedules in key areas, hand calculations and manual data entry.
More SCADA data, more power, remote control
Since SCADA systems have access to important OT data, organizations want to run more advanced calculations close to the PLC. For example, Streamline Innovations, which operates natural gas treating units in Texas that convert dangerous hydrogen sulfide (H2S) into fertilizer-grade sulfur, wanted to employ an automation platform written on a PLC. However, this did not enable complex calculations to provide model-based controls (and therefore semi-autonomous operation), nor remote control of the unit.
Streamline turned to SCADA to run several Python scripts that allow complex calculations — such as fast Fourier transforms on pump vibration and weather forecasts downloaded from the U.S. National Weather Service to determine optimal operating temperature – something that would seem impossible with a PLC. Auto-notifications of alerts are sent via Twilio to operators and operations engineers when issues arise. Accessing data is vital and the use of smartphones and tablets is increasing. In fact, mobile devices have overtaken desktops as the preferred way to get online and find information. This paradigm shift is happening in the industrial space, too.
SCADA enables virtual reality, visualization, controls
San Bernardino County in Southern California was looking for its next-generation visualization and control system for its landfills. Existing equipment was old and in need of upgrade — and did not have an easy-to-use HMI or data visualization. The mandate was clear: there is a need for a flexible architecture that allows visualization natively in HTML5 to leverage any modern brower-based device. Using a hub-and-spoke model with an edge gateway onsite and a cloud platform, Corso Systems and SCS Engineers offered a complete enterprise solution for the county. SCS uses aerial data to compose topographic mapping, 2D images, 3D renderings, GIS, thermal, near-infrared (NIR), and methane leak detection for various waste facilities.
After flying over the county’s San Timoteo Landfill, uploading the imagery, and mapping the facility, SCS and Corso were able to embed the 2D images and 3D renderings. This allowed users to access data using any modern device from anywhere. Additionally, the team was able to take those rendered images and apply them into a Microsoft HoloLens VR (virtual reality) headset, which allows decision-makers at San Bernardino County to “walk the site” from their offices. The pilot project’s success led to it being expanded to 27 other county sites.
Stronger connections all around
SCADA systems have the unique ability to connect not only data together, but also people. Using modern SCADA systems with unlimited licensing models, OT and IT departments can get access to needed data. As new challenges arise, new projects can be built to solve those problems. LafargeHolcim provides building materials and has more than 70,000 employees.
SCADA links servers, plant, management data
During a reorganization, the company wanted to manage the work of nearly 300 of its employees in six locations around the world. As the company was planning to have a central SCADA server to manage all its local SCADA servers, it decided to build an application that would link plant data with people and management data.
The main application has three primary workflows: 1) missions, which are requested by plant managers (assistance, technical studies); 2) activities (who is working on which subject); and 3) timesheets (showing what has been done and also what will happen in the future, with a real-time forecast). The application is used by almost 600 people, and is a great example of a non-direct, think-outside-the-box application.
These examples show how HMI/SCADA can accomplish much more than older software by leveraging modern technology and open standards. To get the most from SCADA software, identify challenges, build solutions to meet those challenges and achieve business value. Embracing new technology will allow operations to get more value from applications and allow more access across an organization.
Travis Cox is co-director of sales engineering at Inductive Automation. Edited by Chris Vavra, associate editor, Control Engineering, CFE Media and Technology, [email protected].
MORE ANSWERS
Keywords: HMI, SCADA, HMI/SCADA
CONSIDER THIS
What applications would benefit most from HMI or SCADA in your plant and why?