Representations also serve as interfaces to further information
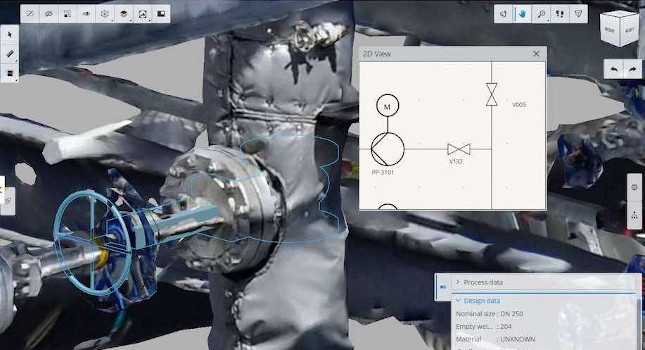
Digital twins are taking center stage — advancing beyond building information modeling to enable asset-centric organizations to converge their engineering, operational, and information technologies for immersive visualization and analytics visibility.
As is well known, a digital twin is a digital representation of a physical asset, process or system that includes the engineering information that allows us to understand and model its performance. Typically, a digital twin can be continuously updated from multiple sources, including sensors and continuous surveying, to represent its near real-time status, working condition or position. A digital twin enables users to visualize the asset, check status, perform analysis and generate insights to predict and optimize asset performance.
In the energy sector, digital twins are used to optimize the operation and maintenance of physical assets, systems and production processes. Many organizations using digital twins on projects are proving their value. An excellent example is Shell Chemical’s use of a digital twin on a very large construction project in Pennsylvania. Shell is surveying its plant with drones on a twice weekly basis as the plant is being constructed.
The reality model is combined with other asset data to update the project’s digital twin. The digital twin is used to track construction and identify issues by visualizing change over time. This capability enables the team to immediately respond to onsite changes. Shell is also capturing the asset’s digital record as it is being constructed for use in operations and plant maintenance, such as the precise location of underground utilities. The digital twin enables the organization to make better sense of its data, both now and in the future.
Embracing digital twins
The energy sector is well placed to take advantage of digital technologies. Whether it is simply adding a vibration sensor to a piece of rotating machinery or creating a full digital twin of an entire plant, digital twin technologies can reduce costs and streamline maintenance and operations processes.
Digital twins are a hot topic, and many organizations are keen to work out how they can best benefit from their use. Most companies are looking for advice on where to get started. Our advice is to start with the good asset data that you already have, get it in a position to be shared, and grow from there. Quite often, the good data is buried in systems that are inaccessible to the people who need it. One of the biggest benefits of digital twin technology is that it makes trusted, up-to-date information more widely available.
Bentley provides an open, connected data environment, which is a set of cloud-provisioned or on-premises services that support digital context, digital components and digital workflows. By enabling an open, connected data environment, energy firms can better manage and access consistent, trusted and accurate information. Owner-operators and project delivery firms also can share the benefits of an open, integrated and connected framework.
The energy sector has always embraced innovation, and there are several examples where digital technologies are already delivering significant business advantages. For example, Oman Gas developed a reliability and integrity program based on a digitalized, automated framework provided by Bentley’s AssetWise Reliability solution. The applications are reducing human intervention and improving resource effectiveness. Another example is Vedanta Ltd. — Cairn Oil & Gas in India. This organization is using asset performance software to optimize production across its over 800 offshore wells. The company implemented smart well integrity and a flow assurance management system to manage integrity risks and manage its stocks. Bentley’s AssetWise provides a connected data environment that interacts with the company’s existing systems and integrates data from many sources.
In Russia, Volgogradnefteproekt is playing a pivotal role in going digital with Lukoil for the development of the Filanovsky field in the Caspian Sea. Volgogradnefteproekt has overall project management responsibility for all Lukoil projects in the Caspian Sea and has introduced an integrated BIM approach consolidating input from the various contractors. The organization implemented this approach to deliver and maintain a consistent 3D model using Bentley’s connected data environment. Used across design, engineering and construction, the connected data environment has already delivered benefits, including reducing overall design time by 70% and construction costs by 20%. The organization also uses the 3D digital engineering model from design through construction and commissioning to operations and maintenance, which is expected to reduce annual operations costs for the field by 30%.
Saving time, organizing information
Digital twins, and other digital technologies, can help the energy sector save significant costs over time. A sound approach leverages the investments that companies have made in technologies, offering seamless upgrades to new platforms and using existing systems, sensors, and other data sources as much as possible. In many cases, using reality modeling to capture as-is conditions is less expensive than traditional survey techniques.
The next step for many organizations is to gather the data accumulated from sensors into a single view, leveraging reality modeling for users to easily make timely decisions based on current data. Digital twins can help users organize their information. Having a single view of the truth allows for quick maintenance and operation decisions while also assuring that decisions are based on the most accurate data available.
Digital twins help users decide the viability a business option, as well as follow up on that decision. Another benefit that digital twins provides is streamlined updating processes. Using traditional updating processes, it can take as much as six months to record a change made in the field by maintenance. If someone looks at the records during this six-month gap, the records are outdated, leading to accidents and major compliance issues. The work processes associated with digital twins can ensure that all information is immediately updated, and data is always in compliance.
Digital twins’ interoperability with other applications is another major benefit. Digital twins are opening new opportunities for all types of new services. Because of the rapid growth in the adoption of reality modeling, new companies are replacing traditional inspection and surveying organizations, providing digital models of assets rather than reports. An example of a new service offering is the recent announcement by Siemens Power and Bentley Systems to provide asset performance management services for power plants. This new cloud-based service empowers power plant owners to take full advantage of digitalization, which helps improve maintenance operations and planning.
Open environment, improving safety
Cloud technology is crucial for digital twins, helping enable collaboration, improve decision making, and deliver better project outcomes and better-performing assets. To have open and live access to information within digital engineering models, organizations need to implement a connected data environment. This type of environment allows engineering technologies (ET) to be brought together with information technologies (IT) and operational technologies (OT) to improve the throughput, safety, and reliability of their production assets.
Microsoft’s Azure cloud platform can be used to ensure the safety and security of information. Microsoft Azure has many layers of security and is regarded by many people in the industry as the safest platforms from malicious attack. In fact, many energy organizations have found that keeping their data in the cloud is safer than keeping data in their own data centers.
In addition, leveraging applications that also work in a connected data environment — such as project collaboration solutions and asset performance management solutions — ensures both user and component level access to data and information. Both type solutions ensure that the right people are viewing the right information at the right time, making their digital twins a safe place to store their data.
Accelerating your digitalization
Digital twins have the potential to offer huge benefits to the energy sector. The challenges, however, are where to start, what are the next steps, and how you can accelerate your digitalization. Most companies in the energy sector have good document management systems supporting their regulatory processes, as well as often having good enterprise asset management systems supporting maintenance. Much of this data, however, is inaccessible to those people who need it and often not as timely as it should be.
Opening this information using a federated approach — including use of mobile platforms — will bring initial benefits, including better ways of finding information. If you have existing plants, use reality modeling as a starter to allow digital twins to capture as-is conditions. Link those models to sensor information to enable operations and maintenance to have a better understanding of context.
Finally, adding simple workflows to the digital twins to record changes in the field will keep information evergreen and up to date, providing a sound basis for next steps. These steps might be leveraging artificial intelligence and machine learning to improve maintenance and operations processes, enabling digital twins to truly drive your business.