Combined heat and power (CHP) systems play a key role throughout the United States as a key source of power for facilities and several examples of how they improve a facility’s overall performance are highlighted.
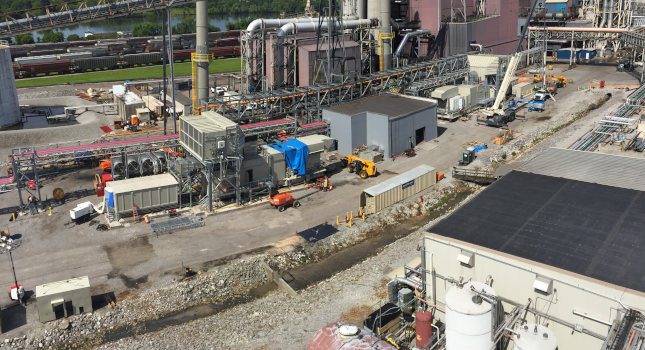
Combined heat and power (CHP) systems play a key role throughout the United States as a key source of power for facilities. These systems generate electricity and usable thermal energy from onsite generator sets. Typically, CHP systems are used at facilities with high heat load requirements. Most CHP installations run on natural gas and power part or all of a facility’s operations. Facilities with CHP systems save money over buying power from the grid and gas for heating.
CHP is used in many unexpected places and is providing flexibility and power generation to industries that might not be considered for CHP at first glance.
Taking flight at Johnson Space Center
NASA’s Lyndon B. Johnson Space Center (JSC) has served as a hub of human spaceflight activity for more than sixty years. The combined heat and power plant (CHP) supports mission control to the International Space Station and training center for the world’s leading space explorers – with adaptability and flexible scale, while meeting JSC’s electric and steam requirements, and half the chilled water requirements. JSC is home to the nation’s astronaut corps, the International Space Station mission operations, the Orion Program and a host of future space developments.
Funding for The Johnson Space Center (JSC) CHP plant was provided through the DOE’s Energy Savings Performance Contracting (ESPC) partnership with Energy Systems Group. In this $47 million project, utility savings are used to cover the project and maintenance costs over a 22-year period. Since operations and maintenance (O&M) for new equipment is included, there will be no increase to the current facilities contract. The ESPC also provides that all ESCO installed equipment have at least 10 years of remaining operational life at the end of the contract term of 22 years.
JSC’s CHP plant, operating in parallel with the utility, powers 70% of the site base electric load. The waste heat from generators is converted into steam. This provides 100% site steam load, and between 40 and 60% peak chilled water load. This is possible because of the existing steam turbine chillers in the JSC plant. Further, in the event of utility power disruptions, the CHP plant provides the potential for island microgrid operation of critical mission operations. The CHP plant produces nearly 12 MW of electricity via two 5.7 MW combustion turbines and one 500 kW steam turbine.
Utilizing waste heat from the combustion turbines, the two heat recovery steam generators produce ~50,000 lbs./hour of high-pressure steam. This steam is used for heating as well as generating chilled water through existing steam turbine-driven chillers.
Whereas traditional utility power provides on average 36% efficient electric, ESG claims that NASA JSC’s CHP plant allows for approximately 85% efficient operations. This CHP system allows JSC to meet federally mandated energy reduction metrics.
Start early planning of any CHP project and get the local gas utility involved. to avoid potential timing issues with energy supply, & connection to local gas distribution system.
Consider hiring specialty consultants that can perform a Life Cycle Cost analysis that looks at capital costs, energy costs, and maintenance costs all over the life of the expected system.
Plan for procurement and installation time frames, which includes permitting.
Bringing CHP to a food ingredient processing plant
Tate & Lyle has been a long-time user of CHP at many of its industrial locations. Two of its corn wet mills in Loudon, Tenn. And Lafayette South, Ind., have been awarded the U.S. Environmental Protection Agency’s (EPA’s) Energy Star certification, having met strict energy efficiency performance levels set by the EPA. It is the only corn refining plants in the U.S. to earn this accolade. Energy Star was introduced by EPA in 1992 as a voluntary, market-based partnership to reduce greenhouse gas (GHG) emissions through energy efficiency.
“This reflects the dedication and hard work of our operations team, especially our technicians who are committed to running these mills as efficiently as possible,” said Nick Waibel, global energy lead at Tate & Lyle.
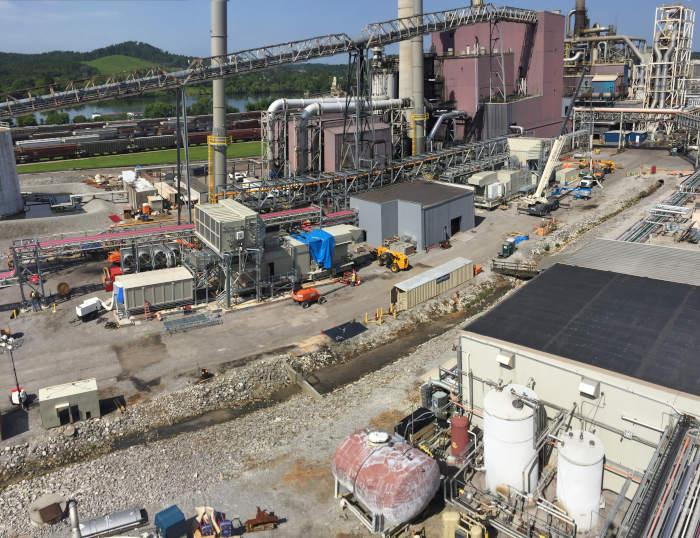
Demanding corn milling processes
Tate and Lyle, a global provider of food and beverage ingredients, processes around 2% of the U.S. annual corn crop in several plants. The company takes shelled corn (maize), separates the kernels into their core components (starch, oil, protein and fiber) and processes them to create a range of products such as specialty sweeteners and bulk ingredients, which are distributed globally.
Tate & Lyle has been a long-time user of CHP at many of its industrial locations. Two of its corn wet mills in Loudon, Tenn. And Lafayette South, Ind., have been awarded the U.S. Environmental Protection Agency’s (EPA’s) Energy Star certification, having met strict energy efficiency performance levels set by the EPA. It is the only corn refining plants in the U.S. to earn this accolade. Energy Star was introduced by EPA in 1992 as a voluntary, market-based partnership to reduce greenhouse gas (GHG) emissions through energy efficiency.
Tate & Lyle, encouraged by the return on investment (ROI) they received switching to natural gas-based CHP at a facility in Loudon, TN, completed a similar upgrade at their Lafayette South food ingredient processing plant in Indiana. It chose to replace its aging coal boiler with a similar configuration as Loudon: two Siemens Energy SGT-700s and two Rentech Heat Recovery Steam Generators (HRSG).
“Natural gas fired cogeneration brings clearer energy online and helps us move away from the use of coal boilers,” said Nick Waibel, global energy lead at Tate & Lyle. “We have set a goal of eliminating coal from all our sites by 2025. Our Decatur, Ill., facility, is also in the midst of replacing coal boilers with natural gas.”
The energy units are designed for high output/efficiency and lower emissions with a wide fuel range capability. Due to high process heat needs these sites are s well suited to CHP. The system also includes a third-generation dual fuel dry low emissions (DLE) combustion system which keeps NOx emission levels low.
“In these dynamic times, we had to ensure our investment will serve us in the near term and the long term. It’s good to know our turbines can make the transition to hydrogen when that supply comes online in the future.”
The results of this plant upgrade were positive: Improved grid resiliency, greater process efficiency, carbon emissions slashed by more than 30% and a GHG emissions drop of around 40%. By replacing aging coal boilers, generating electricity on-site and recovering heat, overall energy efficiency has been boosted while substantially reducing energy costs and cutting water usage by 5%. The plant manager also reports greater process efficiency and power resiliency.
“We take our responsibility to the environment seriously and are committed to doing more to care for the planet, including lowering our greenhouse gas emissions by using cleaner energy,” said Travis Montoya, Lafayette South plant manager for Tate & Lyle.
Far from being projects executed at specific plants, this represents a company-wide target by the company for 2030 to deliver: a 30% reduction in CO2 emissions, all its waste to be beneficially used, a 15% drop in water use and the elimination of coal from its operations. Getting rid of the coal boilers at Loudon and Lafayette is a major step in achieving the latter goal.
“The Lafayette South plant project not only helps meet our sustainability goals in reducing greenhouse gas emissions and water use, it’s also a project that saves us money as a company, so it was really a win-win for us,” Waibel said. “Eliminating coal and going into a clean-burning fuel is the right next step for our plant.”
CHP benefits everywhere
Regardless of the facility’s size or needs, CHP has many potential benefits for manufacturers. Their ability to provide flexibility and power generation to facilities will make them better suited for the future as companies look to leave a small energy footprint.
Johnson Space Center
Tate & Lyle
– This article appeared in the Gas Technology supplement.