There are several different types of bulk solids material handling equipment available; learn tips and tricks here
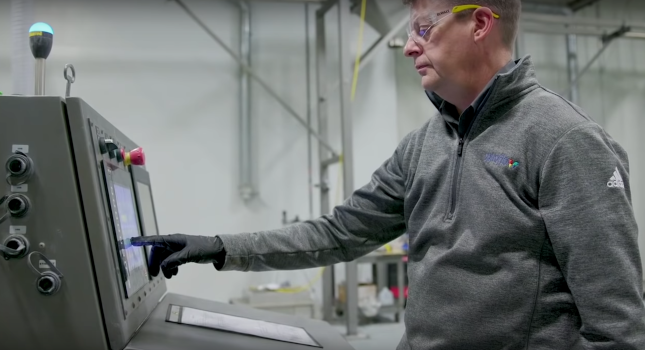
Learning Objectives
- Understand different types of bulk solids material handling equipment and their uses.
- Learn to develop safe material handling practices.
- Gain insights about commonly asked questions.
Material handling insights
- Material handling of bulk solids can be done effectively and safely if the correct products and systems are selected.
- Understanding the uses of material handling equipment allows a manufacturing plant to make educated selections.
Bulk solids material handling equipment plays a crucial role in industries that process dry and bulk solids in either powder or granular forms, including pharmaceuticals, chemicals, food and beverage. Bulk material handling solutions providers offer a wide range of equipment for conveying, loading and unloading material.
Understand the different types of material handling equipment and their uses
Efficient material handling is a critical aspect of any industrial process, and selecting the right equipment can help maximize productivity while minimizing downtime and accidents. Choosing the right equipment can be confusing with so many different types of material handling equipment available on the market.
Throughout the processing line, some key pieces of material transfer equipment will include conveyors, bulk bag fillers and bulk bag unloaders.
Conveyors are an essential part of most bulk solid processes, and there are various conveyor technologies on the market. Automating the movement of materials from one part of a process to another can have a huge impact on the speed and efficiency of an operation. Through careful conveyor selection, companies can improve process safety and productivity, make significant savings on labor and energy costs and minimize product degradation or contamination.

Some of the more common types of conveyors available include aero mechanical, belt conveyors, bucket, cable drag, flexible screw and pneumatic. Each of these conveyors has unique features and benefits that suit different applications.
For instance, flexible screw conveyors are a great and economical choice for a wide range of materials. Cable drag conveyors are ideal for handling materials that need to be moved long distances and handled gently to avoid breakage. Pneumatic conveying systems can quickly move products over long distances and complex routes, however, they often require expensive and heavily regulated air power units, fans and filters. Aero mechanical conveyors are a unique hybrid technology that allows for near-total material transfer without the additional complexity of pneumatic systems.
Totally enclosed conveying options such as cable drags and aero mechanical conveyors also have advantages over the open belt and bucket style conveyors when it comes to hygienic conveying and minimizing the risk of product contamination.
Selecting the right conveyor system is critical to optimizing material handling processes. Each conveyor type has unique features and benefits that suit different applications and choosing the right one can help increase efficiency, productivity and safety.
Due to the convenience, versatility and relatively low cost of flexible intermediate bulk containers, sometimes known as bulk bags, the industry has experienced significant growth in the use of this medium for handling bulk solids across a wide range of industries. To reap the benefits of this technology, end users need to understand and select the most appropriate features to incorporate into their bulk bag handling equipment.
Bulk bag unloaders are designed to discharge large quantities of materials while minimizing the risk of accidents, spills and material waste. They come in different sizes, shapes and configurations to suit specific applications and can be customized to meet different requirements.
An increasingly popular style of bulk bag unloader incorporates a dedicated hoist, which allows for quick, easy and accurate bag positioning over the unloading station. This eliminates the need for a forklift truck to load the bags reducing the amount of manual labor required and minimizing the risk of employee injuries.
Bulk bag unloaders should also be designed to discharge material safely and efficiently, minimizing the risk of dust escaping to the environment and operator exposure. To achieve this, the unloading station can be customized with a variety of bag and spout seals that may include a spout untie chamber with an integrated dust collection system. Bulk bag unloaders may also include mobile options to move to various locations in a plant, low headroom designs for areas with limited space and integral bag dump stations to unload small bags in your process.
Bulk bag unloaders can be integrated with downstream equipment such as hoppers, conveyors or other material handling systems. They can incorporate weighing systems automated and controlled by a programmable logic controller for accurate dosing or batching operations. All of these features can help to streamline the material handling process, reduce material waste and improve overall efficiency.
Using bag fillers in material handling
Bulk bag fillers are another essential piece of equipment in many industries where there is a requirement to package large quantities of powders, granules or pellets. These systems should be designed to fill bulk bags efficiently and accurately while producing a safe and stable package that can be handled and stored easily and safely.
The filler also can weigh the materials as they are being filled, ensuring that each bag contains the desired amount of material. Semi-automatic bulk bag filling systems can help improve efficiency by automating the filling process, minimizing the amount of manual labor required and reducing the risk of material spills or waste.
An advantage of using a semi-automatic bulk bag filler is that it reduces the need for manual labor and minimizes the risk of errors or injuries associated with manual handling. Instead, the system can automatically fill bags with the desired amount of material, reducing the risk of spills, waste and contamination.
With automated filling and weighing capabilities, the system can accurately fill bags at a rate of up to 40 or more bags per hour and significantly increase weighing accuracy resulting in less product being “given away” in overfilled bags. Some manufacturers also offer sophisticated densification systems that can be incorporated and automated during the filling cycle. A well-designed densifying bulk bag filling system can result in significant cost savings by increasing production rates, reducing shipping and packaging costs, minimizing product waste (giveaway) and safer storage and stacking of bags.
By working with a company that has a comprehensive understanding of the different types of fillers, unloaders and conveyors available and how to apply them correctly, manufacturing facilities can make informed decisions that help improve their bottom line.
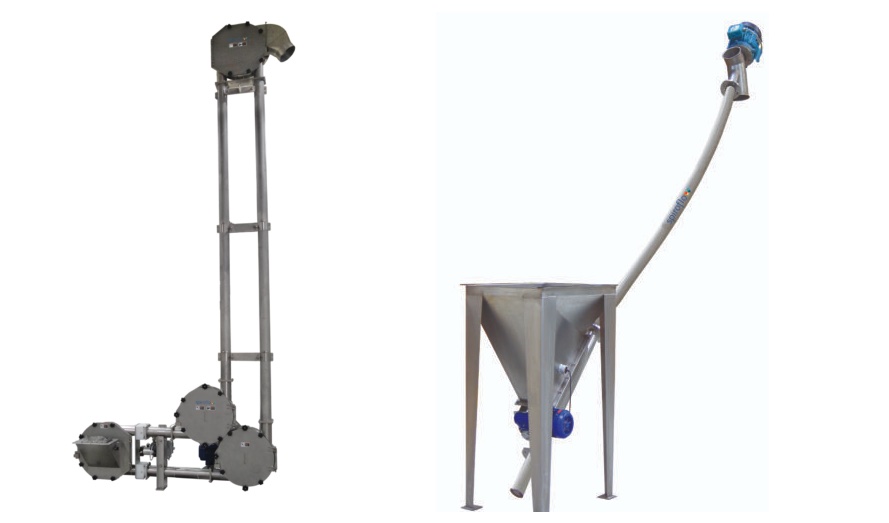
Developing safe material handling practices
Material transfer points that require an operator, such as manual bulk bag unloading or semi-automatic bag filling, can introduce the risk of injury or accidents if proper safety protocols are not followed. Training employees to operate material handling equipment correctly is crucial in ensuring safety. This includes training on potential hazards associated with the equipment and proper procedures to follow in an emergency.
The next step is to identify potential hazards before any material handling activity occurs. This can involve conducting a risk assessment to identify potential risks and taking measures to mitigate them. This is especially critical when handling powders which can be hazardous to personnel or even become explosive in certain conditions. Employees should be given appropriate personal protective equipment — such as gloves, goggles and respirators — as required. Equipment should also be regularly inspected, cleaned and maintained to ensure it is in good, safe condition.
Creating a culture of safety within the workplace is also critical. This can be done by conducting regular training sessions, establishing safety committees and encouraging employees to report any potential hazards or safety concerns. Adhering to industry regulations and standards, such as those set by Occupational Safety and Health Administration, is crucial to ensure all safety protocols are met.
Prioritizing safety in material handling practices not only protects employees from potential harm but also ensures the smooth and efficient operation of the workplace. It helps prevent accidents and breakdowns, leading to costly downtime and lost productivity. A safe workplace also promotes employee morale and job satisfaction, leading to improved performance and better results for the company.
How is the right material handling equipment selected?
Selecting the right material handling equipment is crucial for any industrial setting. Various factors must be considered, including material properties, production rate and desired throughput. Consulting with an expert in manufacturing material handling solutions can help identify the appropriate equipment for a specific application. It’s also essential to consider the equipment’s capacity, durability and ease of operation and maintenance when selecting the right solution.
Is it worth exploring different conveyer options?
Taking the time to find the right conveyor for operations can be a very worthwhile investment. Not only can it be customized, but by finding the most suitable conveyor, it can improve safety, reduce labor costs and increase efficiency. Key points to consider when auditing conveying options include:
- Conveying distance.
- Energy requirements.
- Material challenges (hydroscopic, abrasive, friable, like to segregate).
Can complex bulk bag fillers really save money?
Yes, bulk bag fillers with high fill rates, accurate weighing systems and optimal densification systems can fill bulk bags faster, more accurately and efficiently. Below are a few of the cost savings that can result from a well-designed bulk bag-filling system:
- Reduced bag costs. Savings can come from either filling more material in each bag, reducing total bag usage or from the ability to use shorter, lower-cost bags.
Reduced material waste/giveaway. Less “free” product is given away by avoiding overfilling bags to ensure they are not underweight. - Savings in storage costs and floor space due to needing fewer bags to hold the same amount of material, oftentimes with the additional benefit of being able to safely stack bags due to their more consistent, square, stable shape with firmer, flatter tops.
- Reduced shipping costs. Using an efficient densification bulk bag filler, more weight can be shipped in the same footprint on each truck, often significantly reducing shipping costs.
What type of bulk bag discharger should be used for a specific material?
It depends on the material’s properties, such as its flow characteristics, moisture content and particle size. In narrowing down the decision, it’s important to factor in headroom, space constraints, how the bags will be handled, downstream process requirements and dust containment. A reputable manufacturer will test the equipment for safety and efficiency.

How is material handling equipment maintained?
While the life span varies depending on several factors, including the equipment type and frequency of usage, proper maintenance can significantly extend its life. For instance, selecting a conveyor built to handle expected wear and tear for more abrasive materials can prolong its life span. Regular cleaning and upkeep can also prevent equipment failure and keep it operating at peak efficiency.
Clean-in-place systems are becoming increasingly popular as they allow for quick and efficient cleaning without disassembling the equipment. For instance, a food manufacturer can switch between different flavors without worrying about flavor contamination. Proper maintenance and cleaning can ensure that material handling equipment lasts longer and operates efficiently.
What is the expected life span of material handling equipment?
The expected life span of material handling equipment depends on various factors, including the type of equipment, usage frequency and maintenance. Proper maintenance can significantly extend the equipment’s life span. For more abrasive materials, selecting a conveyor built to handle the expected wear and tear is crucial to ensure the equipment lasts as long as possible. It’s important to choose equipment specifically designed to handle the type of material being transported, as using the wrong equipment can cause premature wear and tear, leading to costly repairs or replacements.
Regular maintenance, such as cleaning and inspection, can also help extend the equipment’s life span. Some providers may offer maintenance and repair services as part of their product offerings, so it’s important to consider these factors when choosing a material handling equipment provider.
What to look for in a provider
When selecting a material handling equipment provider, it’s important to consider various factors beyond the equipment itself. Look for manufacturers offering material testing services to help customers find the best solution for their applications. It’s helpful to work with a manufacturer that offers a wide range of equipment and custom design solutions for any unique challenges, ensuring that operations are optimized for safety and efficiency.