Be cognizant about hazards, preventive measures and the dire consequences of an arc flash event.
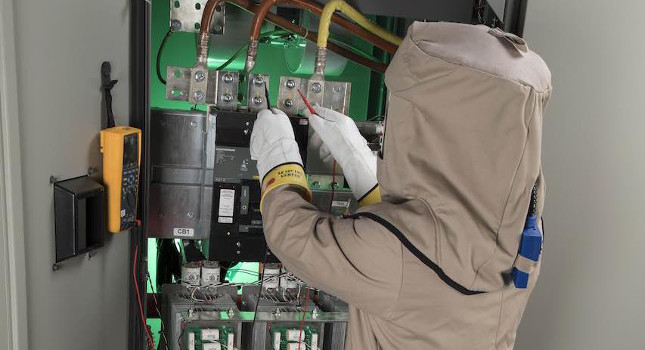
Electrical hazards, specifically arc flash and arc blast, can potentially result in serious injury or even death of electrical workers. Exposure and risk to arc flash hazards have increased in recent years due to higher voltages and available fault currents in electrical systems.
During an arc flash, an individual may be exposed to temperatures as high as 30,000 F, which is four times hotter that the surface of the sun. Air expands dramatically when heated to these temperatures, and arcing can instantly vaporize metals like copper or steel. The rapid expansion of air and metal vapors creates shock waves similar to those produced in an explosion and can pulverize concrete walls. Too often, employees who are not wearing personal protective equipment (PPE) are seriously injured or killed if an electrical arc occurs when they are working on electrical equipment.
On average, there are five to 10 arc flash incidents per day in the U.S. resulting in more than 30,000 injuries and 400 deaths annually, with approximately 80% of the fatalities due to burns, not shocks. Arc flash does not only occur in high voltage environments, but actually is more common within 480V power systems.
Protection through electrical safety training
NFPA 70E: Standard for electrical safety in the workplace states that “Hazard elimination shall be the first priority in the implementation of safety-related work practices.” The proper use of safety equipment, knowledge of electrical hazards and proper response in the event of an electrical disaster are essential for all electrical personnel or those working on or around electrical equipment. An electrical safety program should be designed to provide personnel involved with the operation and maintenance of a power distribution system the knowledge, skills and abilities to meet the NFPA 70E training requirements to be considered a “qualified” electrical worker by NFPA standards. The electrical safety program is a requirement imposed by the NFPA 70E standard and must be implemented as part of your overall occupational health and safety management system. An optimal training program should always be tailored to your specific needs and may include, but not be limited to, the following:
-
Procedures to be used before employees exposed to electrical hazards start working
-
Risk assessment procedures that need to address the potential for human error and its negative consequences
-
Proper major electrical component operation and maintenance using manufacturer’s instructions
-
Applicable testing and maintenance recommendations from ANSI/NETA, MTS or NFPA 70B: Recommended practices for electrical equipment maintenance
-
Site and equipment-specific safety hazards and mitigation techniques
-
Lectures, presentations and hands-on demonstrations to provide maximum possible exposure to power distribution system safety, operations and maintenance requirements
-
Emergency response and safe release methods
-
A method for investigating electrical incidents (NFPA 70E requirement for incident investigations).
More than a label
When you partner with an electrical reliability services provider for your arc flash needs, make sure a complete solution is offered, instead of slapping a label on a piece of equipment. A great arc flash solution must include at least the following tasks and activities:
-
Risk assessment and hazard identification
-
Site review/compliance assessment
-
Protective scheme design review
-
Short circuit and coordination studies
-
Single-line diagrams
-
Arc flash analysis
-
Hazard labeling plan
-
Electrical safety program review/development
-
Training and performance evaluation
-
PPE plan
-
Preventive maintenance
-
Documentation
-
Annual recertification.
Are you compliant today?
If you answer “No” to any of the following questions, chances are that you may not be compliant.
-
Is your arc flash hazard plan documented?
-
Does your documentation include the results of the previous arc flash risk assessment and arc flash training?
-
Have the single-line diagrams been updated following any changes in your electrical infrastructure?
-
Do you have current signs and labels on equipment and at hazardous areas?
-
Do all labels include the type, name/ID, incident energy at working distances, flash protection boundary, arc flash PPE category, shock protection information, date of analysis and the certifying person per OSHA 29 CFR 1910.132 (d)(2)?
Arc flash study frequency
An arc flash study is not a “once and done” type of study. The NFPA requires the arc flash analysis to be updated every time major changes occur in the electrical system or at intervals not to exceed five years.
In addition, there are mandatory audit procedures imposed by NFPA 70E:
-
Electrical safety program: at least once every three years
-
Field work: time intervals not to exceed one year
-
Lockout/tagout (LOTO) program and procedure: time intervals not to exceed one year.
Lack of compliance may possibly expose workers to unknown hazards and result in severe financial penalties.
Preventive maintenance
NFPA 70E requires maintenance to be performed on electrical equipment in accordance with manufacturers’ instructions or industry consensus standards. Your partner of choice for electrical reliability services should assist you in developing a preventive maintenance program to specifically address arc flash hazards. An optimal program needs to evaluate equipment’s condition and determine the most cost-effective and manageable solution to ensure your protective devices operate properly, safely and reliably. Proper maintenance will ensure that you are in compliance with the NFPA 70E requirements permitting normal operation of equipment reducing hazards, thus often allowing tasks to be accomplished safely and without the need of extensive PPE.
Optimal PPE plans need to fully protect employees while addressing all relevant OSHA standards, to ensure compliance. Ideally, before work is performed on or around electrical equipment, it must be deenergized, if possible. Otherwise, recommendations for the minimum protective equipment workers must wear when they are near exposed energized equipment should be based on the findings of the arc flash risk assessment and calculated incident energy (IE) values. The plan also should cover how PPE should be worn, maintained and disposed of at the end of the equipment’s life.
Looking ahead
Arc flash hazards are very serious, and it takes more than a label to ensure the safety and well-being of your employees, while making sure that your critical assets are also protected.
Consider the financial aspect of these types of recurrent and mandatory studies. Prioritize budgets wisely to ensure funding is available for current study needs as well as future updates and ongoing training requirements.