Designing an efficient, long-lasting piping system
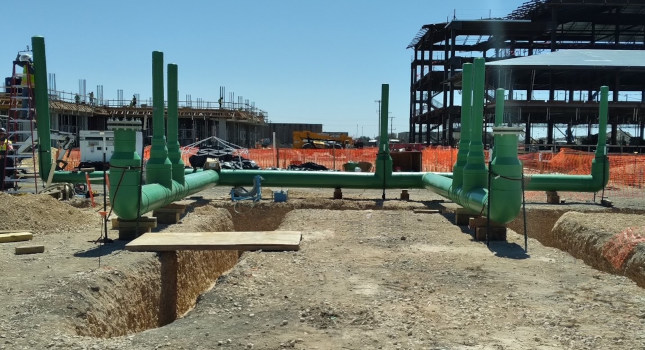
Building the United States Air Force’s new basic training facility at Joint Base San Antonio-Lackland, Texas required large diameter pipe and fittings to move 155ºF (68ºC) water effectively throughout the campus at 90 psi. The problem was that the 6,000 feet of pipe would need to be installed in crawl spaces, trenches and in riser locations. More than 250 fittings would be needed. The goal was to have a system that would provide long-term performance and need as little maintenance as possible.
“The build of the campus is essential to advance the Air Force’s training capabilities,” said Col. Dave Norton, director of AFCEC Facility Engineering Directorate. “The new infrastructure is designed to allow the Air Force to successfully train future enlisted personnel in a more functional, modern campus environment.”
The base dates back to just before World War I when it was established to provide aviation training for the country’s new Air Service and later becoming Lackland Air Force Base. It is now the only site for Air Force enlisted Basic Military Training (BMT).
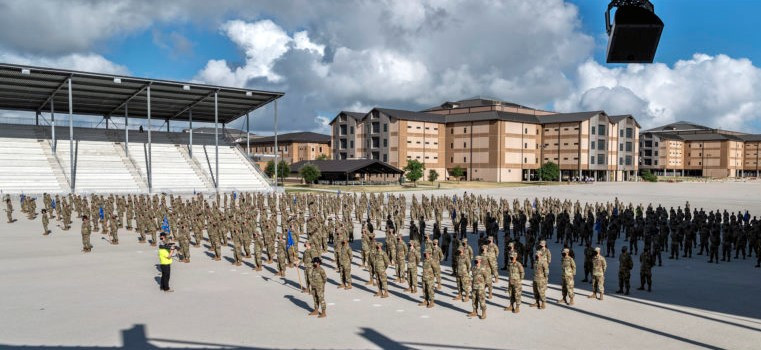
Traditional pipe materials
Traditional pipe materials such as copper and carbon steel were considered, but a type of thermoplastic pipe was selected for the system that would move hot and cold potable water, non-potable HVAC heating and chilled water, plus condenser water. Solving the problem would win the pipe’s manufacturer, Asahi/America, Inc. (Lawrence, MA) the Project of the Year Award from the Building & Construction Division (BCD) of the Plastics Pipe Institute, Inc. (PPI).
The association’s annual awards program recognizes projects and members for exceptional contributions to the industry. Submissions in the association’s divisions are reviewed, evaluated and voted upon by the PPI members. PPI is the major North American trade association representing the plastic pipe industry.
Construction
The ongoing construction of the West Campus at the base will add four recruit dormitories, two classrooms, dining facilities and a chapel. The $226 million project is a partnership between Air Force Civil Engineering Center (AFCEC), the U.S. Army Corps of Engineers, the 802nd Civil Engineer Squadron, Merrick and Company and the 737th Training Wing, the largest training wing in the Air Force. Some 1,250 trainees will be assigned to each of the two 280,550 square foot dormitories once the total project is completed in late 2022.
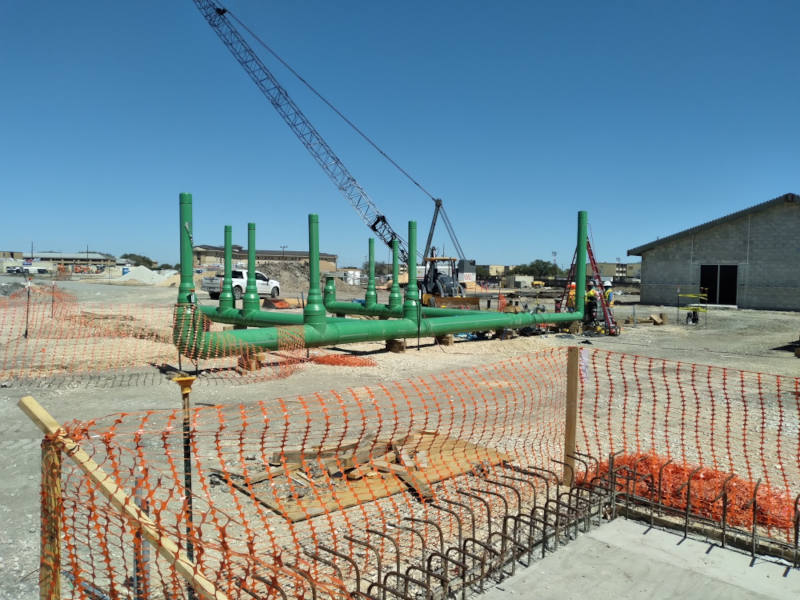
The design called for piping that would range from four through eighteen inches and consist of both SDR 11 and SDR 17 wall thicknesses, and which would accommodate the different requirements of the cold and hot water services and non-potable lines. Plus, potable pipes need to meet NSF requirements for drinking water.
Four to sixteen-inch diameter SDR 17 PP-RCT would be used for plumbing, non-potable, while SDR 11 PP-RCT would be used for HVAC chilled and heating water, condenser water, plus domestic hot water in diameters from four inch to eighteen inch.
Challenges
“Tight places are challenging locations for installing piping systems,” stated Lance MacNevin, P. Eng., director of engineering for PPI’s BCD. “Asahi/ America’s Asahitec PP-RCT pipe would provide light weight, ease-of-maneuverability and would use faster and safer heat fusion welding methods than steel pipe.
Because this pipe is made from random co-polymer polypropylene (PP) with modified crystallinity and temperature resistance, it has a more complex crystalline structure that provides greater pressure capabilities at higher temperatures than conventional PP materials.
PP-RCT piping products are rated for continuous operation at 180ºF (82ºC) temperature, with pressure rating depending on their wall thickness. PP-RCT pipes also may include reinforcement layers for benefits such as reducing longitudinal thermal expansion/contraction. Additionally, the use of PP-RCT piping increases efficiency and long-term maintenance savings. Steel pipes in hydronic systems suffer from the chemical formation of iron oxides, leading to rust and corrosion.
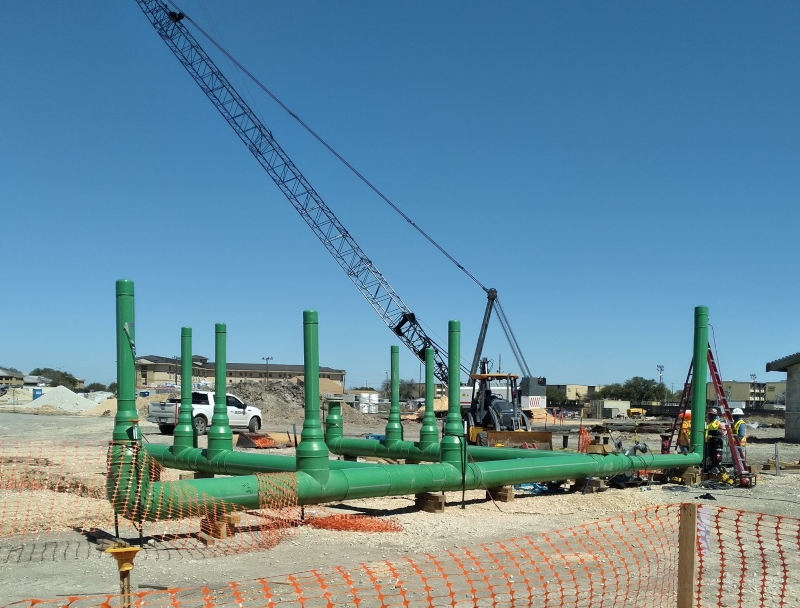
Corrosion build-up can take a toll on the efficiency of pumps needed to distribute water throughout a facility. PP-RCT allows water to move efficiently and operate at higher velocities without corrosion concerns. With the increased performance of a PP-RCT hydronic system, less energy is put into the creation and maintenance of the system, which creates a smaller carbon footprint.”
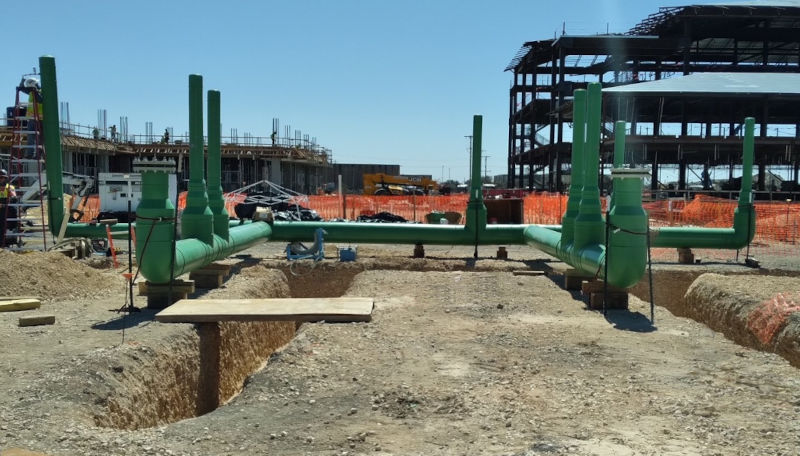
According to Asahi/America, the smooth internal surface of its Asahitec pipe has a Hazen and Williams coefficient of 150.
MacNevin offered, “Although new steel pipe has a Hazen and Williams coefficient of 140, its flow factor and flow characteristics typically change over time due to scaling, rust and pitting. This internal corrosion could reduce the flow coefficient to 110 or 90, resulting in pumps that have to draw more power to overcome growing flow resistance, leading to increased energy usage and decreased efficiency.”
“This is an extensive installation with thousands of feet of piping in buildings and underground,” stated David M. Fink, president of PPI. “The use of Asahitec PP-RCT provided significant peace of mind that major essential campus services at this military base will be trouble-free for decades to come.”
Types of piping
“We’ve been seeing more use of PP-RCT high-temperature plastic pressure piping for plumbing and hydronic heating. PP-RCT pipes also provide resistance to highly acidic and basic solutions, which may be seen in certain non-potable lines. It was perfect for this project. The design engineers knew that a great amount of the pipe would have to be installed in confined spaces and made it a top priority to consider how the crew could handle it it,” concluded Fink.
A six-inch diameter, 20-foot section of carbon steel weighs nearly 400 pounds, which would require special rigging to lift and hangers and support bracing. The PP-RCT is considerably lighter, weighing just 4.5 pounds a foot, or 90 pounds for 20 feet. Being about one quarter of the weight of carbon steel, using PP-RCT pipe made the job a lot easier, practical and safer. PP-RCT provided all the weight savings, installation benefits and performance efficiencies promised by the material characteristics.
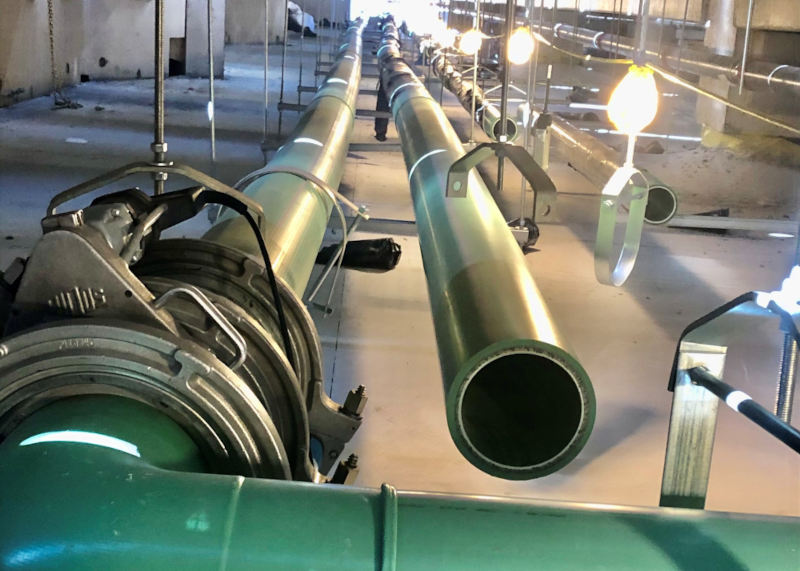
While the light weight of the pipe helped ease the installation underground and in crawl spaces, the fusion process using a hydraulic butt fusion tool to connect pipes and fittings also provided a critical benefit. Using heat fusion joining releases no hazardous fumes or gases, which makes it much safer to use in confined spaces.
Because there are no open flames or combustible gases, using PP-RCT pipe does not require extra permitting tags. The time required to weld Asahitec is also considerably less than that of steel. To weld one 12-inch joint of steel pipe could take up to three hours, while a butt fusion weld of Asahitec takes roughly 41 minutes to complete, according to the company. Because of this, the time and cost savings to both the contractor and the customer were considerable on this project.
Performance
The hydraulic fusion tool served additional functions beyond welding. It acted as a come along for the movement and pressurized fusion of the large pipe, kept weldments in alignment, and the process allowed for continuous operator inspection of the fusion process and final weld.
“The system’s performance will be reliable for decades,” stated MacNevin. “The efficiency of the system will remain as designed, and will not change due to any degradation of the piping system. The base will not have to perform any maintenance on the system, unless outside factors damage it.
“This project provides proof that plastic piping offers all the installation and performance benefits that plastic piping suppliers claim,” he concluded.
The Air Force plans to add two new dormitories, an additional classroom and dining facility and the chapel in the coming years. Once completed, the 1.33 million square foot West Campus will be able to simultaneously train nearly 5,000 recruits.