In oil, gas and chemical processing applications, accurate and reliable temperature measurement is crucial, and is traditionally achieved using thermowells, which have been known to be problematic
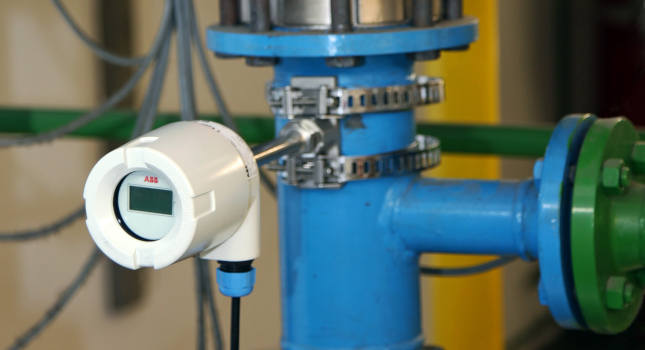
What Is A Thermowell?
Thermowells have been widely used for many years for measuring the temperature of flowing liquids. Essentially a sensor within a protective casing, thermowells are designed to guard the sensor from damage caused by excessive pressure, corrosive materials and high velocity materials.
While thermowell reliability has come a long way, there is a risk that wear could cause a sensor to fail or break. If a thermowell fails and is not detected, the medium temperature could go unmonitored, which can have catastrophic results, and even if detected the process must be shut down to maintain or replace the device.
Thermowells require drilling into the pipe to establish contact between the sensor and the medium. This is problematic, as it can affect the integrity of the pipe, and the reluctance to drill too many holes in pipes places limitations on how many sensors can be used, which can lead to potential blind spots in process data.
Installations can be costly, must be planned far in advance and may require suspension of the process, leading to expensive downtime, as well as a high cost per measurement. This historically has limited the use of temperature as a parameter to gain better process insight across in upstream, midstream and downstream oil and gas processes.
However, a new solution has emerged that allows operators to understand the thermal nature of the material inside the pipe without the need to drill into it and requiring no physical contact between the sensor and the medium. ABB’s TSP-341 noninvasive temperature solution treats the pipe itself as the sensor, taking readings from the surface and then using software to predict the true medium temperature based on variables such as ambient conditions, insulation and process and medium variables like volume, pressure and viscosity (see Figure 1).
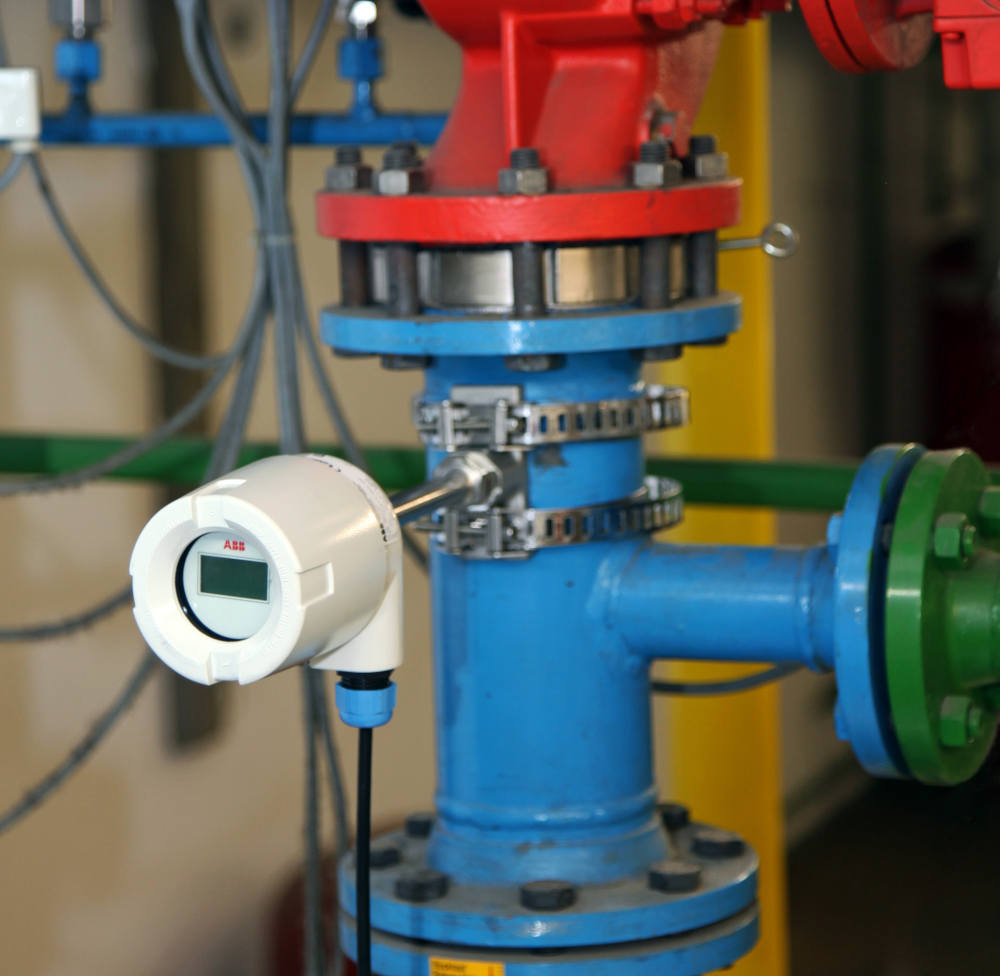
The software interprets the readings from dual sensors — one measuring the temperature of the pipe wall, the other measuring the ambient temperature — and uses the resulting data to calculate and output the process temperature in real time. By taking the ambient conditions during the measurement into account, the transmitter significantly increases the accuracy and the responsiveness of the pipe surface measurement. Coupled with models that predict the range of application of the sensor, i.e., liquid-like processes flowing in the turbulent regime in metal pipes, the performance matches that of a traditional invasive measurement.
Suitable applications
The inherent benefits of the noninvasive temperature transmitter allow it to be used throughout the oil and gas chain with potential applications in upstream, midstream and downstream processes. Oil wellheads are an example of an upstream application ideal for noninvasive temperature measurement. Wellhead applications are three-phase mixtures of sand, gas, oil and water flowing at high speeds, and are thus extremely aggressive. Since noninvasive measurement does not require contact with the medium, the risk of device failure is reduced.
The issues presented by the varying pipe sizes used in a typical oil and gas installation can be addressed by ABB’s noninvasive measurement solution, which attaches to the pipe using straps, enabling one device to cater for every requirement. By overcoming the challenges associated with installing invasive temperature or pressure devices, noninvasive temperature measurement presents an easy and low-cost solution for connecting new or existing wellheads to the digitalized plant in a cost-effective way. Noninvasive means that temperature measurement can be used to complement pressure sensing, helping to discern conditions such as slugging or low flow where dynamic pressure swings are not visible.
Noninvasive measurement can also be used in temperature monitoring for leak detection on midstream oil and gas pipelines, supplying the data needed to factor temperature compensation into leak detection algorithms. Mounting the sensor outside the pipe removes pigging challenges as well as the risk of high-pressure gas leading to sensor failures. A unique advantage of the noninvasive approach is its ability to enable a remote installation without compromising on performance, as the temperature display and transmitter can be located above ground, while measurement insets are mounted underground, where they are protected from ambient conditions.
Monitoring of temperature on heat tracing lines in downstream applications is another application for noninvasive temperature measurement. The small pipelines used for steam tracing are not suited to conventional thermowells and can present a challenge for accurate and responsive temperature measurement.
ABB’s sensor can also be used not only on heat traced piping, but also for monitoring the heat tracing process itself when mounted directly on the process piping to ensure the heat transfer is occurring as it should. Unlike a thermowell, which is only in contact with a specific area of the medium, noninvasive sensors can detect the variances in temperature across the pipe, known as thermal stratification, and give a truer reading of process performance.
Since noninvasive solutions are cheaper to purchase and quicker and simpler to fit, multiple devices can be installed to enhance accuracy across the process and provide validation of existing thermowells and other noninvasive devices across the application. For large piping, for instance in refineries, noninvasive sensing can complement invasive measurements in measuring flow profiles during low flow periods, such as startup and shutdown, giving a truer picture of the temperature profile.
Other applications can include using the sensor to help prevent overheating of flowing product, for instance highly viscous fluids such as heavy oils and lubricants, by monitoring the outlet of pumps for abnormal temperature levels, generally exceeding the performance of in-built pump sensors, while removing the risk of exposing the sensor to viscous and abrasive materials within the pipeline.
Predicting performance
While innovation can prove beneficial in providing new ways of tackling known problems, the perceived uncertainties of using new technologies can also deter engineers from embracing their possibilities. For this reason, ABB has developed an online tool that allows engineers to determine the suitability of using a noninvasive temperature device for an application by allowing them to input process and pipe characteristics to predict its performance.
Part of ABB’s My Measurement Assistant, the web-based tool factors in the influence of flow rate, wall thickness, insulation, wind and thermal conductivity to demonstrate the sensor’s accuracy in different circumstances without the time and costs involved in physically testing a device in a real-life environment. Validation in situ
Noninvasive measurement is also a cost-effective way of checking whether existing thermowells in-situ are accurate. Quick installation and low engineering costs, coupled with eliminating the need for drilling into pipes, means that noninvasive temperature sensors can be used to validate measurements of thermowells and other noninvasive sensors. If the noninvasive sensor handling the measurement is delivering substantially different readings to the other devices, then this may indicate a problem that requires investigation.
Previously, the only way of achieving this would be to install additional thermowells, which has considerable cost implications while potentially affecting the safety and integrity of the process. The more operators can measure, the better they can understand and optimize processes. Noninvasive solutions provide a means of doing so in a cost-effective way without having to shut down or re-engineer the process.
Time to do things differently
While temperature may be one of the oldest process measurements, it doesn’t follow that the way it is measured must stay the same. The conventional justification for maintaining the status quo — based on the argument of “we’ve always done things this way” — is increasingly being challenged by the new possibilities that digitalization is bringing to all areas of industrial measurement.
Advances in temperature measurement technology, particularly when it comes to digitalization, are presenting new opportunities that can benefit most companies operating processes with turbulent flows.
While thermowells still clearly have their place and can present the better solution in certain applications where extremely high accuracy levels and response times are required, noninvasive solutions are ushering in a new era of precise, flexible and low-cost temperature measurement.