Manufacturers come together to develop a better foundry coat.
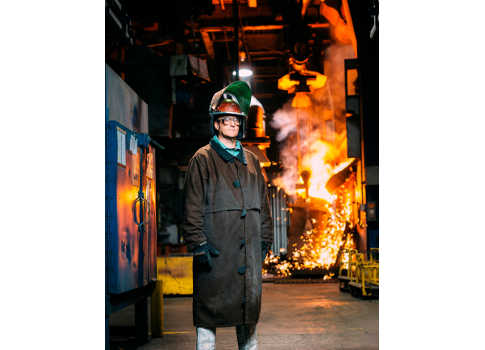
Hope and Crosby. Hall and Oates. Chocolate and peanut butter. The great collaborations in popular culture came about at that hard-to-define intersection of chemistry and serendipity.
So when a company with a fabric that could withstand the searing temperatures of an iron foundry came across a company that wanted a better, more durable way to protect their workers from 2,800 F heat, something called BOGU was born. The workers at Victaulic’s Lehigh Valley foundry in Pennsylvania thought the whole thing was pretty cool—relatively speaking.
Named for the Japanese word for "armor," BOGU’s future success will be determined by the market. The early reviews around this more breathable heat-protective fabric, developed by Toray Fluorofibers in Decatur, Ala., indicate that it has great potential as a barrier against the scorching heat and splash in a foundry.
"It just happened to be good timing. We were developing a fabric, but we didn’t have good direction on how to develop it," said Dung Trieu, general manager at Toray Fluorofibers. "This guy came walking out when they were running some burn tests, and he asked if he could stand around and watch."
"This guy" was Zach Jerrold of Victaulic, who was looking for a better way to protect foundry workers. Their existing aluminum heat suits were effective, but not terribly comfortable, given summer’s ambient heat and humidity added to the foundry heat. Victaulic was looking for something better.
"They were headed down the same path we were," Jerrold said. "The material was not up to par yet, but we kept in contact. They approached us 6 mo later with the fabric." It was a 2-yr process from first concept and first contact to a line of products that may help change the way workers are protected in liquid-metal foundries. It also gave a company such as Victaulic that usually develops product lines for its own customers an interesting look at how solutions for their industry can be developed.
Product development
It’s not as if anyone was surprised that iron foundries are very, very hot and dangerous places, and the workers who toil in them can be exposed to heat and splash from the foundry. For Victaulic, Plant Engineering’s 2014 Top Plant recipient, finding a better solution was part of their corporate reinvention.
"When I first came aboard in 2010, the CEO (John Malloy) gave me several expectations from his perspective that were never lost on me," said Bill D’Amico, Victaulic’s global environmental health and safety director. "He asked how we could drive safety awareness throughout the organization, and he asked how we could leverage technology."
In looking to answer these questions, foundry workers noted the existing aluminum heat suits were usable, but not much more. "Our previous foundry coat was adequate from a protection standpoint, but it was hot, the fabric did not breathe well, and it was difficult to launder," said Jerrold.
When Jerrold and Trieu first met at the University of Alabama-Birmingham’s (UAB) world-class Department of Material Science’s lab, they were both just looking for something, but neither was sure just what that something was. Trieu had the fabric; Jerrold had the need to maker workers more comfortable without sacrificing safety. "People usually are very specific about what they want, and sometimes that’s so limiting," said Trieu. "In the beginning, we kept all the management folks out of it. It was just Zach and I."
There were, of course, some specific requirements. "First and foremost, it had to be comfortable, it had to be durable, it had to be cost-effective," Trieu said. "With these parameters, we created a fabric that we felt would meet the criteria."
The fabric went through the testing at UAB based on ASTM standards. John Griffin, who worked for the Southern Research Institute in Birmingham before that group became part of UAB’s Department of Material Sciences, has been splash-testing fabrics for 25 yr. "It’s not a large project for us, maybe one or two trials a month from different people," Griffin said. "I know most of the people I do testing for. It’s a fairly small community. Most of our work is with pouring iron or aluminum."
Griffin said the lab’s job was focused on the material quality and its characteristics. What people do with the material after it leaves the lab isn’t his focus.
"I’m a testing lab. I run testing as consistently as I can," he said. "I don’t know what happens after, and I don’t want to know. My job is to test in as unbiased a manner as possible."
"We did all the test work at UAB. We tested it multiple times and vetted out any issues," Trieu said. The finished versions were woven and nonwoven polytetrafluoroethylene fabrics, or PTFE. The best-known version of a PTFE is Teflon, another name known for heat resistance. With its final chemistry in place, BOGU was ready to go from a fabric to a garment. And that required one more partner in the process."
Piecing it together
Toray’s strength was fabric development. Victaulic’s strength was foundry work. They needed someone whose strength was garment manufacturing, which brought them to Majestic Fire Apparel in Lehighton, Pa., just 30 mi from Victaulic’s Easton, Pa., headquarters.
"Where we got involved, Victaulic looking for a manufacturer," said Majestic Vice President Jeanane Matula. "They were looking for someone who could manufacture with their specs in mind," said Majestic Vice President Jeanane Matula.. "Typically, all of these suits have all been aluminized, but this is a completely different material. Molten metal just kind of slides off of it, and it’s completely washable, where in aluminized products that’s just not an option. It has both protective value and a much longer life." Victaulic’s employees were directly involved in the on-site testing. "We went through maybe 10 to 15 prototypes over 18 mo," Jerrold said. "We were trying to find a garment just as protective, but more comfortable. And once they are cleaned, they don’t lose shape. These actually perform better after they’ve been washed."
Majestic first manufactured the jacket in three sizes and has worked with Victaulic to develop other accessory items, such as chaps, hoods, and pants. Next up is a line of gloves. The product line is developing, and so is the industry interest. One reason for that, Matula said, is Victaulic involvement in the process at this stage.
"Because of their experience with the material, they’ve really gone the distance to make it known in the industry," she said. "Word has spread, and people can’t help but take note. Everyone is always looking for a better option."
"We will share this advancement with others in the industry in the hopes of advancing foundry safety worldwide and, more importantly, the protection of our most valuable asset—our employees," D’Amico said in a press release announcing the partnership with Toray Fluorofibers and Majestic Fire Apparel.
There is one other factor in the BOGU product. "It’s significantly more expensive," D’Amico said. "But looking at it from a product life perspective, these are lasting three to four times longer than in the past. From my perspective, I don’t see as many replacement orders coming through."
"I was very impressed with their management group," said Trieu of Victaulic. "They saw the data, saw the prototypes around them, and made the decisions on a timely basis. They made a decision and we moved forward."
"They told us it had to be comfortable. They didn’t tell us how it had to be comfortable," Trieu added. "The coat itself is heavier when you put it on, but that feeling goes away quickly. When Victaulic first came out to us, they said they wanted the guys to want to wear it. It’s as simple as that."