Modernization may be an alternative to the common repair vs. replace choices
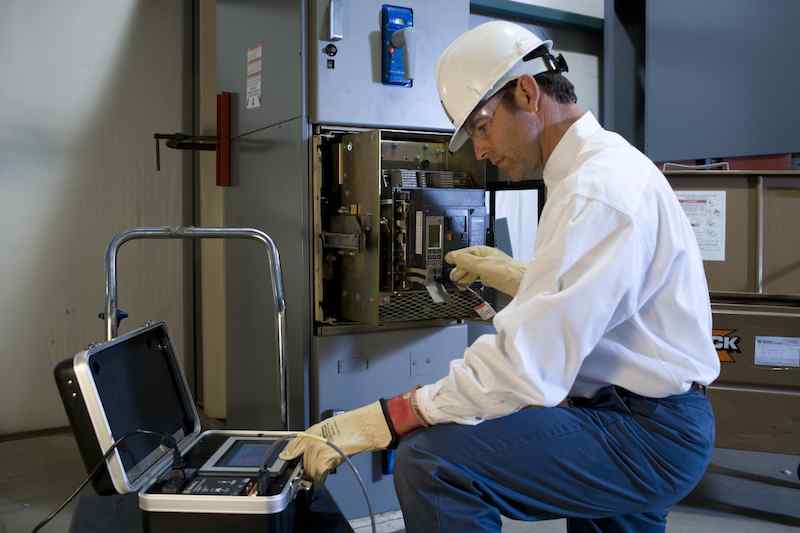
Electrical switchgear has two types of components that make up the system, which can be referred to as passive and active. The passive components consist of such things as the steel framing channels, cover plates, barriers, horizontal and vertical bus structures, as well as components that make up the mechanical structure of the equipment. The critical active components are the power circuit breakers or fused devices that comprise the overcurrent protective system.
Generally speaking, 20 years has been the traditional useful life expectancy for electrical power distribution equipment that has been maintained according to the electrical manufacturer’s recommendations. Of course, there are numerous installations of equipment that have been in operation for well over 20 years. In many of these cases, the equipment may appear to be working, but there are operational issues that need to be addressed.
Even with annual preventive maintenance, there may be instances where the life span is shortened. Factors to consider include the operating environment and the availability of spare parts. But there are ways not only to extend, but also to optimize the useful life of the equipment.
Myth #1: When switchgear problems arise, the only options are to maintain the aging equipment or replace it with new equipment.
When faced with the repair versus replace dilemma, facility managers may now opt to modernize the existing switchgear lineup. As previously stated, both passive and active components require routine preventive maintenance to help optimize equipment reliability. As a rule, the passive components have a longer life than the active components as their structure is typically less complex.
So, why replace the entire structure when problems arise? A more cost feasible alternative would be to leave the switchgear structure and bussing in place and upgrade the active components with the latest state-of-the-art circuit breakers.
Direct replacement and retrofill modernization solutions are available for adapting the latest technology circuit breakers into a switchgear or switchboard. These solutions are available to replace a variety of low-voltage and medium-voltage OEM circuit breakers. Both options are designed to improve reliability, reduce maintenance, and increase equipment capabilities.
- Direct replacement: Via an adaptor cradle, direct replacement circuit breakers are designed to fit into the existing switchgear cubicle with little-to-no modification to the switchgear cell. Direct replacement solutions reduce downtime since there is minimal (if any) outage on the equipment bus.
- Retrofill: The existing switchgear cell and bus are reconfigured to accept the new circuit breaker. This option requires a longer bus outage since the internal cell is being modified.
For both the direct replacement and retrofill modernization solutions, new cubicle doors are provided to match the existing equipment and new circuit breaker face. Designs are available for any manufacturer’s switchgear.
The benefits of upgrading include:
- Improved reliability: Dash-pot style or air break interrupting devices on existing circuit breakers may have reliability issues, and aging materials reduce equipment reliability.
- Reduced maintenance costs: Older power circuit breakers require periodic maintenance and overhaul, which is expensive and time-consuming, and many components for existing circuit breakers are no longer supported.
- Increased capabilities: Fault current interruption, trip unit accuracy and repeatability, arc flash limiting circuit breaker availability, and power metering, monitoring and communication availability.
Myth #2: The cost is too high.
If replacing the existing switchgear, there are a number of costs to consider in addition to the purchase price of the new equipment, such as:
- The cost of demolition and removal of the existing switchgear lineup equipment and the associated contractor labor hours.
- The potential disruption to the facility’s processes and workflow during the course of changing out the equipment. Unless process loads can be rerouted temporarily during the demolition of old equipment and installation of the new equipment, the cost of lost production can be substantial.
- An often overlooked consideration is conduit placement. Installing new switchgear (which is usually smaller than the older/obsolete equipment it is designed to replace) requires that existing conduit above and below the equipment be moved. As such, the cables may have to be spliced or replaced, also adding to the cost.
A direct replacement or retrofill solution minimizes these expenses. There is no demolition of the existing lineup. The disruption to production is minimized, and may even be reduced to the time to rack out the old circuit breakers and rack in the new direct replacement units.
The modernization solutions eliminate the time-consuming, expensive task of moving conduits and replacing cables because the footprint of the existing equipment remains intact. Cables do not need to be touched, eliminating the possibility of damage.
Myth #3: If the equipment is modified, the UL mark will be void.
The UL mark indicates the OEM product left the factory complying with industry adopted levels of safety and performance, generally the applicable UL standard and the NEC. Modification of the equipment does not necessarily void the UL mark. Many products are designed to be modified in the field, such as cutting holes for conduit entry.
It is the responsibility of the authority having jurisdiction to assess the acceptability of the field modifications or to determine if they are significant enough to require one of UL’s Field Engineering Services staff to evaluate the modified product. It is not possible for UL to confirm that the product continues to meet the applicable certification safety requirements unless the field modifications are specifically investigated by UL. For a fee, UL will perform a field inspection of the newly installed circuit breaker(s) and field certify the equipment.
Electrical equipment and power distribution systems have never been designed to be or intended to remain perpetually energized without interaction by the owner. Depending on when the switchgear was installed and how it has been utilized, the equipment may be in a condition somewhere between satisfactory performance and nonfunctional. The latter usually occurs as equipment approaches the end of its expected design life. If maintenance has not been regularly performed, this less-than-satisfactory condition may be entered prematurely, and a shortened useful life of the components may be the result.
While the direct replacement and retrofill options are two different modernization solutions, they provide the same end result: improved power system reliability and lower lifecycle costs.
Key Points
- Among the factors to consider when reviewing the lifecycle of switchgear are the operating environment and the availability of spare parts.
- The benefits of upgrading switchgear include improved reliability, reduced maintenance costs and increased capabilities.
- Modification of the equipment does not necessarily void the UL mark. In fact, for a fee, equipment and be recertified after modification.