In the second of three parts, John Ross examines OSHA's 14 elements from their National Emphasis Program (NEP)
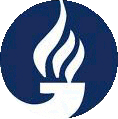
In the first part of our series looking at OSHA’s Process Safety Management (PSM), and specifically the National Emphasis Program (NEP), in the March issue of Plant Engineering, we learned the history and purpose of both PSM and NEP.
Horrific and catastrophic incidents were occurring around the world as a result of unintended releases of highly hazardous chemicals (HHCs). To stem the nature and effect of these accidents, the Department of Labor, through its OSHA agency, initiated PSM in 1992 and NEP for refineries in 2007. A few short years after that, riding on the success of the refinery NEP, OSHA initiated a CHEMNEP (Chemical National Emphasis Program) to lay a level of oversight on the other HHC facilities, in line with what was accomplished in the petroleum industry.
It should come as no surprise that the readiness of the petroleum industry, and now the industries that work with or produce other HHCs, weren’t really “ready” for the level of inspection that OSHA was going to bring. If the physical nature of the work to be demonstrated was adequate, the documentation was most likely missing or not ready for inspection. There was a lot of work to do around the country for HHC-related companies to improve on the management of their processes; and there still remains a good bit of work to be accomplished.
To review from part 1, OSHA’s NEP inspectors will review your programs and processes around 14 major elements:
Here in part 2, we are going to discuss all 14 elements in detail and examine how maintenance is affected.
1. Employee participation
The employee participation element is perhaps the one with the shortest number of mandates, but with one of the largest impacts. Right from CFR 1910.119, “Employers shall develop a written plan of action regarding the implementation of the employee participation….” The stated intent of this element is for employees, production, maintenance, and staff to be involved in all aspects of the PSM program at your site, and to have representation in the development, discussion, and eventual solution to issues around the process hazard analysis.
Simply put, your employees need to know what’s going on that might affect their safety. Your employee participation program must be written and all meetings well documented.
Here is a question from the 100 “static” questions list that was developed for the refinery NEP: “Does the employer’s written employee participation plan-of-action (see document request XLE.3.e) include information on how employees will be consulted on the development of ALL PSM standard elements?”
As mentioned in part 1, the situation isn’t that facilities don’t have written processes; in fact, many of the companies dealing with HHCs have these written programs but just fail to execute them as written. Employee participation is a process that has to be thought out, and followed as written, to ensure that the workers have a clear and documented path of communication for these important PSM discussions.
Maintenance has a significant impact under this element because it has such a significant impact on the success of the PSM effort. Maintenance technicians are involved in the complex task of testing and repairing the production equipment, and their well-being is on the line with every turn of the wrench. When any aspect of the system involving HHCs is involved, maintenance must be involved in the discussion. This process of including maintenance (and operators) must be documented and followed, with an extensively objective, evidence-laden path.
2. Process safety information
This element contains one of the most highly concentrated, maintenance-specific listings of all the elements. CFR 1910.119 states our obligation as maintenance leaders very clearly: “the employer shall complete a compilation of written process safety information before conducting any process safety hazard analysis required by the standard.
The compilation of written process safety information is to enable the employer and the employees involved in operating the process to identify and understand the hazards posed by those processes involving highly hazardous chemicals. This process safety information shall include information pertaining to the hazards of the highly hazardous chemicals used or produced by the process, information pertaining to the technology of the process, and information pertaining to the equipment in the process.”
In this text, “operators” includes maintenance insomuch as maintenance works on and around the HHCs. The CFR text above indicates that your MSDS (material safety data sheets) information needs to be accessible and current, as do your P&IDs, component information listing, electrical classification, ventilation systems, and safe operating limits, and much, much more. This is a very intense element.
It should be obvious what the impact on maintenance is in regard to the PSI element. Our maintenance technicians have to have access to and understand all the technical data around our production systems, including the component particulars and information on the hazards of the HHC involved.
3. Process hazard analysis (PHA)
This element is extremely technical in nature and includes a comprehensive what-if evaluation. The CFR reads, “The process hazard analysis shall be appropriate to the complexity of the process and shall identify, evaluate, and control the hazards involved in the process.” In this element engineers and maintenance leaders hone their Failure Mode and Effects Analysis (FMEA) skills, as well as exploring the consequence of failure. This process analysis will be conducted as a team and includes a review of the facility siting for possible hazards.
The PHA really affords a tremendous opportunity to get both operators and maintenance technicians involved. In fact, the standard requires this team has both “engineering and process operations” expertise. The team makeup also includes at least one person “who has experience and knowledge specific to the process being evaluated.” Additionally, there has to be one person on the team that is “Knowledgeable in the specific process hazard analysis methodology being used.”
After an initial PHA is conducted, the process hazard analysis is required to be updated and revalidated by a team no less than every five years.
4. Operating procedures
At first blush it might not seem that there would be a maintenance impact under the heading of operating procedures, but this element has a few items of interest.
Startups following a turnaround, and after an emergency shutdown is included in this element has a control measure to be taken if physical contact or airborne exposure occurs. If you’ve ever been at a plant during an emergency shutdown or a release, then you can attest to the fact that maintenance is heavily involved in addressing the situation.
5. Training
This element does specifically address the needs for those operating a process. To be sure, though, maintenance technicians need to be fully trained for all the functions they are performing, and that training needs to have been accomplished through a competent source and very well documented.
6. Contractors
There are a lot of opportunities in this element to trip up an otherwise healthy and well-executed maintenance strategy. Contractors are perhaps unfairly known to do what they can get away with to get a job done. Under the auspices of PSM-NEP, there are some very unforgiving rules: “The employer, when electing a contractor, shall obtain and evaluate information regarding the contract employer’s safety performance and programs. The employer shall inform contract employers of the known potential fire, explosion, or toxic release hazards related to the contractor’s work and the process.” This element continues with other very hefty requirements.
The need to document and cross-reference information, and further document meetings, discussions, etc., with contractors is vital to successfully addressing this element. Many times the supervision of a contractor will fall under the office of the maintenance manager; the impact on plant maintenance should be obvious for this fact.
7. Pre-startup safety review
This element and the element on management of change are closely tied together as the safe and effective management of this process lies squarely with plant maintenance and engineering.
The standard requires that “The employer shall perform a pre-startup safety review for new facilities and for modified facilities when the modification is significant enough to require a change in the process safety information.” The phrase “Change in the process safety information” could literally mean a change in a single component. This is a very detailed requirement and one that cannot, and most certainly should not be taken lightly.
8. Mechanical integrity
Along with the process hazard analysis, MI, or Mechanical Integrity inspections are required on a periodic time frame and must be well documented. Systems requiring this periodic inspection are: Pressure vessels and storage tanks, piping systems, relief and vent systems and devices, pumps, controls, etc.
A very important concept comes into play in this element. Not only do the people doing the inspections have to be properly and officially trained in what to look for and how to conduct the inspections, but inspections and testing procedures need to follow “recognized and generally accepted good engineering practices,” RAGAGEP. This is a catchall phrase that is intended to tie the practices of your maintenance technicians back to some accepted OEM, trade, or company doctrine. The layperson’s question would be, “Who told your guy to do it like that?” This is a seriously simple question, but one that has to be answered in a very deliberate way.
9. Hot Work Permit
This is such a simple element, but it is so easy to violate if maintenance supervision and technicians become complacent. Aside from the inclusion of work completed by contractors that requires hot work permits, there is a great chance that the plant assigned resources could get this wrong.
“The employer shall issue a hot work permit for hot work operations conducted on or near a covered process.” Simple enough? What does “or near a covered process” mean? How “near” is near?
Also, the permit has to document that the fire prevention and protection requirements in 29 CFR 1910.252(a) have been implemented. This has to be documented, but prior to all that, we have to train our personnel on the requirement and how to verify the aspects they are responsible for, as well has how to post and file these permits.
10. Management of change
“The employer shall establish and implement written procedures to manage changes (except for “replacements in kind”) to process chemicals, technology, equipment, and procedures; and, changes to facilities that affect a covered process.” The following considerations are addressed prior to any change:
- The technical basis for the proposed change
- Impact of change on safety and health
- Modifications to operating procedures
- Necessary time period for the change
- Authorization requirements for the proposed change.
Many organizations choose to issue an MOC for every change, regardless of whether or not it is a replacement in kind, just to get around any potential errors in this element. There are many details, and questions that maintenance and engineering have to answer satisfactorily to make this a safe process.
11. Incident investigation
This is another element where the language could be a potential tripping point for maintenance as well as operators. The standard calls for an investigation into all incidents that result in, or could reasonably have resulted in, a catastrophic release of HHCs. The ambiguity of the phrasing makes it almost necessary to include all incidents around HHCs to be classified as at least meeting the lesser criteria. Maintenance and engineering leaders must shore up their what-if scenarios in the PHAs to guard against even the slightest incident.
12. Emergency planning and response
Like most emergency situations at plants all across the country, any emergency planning and response actions will include maintenance resources. This particular element requires employers to establish and implement an emergency action plan, including a plan to handle small releases.
13. Compliance audits
This element is redundant of the actions required by other elements in the PSM-NEP. Once again, the standard requires that “Employers shall certify that they have evaluated compliance with the provisions of this section at least every three years to verify that the procedures and practices developed under the standard are adequate and are being followed.”
This element continues to state the requirement that the audits will be conducted by at least one person knowledgeable in the process. Also noted in the standard is a requirement to retain the last two most recent audit reports.
Maintenance personnel will quite often be called into service to be on the audit teams.
14. Trade secrets
This element was a late add-in element published to acknowledge that until now, some companies kept process information secret from their own employees under the guise of proprietary information, in essence protecting their trade secrets.
Maintenance personnel are typically involved in all aspects of the process but might be lacking in the knowledge of the details of production. Operations and maintenance employees have the expressed right, under this element, to be made aware of those secretive processes that might affect the health and safety of the employees.
This completes a review of the 14 elements that make up the PSM-NEP line of inquiry with a brief explanation of how maintenance and others are affected by the individual elements. Of course, there is more information available on these elements and each organization has to be prepared to successfully question its own abilities and those of federal or state auditors.
The intent of this program is to ensure that we perform our processes in a manner that is consistent with safety in all operations, engineering, and maintenance tasks that are conducted involving HHCs.
See more from Marshall Institute’s blog on Plant Engineering’s website.