Every day that your operation stalls is a day that you're leaving potential profits on the table.
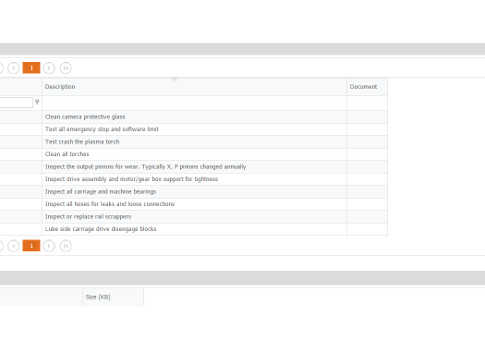
For most organizations, the No. 1 goal in the grand scheme of things is to maintain business continuity. Every day that your operation stalls is a day that you’re leaving potential profits on the table. It’s clearly vital to keep business humming along as efficiently as possible at all times.
This is why the threats of shutdowns and outages continue to be so worrisome for business leaders. The C-Suite works tirelessly to devise business plans that will ensure steadily flowing profits, but those plans are contingent upon staying in operation without any unforeseen delays. When those delays do happen, they can be devastating to production, deliveries, costs and more.
It’s important to manage these incidents to whatever extent is possible. Even a short window of downtime for such an operation can have massive ripple effects on an industry at large. So what can be done about shutdowns and outages?
It helps first to understand the issue.
The nature of the shutdown issue
The basic problem is that when one element of your process shuts down, it tends to have a ripple effect on everything else you do. Joel Levitt, director of international projects at Life Cycle Engineering, emphasized this in his book, "Managing Maintenance Shutdowns and Outages." Levitt explained that a shutdown can have a major deleterious effect on your workflow.
"Project work in general and shutdowns in particular are in conflict with just about everything else going on at any time," Levitt wrote. "If the advantages were not so great, shutdowns would never occur. Projects involving shutdowns of major equipment are expensive in … costs (money for labor and parts) and lost production."
Methodologies applied to unplanned events can involve reviewing work order backlogs, pulling in preventive maintenance activities, ascertaining labor and material availability and so forth. The costs of the shutdown—i.e., the materials and labor needed to repair what’s not working-play only a partial role in the impact of these types of shutdowns. Much more significant are the opportunity costs you incur by not staying up and running.
The "forced vs. planned" distinction
Of course, there are different types of shutdowns to consider—some are more justified than others. At a typical manufacturing facility, you can divide such incidents into planned shutdowns and forced ones.
Delays are planned for any number of reasons including routine maintenance tasks and "pilot runs" to experiment with your process. In these situations, you can prepare well for the planned delay and survive unscathed. Unplanned delays, however, can be a major roadblock to productivity. If and when they happen, you may have to make the best use of the time.
Mastering project-management techniques
When shutdowns do happen, they can be disastrous for business. The good news is you can manage crises effectively if you know a few basics of project management.
For example, if you have a set of procedures in place to respond to shutdowns and outages, it’s easier to spring into action and respond quickly. It’s good to make sure everyone knows in advance which individual tasks will be assigned to them, and where those tasks may be found—such as through email notifications, a dashboard view, or within the preventive maintenance (PM) function of your modern computerized maintenance management system (CMMS). An inspection should include the litany of steps needed to perform the procedure properly. These PM tasks can be fairly comprehensive, involving images or specs, labor assignments, associated parts and assets, estimated costs and hours and more.
It’s best to have a contingency plan in place as well. While you certainly want to take into account fire or weather-related emergencies, you also want to review the handling of internal service failures, such as chemical spills. Ensure that these plans are uploaded to your CMMS’ document management for quick reference or are already configured as a task for fast work order generation.
Finally, measurement is a necessary road to improvement. David Berger of Plant Services magazine writes that typical performance metrics cover the following:
- Project management (lower shutdown costs as compared with previous years)
- Customer satisfaction (higher quality of output after related problems are identified and eliminated)
- Operational capability (increased equipment reliability through failure analysis)
- Risk management (decreased lost-time injuries).
– This article originally appeared on Smartware Group’s blog. Smartware Group is a CFE Media content partner. Edited by Erin Dunne, production coordinator, CFE Media, [email protected].