Frost & Sullivan study finds maintenance improvement can drive greater profitability.
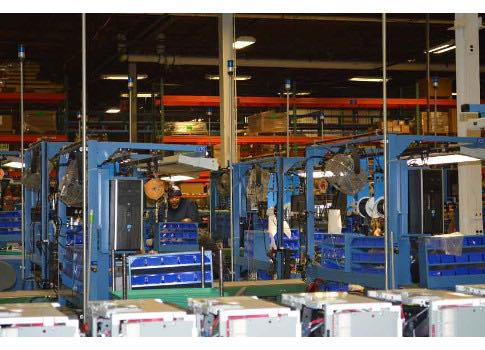
The emergence of Industrial Internet of Things (IIoT) as a plant strategy has focused on productivity and operational issues. One area of great potential, and one area that often gets overlooked, is maintenance. A recent study by global consultancy Frost & Sullivan talked about the relationship between IIoT and maintenance. The study found that service strategies will shift from corrective to preventive and predictive maintenance services over the next five years.
"Effective utilization of predictive analytics can optimize costs and eliminate unplanned downtime, which are highly attractive benefits for manufacturers," Frost & Sullivan officials reported. "Big data analytics is poised to change the maintenance services models across the manufacturing sector. The investments for establishment of robust maintenance and support service model by leveraging the big data analytic concepts is the critical factor for the high growth rate."
Report author Srikanth Shivaswamy, senior research analyst for industrial automation and process control for Frost & Sullivan, discussed the ways IIoT will impact the maintenance area.
CFE Media: One of the hottest topics around IIoT is the potential for better maintenance within plants. Has maintenance been overlooked by most plant managers? How will IIoT potentially change that?
Shivaswamy: Conventional maintenance systems followed pre-set approaches for maintenance and repairs; service activities were performed according to pre-design standard operating procedure. Maintenance and repair operations were initiated based on equipment or process flow breakdown.
Internet of Industrial things would see the emergence of scheduled and automatic maintenance and repairs activities generated by pre-programmed algorithms.
- Dynamic maintenance schedules can be generated based on real-time data by sensors.
- Ability to migrate to a completely different service model to adjust to a new process/ product /solution and improve the overall performance of the end-user.
- Flexibility to scale up and down the services capabilities.
CFE: Will this increase in data also change the training and skill set needed for maintenance workers? What are the challenges and opportunities here?
Shivaswamy: The skill set of the maintenance workers need to be tuned to understand the dynamic service models. In most cases the maintenance workers needs to be trained to understand and operate the IIoT based platform.
Challenges and opportunities:
- Development of smart and user-friendly platforms for data management
- Asset and resource management modules
- Standard service and maintenance models
- Use of off the shelf mobile devices
- Development of integrated cloud platforms to execute design, maintenance, and business services.
CFE: It appears that there will be more companies providing third-party services in both maintenance management and cyber-security. What do you see as the pros and cons to such an approach?
Shivaswamy: The increase in number niche companies can be attributed to the emergence of industries data services and cyber security services. The lack robust software platform in the industrial space has been seen as a lucrative opportunity by most of the niche companies.This would witness the upcoming of innovative platforms to increase the utilization of products, equipment and assets. Lack for standardization across software platforms has been the major concern for data cross-flow and integration.
CFE: What is the first thing plant managers should do to prepare for IIoT in their facilities?
Shivaswamy: Information technology and communication infrastructure in the most of the plants needs to be improved for complete implementation of IIoT modules.