Encouraged feedback and team empowerment allows a team to take ownership of a continuous improvement effort. Four tips for encouraging employees are highlighted.
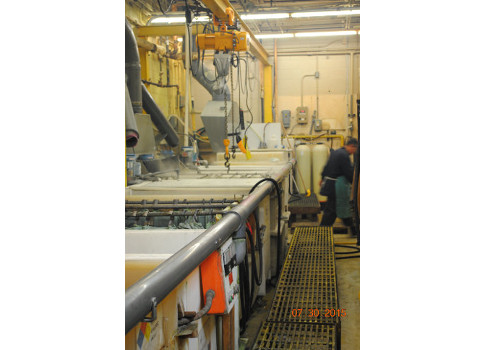
Today, the biggest challenge in most organizations is maintaining their competitive edge while demonstrating their ability to make relevant improvements on a regular and consistent basis to their customers. To successfully meet these challenges, requires or demands change.
Everyone from the boardroom to the production floor have a difficult time overcoming the fear of change. As a result, efforts to continuously improve are stalled right from the beginning. Fear of failure also factors into this dynamic because no one wants to make a mistake or look bad. Innovation can’t come from a controlled situation. Delegating or forcing the issue through the workforce cannot create it. It comes from spontaneity and chaos.
If any effort directed towards continuous improvement or innovation to succeed, employees must feel that their suggestions are genuinely wanted and encouraged. They must willingly take ownership in the future of their organization – continuous improvement is everyone’s responsibility.
Every employee can launch simple initiatives to create an environment where the focus on continuous improvement happens every day. Examples include:
1. Study game films approach. Every important project is reflected upon regardless of the outcome. Based on the outcome, what needs to be known? If a similar project is acquired, what should be the first course of action? What should be stopped or done more of? This simple process insures something is learned from every event. Most employees know what they must do, when to do it, and how to do it. Many do not know why they do it, who they do it for, and where it fits in to the total picture. Being armed with the why, who, and where helps them identify and suggest ways to improve what they do.
2. Meetings should be conducted on a regular basis to actively solicit feedback on how work is produced – the first question should be based off of the one thing that can be done today to produce a better result tomorrow. The same approach should be taken with better customers. They have a lot to offer so long as they are asked and shown their feedback is important.
3. Don’t let the potential for mistakes or failure deter innovation. There will always be rough times. The team should be shown that everyone’s actions and mistakes are part of business and offer an excellent opportunity to learn how to do things better.
4. A meeting should be scheduled each week to evaluate important strategic issues. Even 1 or 2 of these meetings would be beneficial each month to identify and act on tasks that support continuous improvement.
"What’s one thing that could be done better?" is a question that should be asked at every staff meeting. This encourages feedback and empowers team members to take ownership in the continuous improvement effort.
-Chris Ruisi is a leadership and motivational business speaker and an author for AME. This article originally appeared on AME’s blog. AME is a CFE Media content partner.