New study points to the value of exceeding regulatory guidelines
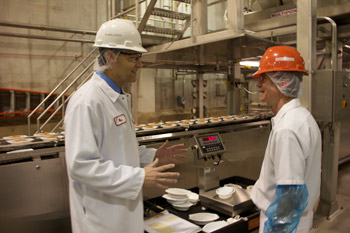
The Food Safety Modernization Act (FSMA) will go into effect this year, and a new study discusses the concept that regulatory compliance can be a benefit not just to the consumers, but also to the manufacturers. As Frost & Sullivan prepares to release its new white paper, “Achieving Value Beyond Compliance: How the Food and Beverage Industry Extracts Value by Working with the Top 25 Best-in-Class Companies,” their Industrial Automation & Process Control practice in Mountain View, Cal., responded to questions from Plant Engineering about its findings and how food and beverage manufacturers actually can benefit from the new rules:
Plant Engineering: As you look at the Top 25 Best In Class Companies, what characteristics do they have in common? What specific things make them best in class?
Frost & Sullivan: These companies provide not just the means to be compliant, but value beyond compliance. They pioneer industry best practices. They work on driving customer value and continuous customer engagement. They are solutions-focused, and bring excellent problem solving capabilities to bear. They are able to connect the dots between customer pain points and their solutions, and in the process create measurable benefits to users.
PE: Talk in general about the idea of compliance vs. productivity. What is the parallel between being compliant and being profitable, especially in the F&B industry?
F&S: There is a general misconception that compliance hinders productivity; that it is counterproductive to productivity, slowing down processes, creating inefficiencies. It can actually drive productivity in ways of improved yield, better ‘first time right’ processes, fewer recalls.
In the case of a pump, a typical pump has a seal, a component which is infamous for creating potential product contamination. There is constant servicing associated with this unit. By switching to a seal-less pump you are compliant but, but also accruing other benefits including reduced maintenance, increased uptime, etc. So, there is improved productivity as one benefit.
PE: In contrast, what are the barriers to compliance for those laggard companies? What keeps an F&B manufacturer from being more productive, and this more profitable?
F&S: We estimate that 50% of the market could currently be characterized as laggard. They typically buy for compliance on a reactive basis, because they see compliance as a cost center, not a profit center. They don’t have the larger vision of value. They tend not to partner with best solution providers, relying on piece-part procurement methods of keeping the process going. They lack education on best-in-class solutions, and don’t have a clear road map vision of where they want to be in five to seven years.
PE: Let’s talk about some of the specific components. On the pumps and motors side, what are the implications of FSMA, and what are some areas a plant manager should be aware of in order to improve compliance and performance?
FSMA has a specific rule on Preventive Controls for Human Food focuses on Hazard Analysis and Risk-Based Preventive Controls (HARPC). There is a mandate to ensure that process controls focus on ensuring Physical, biological and chemical hazards are avoided. Pumps are being increasingly focused on by FDA inspectors to ensure sanitary conditions.
Many applications in F&B industry such as chocolate processing use gear or a progressive cavity pumps. As these are considered unsanitary due to the fact that there are dead spots inside the pump and that metal scrap or rust from the pumps can contaminate, end-users are encouraged to increase their maintenance schedule or replace them with a lobe pump.
Similarly, motors used in conveyors and process equipment need to be cleaned often. Use of washdown servo motors and electric motors reduces maintenance time and increases equipment uptime.
PE: Automation clearly is a huge opportunity in this industry. What are the ways automation should be utilized to achieve compliance and productivity?
F&S: The food and beverage industry is a goldmine of opportunity from an automation controls and software standpoint. The industry, by itself, is very forward looking and eager to adopt new technologies like wireless, mobility, cloud, workflow automation, etc. However, the current state of the industry shows islands of automation with poor or weak integration between them.
In order to drive nimbleness, agility and flexibility in the operational ecosystem, automation is the only answer that ties the different facets together. Automation has the capability to mitigate the trade-off between achieving compliance and productivity.
Clearly, control-loop mechanisms ensure precise recipe control, batch management which drives compliance to regulations. Moreover, the biggest interaction to be seen in the industry will be between operational assets and informational assets. This bi-directional flow of information will open up tremendous amounts of opportunities for the end user, as they can possibly have a single window view of all KPI’s across an enterprise.
Automation helps in standardization of systems and continues to influence end-users in executing things differently rather than doing different things.
PE: Let’s also talk about sustainability. How will FSMA impact energy and sustainability issues and what steps should manufacturers take to meet these goals?
F&S: Sustainability factors into what we call our S3 framework for defining value beyond compliance. S3 stands for safety, security, and sustainability and all are key areas of focus for not just FSMA compliance, but for achieving next-gen production levels in the industry. Basically, to comply, companies will have to adopt GMP, in which energy efficiency is an important component.
Imagine if the entire industry addressed this component; that would create a significant difference in energy profile, carbon footprint, etc. We often hear that the industry is more focused on uptime, equipment reliability and repeatability, etc., and that energy efficiency takes a back seat to these issues. But as plants become more and more integrated, and production metrics are integrated with other business metrics, businesses will address energy efficiency and sustainability overall as a corporate measure, and one of the biggest places an F&B enterprise can make strides in increased sustainability is in better optimizing production. There are various methods to get on this path, including plant walkthroughs to understand high energy consumption points, and understanding the automation components that will enable transitions from energy consumption to energy conservation.
PE: Are there other points you’d like to make about FSMA and its impact on manufacturing?
F&S: A vision of robust consumer safety could be realized if there is immersive connectivity within the four walls of a food and beverage plant, to ensure that good quality and safe products were made, and that any deviation from that would be immediately recognized, and acted upon – it is building an information network in plant will escalate deviations to right decision maker in real time. This creates an enterprise that is extremely agile, flexible and nimble.
Replication of these practices across other plants across an enterprise would create an agile network of manufacturing facilities. This is definitely the direction manufacturing in general is going, and a direction F&B needs to embrace.