A well-managed obsolescence management system safeguards a company from the aforementioned issues. Here are seven steps in using the system to predict equipment lifecycle.
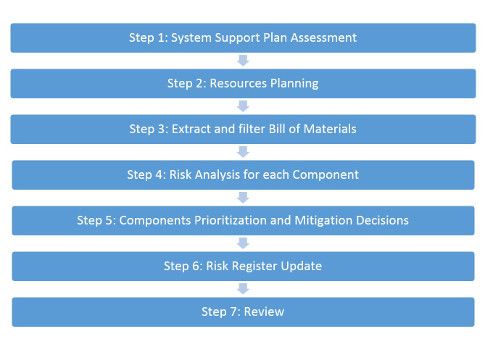
Companies worldwide receive thousands of product change notifications (PCNs) and end-of-life (EOL) notifications daily. What could be the possible consequences of these notifications? Can we assess the risks involved in a delayed response when handling obsolescence?
Obsolescence can be simply put as the transition from availability from the original manufacturer to unavailability. Immediately after the information about discontinuation has been announced from its Original manufacturer, obsolescence of a product starts. This is usually done by a product discontinuance notice (PDN) or a message about the EOL. Also an announcement for a life-time-buy (LTB) or a PCN could be the start of obsolescence.
Reasons for obsolescence occurrence include market change, technological evolution and environmental policies & restrictions. It is very common that a situation of market change can lead to a decrease in demand for older products such that the economic production is not feasible. Similarly, a newly developed generation of technology renders the old one obsolete and sometimes these new technologies are often cheaper to produce than their predecessors. In some cases, old technologies are completely displaced by new ones. Moreover, government and other interest groups intervene with legal regulations and restrictions. Failure in compliance with environmental policies can lead to product obsolescence.
The financial impacts of obsolete components are quite high for the end-user especially when a redesign is necessary and costs not only incur for engineering services, but also for operating capital or testing equipment. The costs of repeated obsolescence intervention throughout the system’s life largely exceeds the incremental costs associated with an obsolescence management strategy.
Following should be taken into account when designing obsolescence management strategy:
- All components of every system shall be designed in full accordance with the relevant codes and standards applicable.
- The obsolescence management strategy shall be defined and communicated throughout the company.
- The obsolescence management process shall be subject to regular reviews to make ensure that the strategies and processes remain fully applicable and effective.
To prevent these risks of obsolescence following three management strategies are established:
Reactive obsolescence management
Reactive obsolescence management is the instruction to deal with obsolescent components after receipt of EOL notice. The following solutions are used to mitigate the risk of obsolescence:
- Reclamation or cannibalization of parts
- Finding alternate (fit, form and function) replacement from the same or a different manufacturer
- Finding nearest equivalent substitute part, to reduce the redesign cost
- Costly ‘last time buys’ (LTB) or ‘Die Banking’. Buying the components in bulk and store them in inventory for future needs.
Proactive obsolescence management
For critical components that have a high risk of going obsolete, proactive management is implemented.
Benefits of using proactive obsolescence management include:
- Early warning of component discontinuance (end of life) allows maximum time to react and avoids to choose costly resolutions
- Corrective action options at the component level can be taken while low cost opportunities still exist.
- Evaluation of end of life notices and part change notifications (PCNs).
Strategic obsolescence management
This is a long-term strategy that considers technology forecasting and long-term business case planning and development.
For proactive obsolescence planning, the aim is to categorize all the parts out of the Bill of Materials (BoM) in a systematic scheme and treat them in different ways. In general, seven steps are required.
Step 1: System support plan assessment
The first step is to identify the period when each component in the BoM is required and how long necessary supply parts should be available.
Step 2: Resource planning
For the second step, the available resources that can be allocated to the project are identified. The items with the highest risk of obsolescence should be supported by most of the available resources.
Step 3: Extract and filter bill of materials
Next, get a BoM with the low risk components filtered to reduce the workload. This complete risk assessment will figure out high and low risk potentials in detail for each component in the mentioned BoM.
Step 4: Risk analysis for each component
Now the risk of each component in the mentioned BoM should be assessed according to the risks of getting obsolete. Therefore is it essential to consider the following two criteria:
- Probability that the component becomes obsolete
- Impact of the obsolete component on the system.
Step 5: Components prioritization and mitigations decisions
Here it is important to find systematic ways to treat very high, high, medium and low potentials of obsolescence. very high obsolescence risk are those items that should be permanently treated and strategies should be deployed to reduce the risk that obsolescence occurs. For high obsolescence risk items the obsolescence manager has to decide how these items should be treated. In many cases the same treatment as for very high obsolescence risk will be used. For medium obsolescence risk the components a frequent check of parts with medium obsolescence risk seems to be enough. In low obsolescence risk category it is advised to implement a reactive treatment. Reactive treatment is cost effective for this category.
Step 6: Risk register update
All the data which have been collected in correspondence with the appropriate treatments have to be noted down in a risk register. This register must be frequently updated to ensure the best mitigation of obsolescence.
The following information should be provided for each part of the BoM:
- Status (obsolete or not)
- Period in which the component should be available
- Details about the risk level
- Next planned steps if the part is obsolete.
Step 7: Review
Periodically, the assessment needs to be reviewed and updated if necessary. The obsolescence manager has to decide when this must happen and the corresponding responsibilities have to be assigned.
A well-managed obsolescence management system safeguards a company from the aforementioned issues. Obsolescence is inevitable and hence cannot be avoided, but careful planning can help us reduce its impact. It must be managed as an integral part of design, production and service support in order to minimize the financial and availability impact throughout the product life cycle.
– Ali Awais Amin is a design & application engineer at Intech Process Automation, a system integrator and automation solution provider for the oil & gas sector globally. Intech Process Automation is a CFE Media content partner. Edited by Joy Chang, digital project manager, CFE Media, [email protected].