Scaffolding companies can assist plant managers through scheduled outages safely and efficiently while remaining productive.
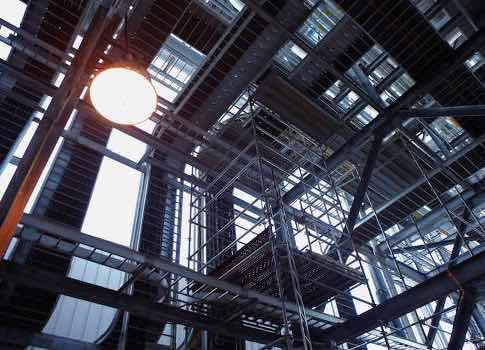
In modern scaffolding operations, the use of improved communication, precise planning, and innovative project management techniques has enabled crews to achieve more efficient results with a leaner, more specialized workforce in a safer environment. Through ongoing educational programs, personnel-specific planning, and a holistic implementation approach, scaffolding companies can provide all-inclusive solutions with reduced overhead and fewer modifications.
This modern approach is a significant departure from the traditional mindset of simply assigning more bodies to perform a larger job. By working smart, scaffolding companies can assist plant managers who are working through scheduled outages by safely and efficiently achieving the highest level of productivity possible.
Construction techniques
Typically, plant scaffolding companies schedule maintenance work during outage season, allowing the plant to operate uninterrupted through the busy months. With this in mind, modern construction techniques have been developed to assist plant managers in meeting their outage needs by creating the safest and most efficient work environment.
In the past, the concept of assigning more bodies to get a job done was the most common approach. This focus made scaffolding operations less efficient by ignoring the concept of a specialized workforce. Scaffolding jobs require a variety of focused titles, including millwrights, carpenters, ironworkers, boilermakers, pipefitters, and supervisors.
Each worker should be assigned a specific task in their area of expertise. Before this idea became more common, the entire crew would work on the same task to get one job done. This system is now antiquated, and those who still embrace it on a regular basis are shutting themselves off from an opportunity to learn more effective methods of operation.
Newly developed construction methods are heavily focused on planning and safety. Precise planning allows plant managers to look at all aspects of a project beforehand so they can use every available resource. When planning a scaffolding operation, contractors should ask plant managers questions about the types of scaffolds needed, capacity limits, planking requirements, guardrail qualifications, supportive equipment needs, safety provisions, and the type of personnel needed for the job.
Additional planning requires the inspection of a scaffold to ensure the safety measures are met for the user. This includes checking for secure footing, guardrails, toeboards, cross braces, poles and legs, and more. Once all the construction requirements are met, scaffolding operations can begin.
With a need to yield better results with fewer resources, scaffolding companies have turned to comprehensive planning as part of a holistic approach to achieving the best outcome. It is part of a scaffolding company’s responsibilities to ensure that a power plant’s applicable reliability standards developed by the North American Electric Reliability Corp. (NERC) are in accordance with the Federal Power Act.
Established to evaluate and improve the reliability of power plants, NERC annually assesses seasonal and long-term reliability, monitors the power plant through system awareness, and educates, trains, and certifies industry personnel. This all-inclusive preparation performed by scaffolding companies allows power plants to meet and maintain scaffolding operation procedures during the construction period while ensuring that risks are properly managed. Scaffolding companies can deliver higher-quality results to their customers if these standards are addressed in planning meetings before the work is performed.
Ongoing education
One innovative project management technique being used by modern scaffolding companies is providing ongoing educational programs for employees. It is important for scaffolding companies to proactively send key personnel to project management workshops, providing consistent education in organized leadership for foremen to meet union requirements. Scaffolding contractors should constantly update their educational programs to expose their employees to new ideas.
Lean manufacturing is designed to optimize workflow and use scaffolding employees’ full skillsets. Many benefits come from the lean process including preventing waste to reduce costs, achieving faster delivery, and improving the quality of service. By using this method, scaffolding companies and power plant managers will see an improvement in overall results at the lowest possible cost. Producing a useful, versatile, and effective educational approach enables scaffolding companies to provide high-quality service to their customers.
Communication
It is vital for scaffolding companies to communicate with power plant managers throughout the job process. Improved communication starts with pre-outage meetings to help planners capture all of the project details and set appropriate budgets. Information gathered from a pre-outage meeting improves planning and sets a foundation for all functions of the scaffolding operation.
Many specifics vary from job to job, including power plant measurements, scaffolding configurations, and supportive elements that reinforce the scaffold. Scaffolding managers can use personnel-specific planning by mapping out the placement of each scaffold, assigning appropriate workers and determining the type of scaffold needed for each job. These decisions are imperative to scaffolding operations achieving a successful, well-planned plant shutdown.
As a result of improved communication, scaffolding companies and plant managers are able to reduce modifications and cut overall cost. Time is valuable, and specialized work is necessary to complete a job on time and within budget. Therefore, an open line of communication during pre-outage meetings and scheduled outages is necessary to ensure satisfying results for power plant managers.
Putting theory into practice
Safe, efficient scaffolding operations can achieve the highest level of productivity by working smart with the use of correct job preparation. Scaffolding companies need to be thoroughly prepared for power plant outages to execute a job successfully. This includes thoroughly communicating with power plant managers, inspecting the scaffold and job site for safety regulations, assigning a specialized workforce for each job, complying with reliability standards, and offering educational programs to employees.
Each of these aspects should be combined into a holistic implementation approach that enables scaffolding companies to successfully work through scheduled outages and provide all-inclusive solutions for power plants.
Jim Ryan is the general manager for StructSure Scaffold & Insulation, a St. Louis-based specialty scaffolding and insulation contractor with more than three decades of experience.