Performing an annual infrared (IR) scan helps secure assets and also prevents downtime and disastrous equipment.
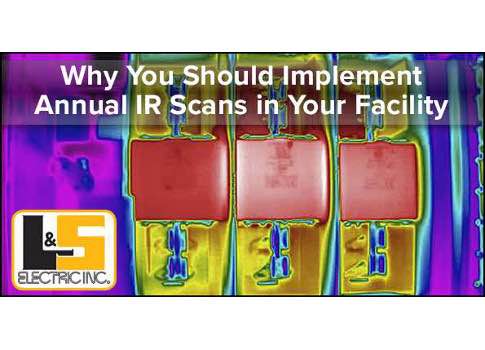
Maximizing uptime needs to be the main goal in running a business in this tough global economy. Performing an annual infrared (IR) scan should be a major part of a company’s predictive maintenance program. An IR scan helps secure assets and also prevents downtime and disastrous equipment. An IR scan program administered by a professional helps in identify potential failures in an electrical system, utility supplies, and fired equipment in the facility.
IR scan basics
Any object emits heat or thermal energy. The energy released from that object gets hotter. Over time, the infrared radiation from that object becomes more intense. The human eye cannot detect this radiation so it helps to use an IR scan, which is designed to detect, capture an image, and measure the radiation present in areas emitting an abnormal temperature.
Advanced features in IR cameras provide you with detailed pictures that show the heat signature of the equipment. Excessive temperatures in components show possible issues such as corrosion, imbalance, or overload. After interpreting the thermal profile, it is easy to make an accurate reading of the condition of the equipment. Then, provide recommendations after analyzing the cause of the problem.
An IR electrical scan locates hot spots from defects in components and connections. IR scans, it is possible to find sections exposed to excess heat due to increased resistance. This way, it becomes easier to determine the presence of a potential issue before complete failure. IR scans also prevent safety hazards and loss of productivity. All these factors impact your business.
Benefits of IR scans
Based on the insurance industry’s loss statistics and analysis, over 30 percent of fire losses are due to electrical issues. Even if electrical failures do not create large fires, damages to your equipment may still arise. These incidents all contribute to a reduction in your productivity resulting in long-term customer loss.
So, many insurance companies require businesses to conduct an IR scan on an annual basis. If you consider how this process reduces the chances of damages to the facility, equipment, and personnel, you may end up paying lower premiums. Conditions detected by this form of maintenance task include:
- Overloads
- Defective equipment
- Inductive heating
- Open circuits
- Loose connections
- Harmonics.
NFPA recommendations for IR scans
According to the National Fire Protection Association (NFPA), IR scans to aid in preventing losses due to excessive heat in the facility leading to fires. The NFPA recommends that business owners conduct a routine IR scan of electrical systems on an annual basis. Aside from minimizing chances of losses, IR scans can prolong the life of the equipment.
Since an increase in temperature by at least 10 ºC shortens the life of a motor, an even higher amount of heat leads to greater damages. The chances of these temperature spikes make it even more necessary to schedule IR surveys to locate problems before they start. These programs prevent production issues, unplanned downtime, and massive energy consumption.
IR scans are extensive tests that determine the condition of your equipment without interrupting normal operations. These scans take place while the plant is in operation and the equipment is at full load. There is also no contact made on the target object. If the equipment is in a hazardous location, the scan takes place at a safe distance.
The professional conducting the IR scan prepares a report after completing the survey, which provides context to the scanned equipment, including:
- The location and qualities of the equipment tested
- The particular item with a thermal abnormality
- Any increase in temperature present
- Severity of the condition
- The color thermogram
- The potential cause and suggested solutions to the problem.
An annual IR scan performed enhances the efficiency of your equipment by pinpointing electrical problems at their early stage. Since there are no disruptions during the test, you continue with your normal business operations while preventing expensive and unexpected shutdowns of your systems.
David Manney is a marketing administrator at L&S Electric. This article originally appeared on L&S Electric Watts New Blog. L&S Electric is a CFE Media content partner.