Make your company’s electrical safety program NFPA 70E-compliant by following eight best practices to make sure that the electrical safety programs drives the development of safety habits.
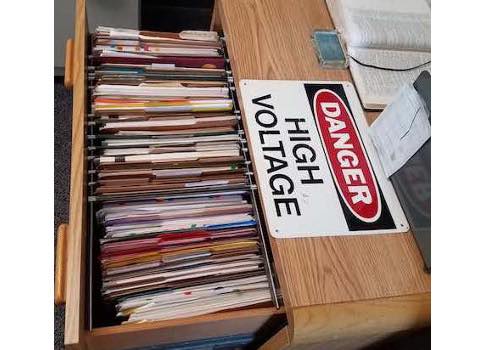
The 2015 edition of the National Fire Protection Association (NFPA) 70E standard requires employers to implement and document an overall electrical safety program. Sometimes it may feel cumbersome to try to understand and comply with OSHA-mandated industry standards, but when they are broken down and looked at piece by piece, it can become a very obtainable reality.
The general requirement is for the safety program to direct activity appropriate to the risk associated with electrical hazards and to be integrated with the employer’s overall occupational health and safety management system. While NFPA 70E requirements can be broken out into eight pieces, it is important to point out that training is the thread that runs through the entire program.
Training, in one form or another, is an important aspect of all eight pieces that make up an NFPA 70E-compliant electrical safety program. We often hear the saying "knowledge is power," and when it comes to electrical safety, knowledge should be the priority.
1. Awareness and self-discipline
The overall electrical safety program should be designed in a manner that consistently increases the employee’s awareness of the electrical hazard as well as the mitigation techniques available to provide protection from those hazards. The program should also encourage the development of self-discipline in using the safety principles and controls that are an integral part of the application portion of the program.
Essentially, the electrical safety program should drive the development of safety habits that, in turn, shape an overall culture of electrical safety. This is the first of the eight pieces, because all of the other pieces have to be incorporated with this awareness and self-discipline to successfully create the desired electrical safety culture.
2. Principles
Employers are required to document the key aspects of their expectation for employee safety with respect to electrical hazards. One very important 70E-driven aspect would be the principle of always working on electrical equipment when it is de-energized unless it is not feasible to do so. Hazard identification and mitigation is another key principle in any electrical safety program. Other principles could include:
- Knowledge of the installation, operation, and maintenance of equipment
- Planning jobs
- Documented task instructions
- Personal protective equipment (PPE)
- Proper use of the right tool for the job
- Using qualified workers for the job.
No matter what list of principles the employer comes up with, the key to this piece is training employees to what these principles are and what they mean with respect to the employer’s expectation.
3. Controls
The employer needs to have a documented method for how the program is put into application by the employees. As with the other pieces, employee training and knowledge is the key. The employer must train employees to be qualified at the appropriate level with respect to the hazards to which the employees will be exposed. It is also typical for the employer to develop a process that will drive best work practices and the development of safety habits.
These controls should be built upon the principles in the second piece: What can be done to ensure that the principles are applied to each task? The principle of only working on de-energized equipment is applied through a process that requires the development of an electrically safe work condition. If it is not feasible to work on de-energized equipment, then the control becomes a process that establishes the appropriate boundaries and PPE.
4. Procedures
The controls that are required in the third piece often manifest themselves as written procedures. Other procedures could include the task requirements that describe the details of the work that is to be accomplished. All electrical tasks are planned, and that information should be documented: required PPE, hazard identification, applicable safety procedures, lockout/tag out, boundary identification, energized electrical work permit, drawings, operations and maintenance (O&M) manuals, sketches, photographs, etc.
The program identifies when specific procedures are required, recommended, and—in some cases—not required. These procedures provide the documentation of the steps taken to provide a safe method to execute the associated task.
5. Risk assessment
This piece of the program has been the subject of change for each revision since the 2004 edition. The 2015 edition brought a significant change of specifically requiring three aspects to what is now called the Risk Assessment Procedure:
- Identify hazards
- Assess risks
- Implement risk control according to a hierarchy of methods.
This hierarchy of risk-control methods is specified in ANSI/AIHA Z10, American National Standard for Occupational Health and Safety Management Systems. The hierarchy is as follows:
- Elimination
- Substitution
- Engineering controls
- Awareness
- Administrative controls
- PPE.
The risk assessment for electrical tasks must be documented and include the hazards, risks, and the method used to protect employees from the hazards. This is often documented in a type of job-safety analysis, briefing checklist, or similar document. Moving toward the risk terminology is an effort found throughout the NFPA 70E 2015 revision that addresses probability along with the severity of the hazard.
6. Job briefing
Before any task involving a potential electrical hazard begins, a qualified person leading the task must conduct a job briefing with the employees involved. Interestingly, the 2015 revision removed the distinction between repetitive task, similar task, and routine work. All tasks are treated equally with respect to the job-briefing requirement.
The job briefing should identify the hazards as well as any other related interfaces. Questions that any employees involved might have related to the job should be resolved during the job briefing. The briefing should ensure that all employees involved understand their tasks and how they might impact or be impacted by other tasks being executed.
The group should think through and discuss the whole job from start to finish to confirm their execution plan and identify any gaps. All job-related documentation should be reviewed and discussed. One very important aspect of the job briefing is preparing for an emergency. If work is being performed around an electrical hazard, the source of the electrical energy should be identified along with the next upstream disconnecting device, location, and PPE required to safely operate that device and remove power.
7. Maintenance
This piece was added to the 2015 revision of NFPA 70E. Updates made throughout the 2015 revision bring a heightened awareness of the relationship between maintenance and probability of failure. It is logical to make the connection that equipment that is inadequately maintained will have a higher probability of failing, resulting in an arc flash hazard and/or shock hazard. Therefore, employers are required to make maintenance practices a part of their overall safety program and hazard-risk assessment.
8. Safety auditing
The employer who cares enough for their employees to put together a safety program for employees’ well-being should also care enough to verify that the program is being applied to the work. A lot of time and effort goes into developing this electrical safety program, and it is only effective if the employees understand it and apply it every day to every task. There are two types of audits that the employer is required to perform.
The first audit is on the program itself and is required at a frequency not to exceed three years. It is no coincidence that NFPA 70E is revised on a 3-year cycle. This allows the electrical safety program to be revised to line up with the latest 70E revision. The employer is also required to conduct and document field audits to verify the program is being applied by the employees. These field audits are to be performed at intervals not to exceed 1 year.
Knowledge gained from appropriate training is the key factor that will make or break a company’s electrical safety program. Knowledge of the NFPA 70E standard and the hazards it is designed to safeguard us from is certainly helpful in the establishment of an effective electrical safety program, but it is not the only thing needed for success.
When electrical workers truly understand the hazards they are faced with and the mitigation techniques that are available, their self-preservation instinct will drive them to work safely. It is through this understanding of the hazard and safe work practices that the safety program is able to truly mature into an effective safety culture.
The NFPA 70E requirements simply summarize the requirements in a manner to ensure nothing is being overlooked. If the employer’s motivation is for workers to go home safely to their loved ones each day, then the intent of the requirements of NFPA 70E may already be followed. The only thing left to do is verify it, document it, and audit it.
Tommy Northcott is president of Northcott Consulting LLC and specializes in electrical safety training and NFPA 70E and OSHA compliance. He is a professional engineer licensed in the state of Tennessee and a certified maintenance and reliability professional.