Selecting a new plant site can be a difficult process. To ensure you make the right decision, follow these five rules to keep things on track.
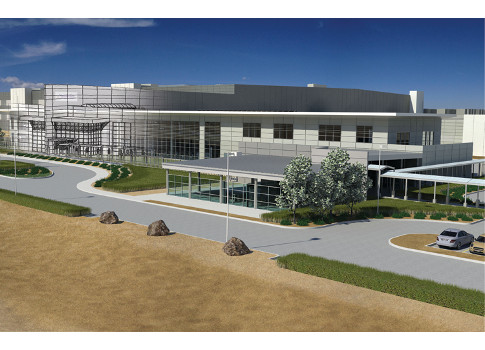
Earlier this year, Food Processing magazine’s Kevin T. Higgins claimed that being a food manufacturer was the next best thing to being a king. Why? Because most new plant projects and renovations are now supported by generous, multimillion public subsidies. But while communities dangle expensive bait in hopes of catching job creation, it’s skewing the site-selection process, resulting in plants built in unfit locations.
While these high financial contributions are certainly positive for the industry, it’s crucial that these deals are mutually beneficial. You have to be sure that the site will meet your plant’s needs and business plan before cashing any checks.
A sound business plan should be the foundation of your site-selection process. The first step is to detail facts include:
The goods the plant will produce
The quantity of goods the plant will produce
Five years of production planning
Future growth expectations
Defining these facts is key because they impact various aspects of a site ranging from size requirements to energy availability. Based on your business plan, first check to see if your organization even needs a new site. Perhaps optimizing current facilities can help you reach your goals. If your organization does require an entirely new plant, here are five factors to consider that will help keep you on track during your site-selection process:
1. Local geography
A site may require additional land depending on local conditions such as topography, drainage or governmental regulation. Don’t forget to investigate these factors.
2. Daily operations
How much traffic will be within your plant and how often? Consider activities such as raw ingredient delivery, finished product distribution and the facility’s internal material movement. Ask yourself additional questions such as, "Will the plant’s operations require rail access?" or "Is interstate accessibility high priority?" Aim to answer these early on in your site selection process to help clearly define the logistics of your new plant.
3. Utility and water costs
Determine the square footage you will require, and use a utility matrix to estimate its utility requirements. If your organization has built similar facilities, project these items based on existing data. If not, consider consulting with an experienced engineering firm.
Utility and water costs go hand-in-hand with your operations costs. When selecting a site, ensure an adequate energy supply source is readily available. Review your water and wastewater requirements. Water consumption costs are heavily influenced by wastewater pre-treatment costs or additional wastewater surcharges. Having estimates of these costs can help qualify your prospective sites.
4. Distance
Identify the location of your customers and distribution centers. Where are your raw materials located? Pinpointing these can help determine the ideal location of your new plant.
Keep transportation costs in mind, as well. Understand that costs vary between inbound material and outbound product. Your organization should strive to minimize the total transportation cost over simply minimizing the mileage between customers, materials and your plant. However, if you have a major customer that demands quick product delivery from your new plant, that should outweigh all other factors, so select a site located at a distance matching that need.
5. Environmental issues
This is a crucial consideration for food processing plants. Examine nearby industrial sites. Do they emit dust? Is there air pollution? What about odors? Noxious or toxic elements? If the site is contaminated, it’s absolutely not suitable for a food processing facility. These issues are typically covered in a Phase I environmental assessment, usually orchestrated by a consultant.
Jim Hale is a senior civil engineer, he has more than 30 years of experience in project engineering and project management. He has worked on projects for Tropicana, Nestlé, General Mills, Boar’s Head Provisions and many others. This article originally appeared on Stellar Food for Thoughts. Stellar is a CFE Media content partner. Edited by Joy Chang, digital project manager, CFE Media, [email protected]