Keep an ear out for leaks, but look at other factors as well.
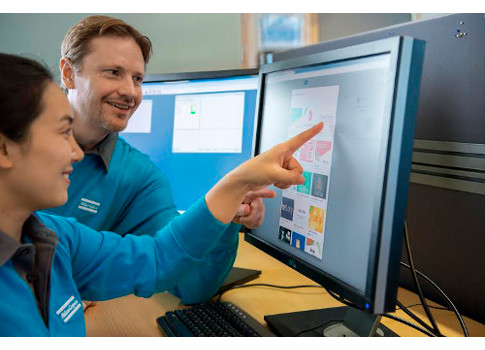
Compressed air is a necessity in many industrial applications, but it can be costly if you’re not careful. By investing some time and thought into your compressed air system, you can identify inefficiencies that, when fixed, will make compressed air an affordable solution.
Here are 10 tips that will lower your compressed air costs.
1. Analyze air consumption
Typically, only half of generated compressed air is used for the intended process. The other half is depleted by artificial demand, inappropriate use and leaks. Artificial demand is created when there are extra margins on sizing compressed air systems in terms of flow or pressure requirement. It can account for about 10% to 15% of compressed air consumption, which translates into wasted money.
You also should check your operation for potentially inappropriate uses of compressed air such as open blowing, personnel cooling, cabinet cooling or air motors. Some of these applications, including cabinet cooling, liquid agitation or stirring and vacuum generation, can be served more efficiently by a fan, blower or vacuum pump, all of which consume less energy than air compressors. Knowing where your air goes is the first step toward developing an action plan to reduce unnecessary compressed air consumption.
2. Inspect distribution
Inspecting your distribution means checking for leaks and assessing your pipe sizing. Both leaks and incorrectly sized pipes can result in unwanted pressure drops, causing your compressed air system to work harder and consume more energy. In some systems, leaks account for 20% to 30% of air consumption. Let’s take a look at some calculations and examples to understand the impact of distribution inefficiencies.
Leaks: At 80 psig, a leak through a 1/16-inch hole consumes about 5.24 cfm. When the pressure moves to 125 psig, that number jumps to 7.66 cfm. This 46% increase in wasted air can compound energy costs quickly, so leaks should be identified and addressed as quickly as possible.
While some larger leaks can be heard in a system walk, an audit is the best way to ensure all leaks are found. Ultrasonic leak detectors are available to find minute leaks, but an ongoing identification program involving all personnel is the most effective practice.
Pipe sizing and configuration:Â Pipe sizing may seem like a small factor, but it can have a big impact on pressure. For example, suppose a plant experiencing low pressure generates 400 cfm while running at 100 psig with pipes that are two inches in diameter. To compensate for the low pressure, the operator considers purchasing a new, larger compressor. Is this a good solution? Probably not. Increasing the pipe size from two inches to three inches and creating a closed-loop system reduced the pressure drop from 12 psi to 1 psi without a new compressor. Another way to avoid air pressure drops associated with piping and configuration is to just say no to long hoses. Minimizing the use of hoses and frequently inspecting fittings can preserve line pressure without forcing the compressor to work harder than necessary.
3. Reduce pressure
It’s common to find systems running at a high pressure to satisfy the needs of only one point of use. However, this can waste large volumes of compressed air, especially when the pressure needs of different end uses are highly disparate. To avoid generating unnecessary amounts of compressed air, try using a separate compressor or booster. That way, the rest of your system can continue to operate at a lower pressure, reducing leakage and usage rates and ultimately decreasing overall energy consumption.
These savings can add up. Every additional 2 psi increases energy costs by about 1%. But before you buy a separate compressor, try a few simple checks:
- Assess the validity of compressor control settings.
- Look for pressure drops through dryers, filters and piping systems.
- Determine if you have artificial demand.
4. Ensure air receivers are used properly
Air receiver sizing and placement are crucial to lowering compressed air costs. Air receivers play a vital role in the compressed air process. They store compressed air prior to end use and serve as a buffer between the compressor and system, modulating pressure variation that may happen during compression.
The Compressed Air and Gas Institute (CAGI) recommends four to five gallons per cfm. For installation with multiple compressors, the air receiver should be based on the size of the trim compressor.
Ensuring your air receiver is in the right location is another way to lower your compressed air costs. Some operators decide to install an air receiver before the compressed air dryer. This can be beneficial to the dryer, as the receiver may provide radiant cooling that removes some of the condensate and entrained oil. However, the receiver will be filled with saturated air. If there is a sudden demand that exceeds the compressor and dryer capacity rating, the dryer can become overloaded, leading to a higher pressure dew point.
Installing the receiver after the dryer doesn’t provide the same advantages, but it does store clean, dry air. Any sudden demand occurring in this situation will be met with dry air. The best proactive air receiver placement is to have two receivers on the supply side: one “wet” receiver before the dryer to provide control storage and condensate dropout and a second “dry” air receiver to meet sudden demand.
5. Control multiple compressor systems effectively
When designing a multiple compressor system, a good way to save money is to base load as many compressors as possible. Multiple compressor control can optimize the running cost because you are selecting which compressor to run at a specific load based on plant flow demand.
It can also reduce the compressor operating pressure band (remember, 2 psi increases the energy consumption by 1%). If you have VSD and a centrifugal compressor in the system, multiple compressor controls will keep the VSD compressor and centrifugal compressor in an optimum zone, minimizing compressed air blow-off.
6. Choose the right dryer and filter
The process of drying compressed air is often misunderstood, which results in inefficiently pieced together systems that waste energy and money. We often get questions regarding dryer and filter selection, such as:
- Should I get a desiccant or refrigerant dryer?
- What level of filtration do I need?
- Do I need all these filters, regulators and lubricants?
Regardless of the question, the answer is almost always the same: it depends on your application. However, there are a few universal tips to follow when using dryers and filters that can help reduce compressed air costs:
- Do not dry compressed air more than the application requires. This is unnecessary and wastes money.
- Consider initial drying with a refrigerant-type dryer, then dry further only to meet point-of-use requirements.
- Every filter causes a pressure drop, which costs money. Don’t filter more than necessary.
7. Remove condensate with no-loss drains
Compressors make a lot of water. You need a way to safely and efficiently remove it from your system to avoid turning your compressed air pipes into water pipes. Manual drains should not be used, because they rely on a maintenance team who may have other priorities.
When left open, manual drains can waste expensive amounts of compressed air.
Timer drains present a similar issue, and both types of drains may not work properly on a humid day.
Instead, opt for drain traps that sense the presence of condensate and drain it without the loss of compressed air. You should always inspect drain traps regularly and repair as needed.
8. Recover heat
Heat is always a byproduct of air compression. In fact, you can recover almost 90% to 95% of heat from certain compressors. A radiator-cooled unit can provide air for space heating in a building, and a water-cooled unit can produce hot water for plant use. Instead of directing hot compressor outside or discarding the hot water, use these resources to power your facility to save money.
9. Measure and monitor air use
Keeping track of your compressed air consumption can offer important insights. From informing maintenance practices to prompting energy saving initiatives, it’s always good to know what’s happening in your system. Doing so will not only prevent serious issues from going unnoticed, it will also help your plant find ways to continuously improve efficiency.
There are seven important things to keep in mind regarding monitoring:
- Establish a baseline of your system before making any changes.
- Establish a benchmark of energy consumption against rate of production.
- Record any system changes and resulting energy savings.
- Record maintenance data and trends.
- Record operating pressures at strategic points in the system, as these changes can reveal problem areas.
- Review the impact of new production machines.
- Analyze low pressure at point of use; this could signal a system problem rather than a need for a new compressor.
Mapping your system is a helpful starting point. This could be done by plant personnel or through a compressed air audit. The latter can offer deeper insights into the system’s functionality and reveal changes that would improve the current system. Another way to keep an eye on your compressors is through a remote monitoring system, which can show where compressed air is going, where pressure drops occur and how much energy the system is using.
10. Select the right compressor
Selecting the right compressor for your operation is paramount. While there are many options, it’s important to understand the different types of compressors and the cost advantages they offer. Every technology has its unique advantage based on the plant demand and application.
- VSD: Because it adjusts to meet demand, this compressor is good for trim applications.
- Oil-free: Oil-free compressors are ideal for sensitive applications like food, beverage and pharmaceutical processing.
- Centrifugal: These dynamic compressors are large and produce high flows, making them good base load compressors for large production industries, such as semiconductor production.
- Piston: Piston compressors are frequently small and portable, making them perfect for automotive and other shop applications.
Don’t purchase a compressor without first researching which best fits your application, pressure and capacity needs. Examining your options up front will save you money down the line.
These tips are just the beginning. Implementing energy and cost-saving practices takes time and ongoing commitment. By adhering to the above practices, your facility can save significant amounts of energy-and money.
-Deepak Vetal is product marketing manager for Atlas Copco Compressors.